Before the Drywall Dries: The evolution of construction starts from within
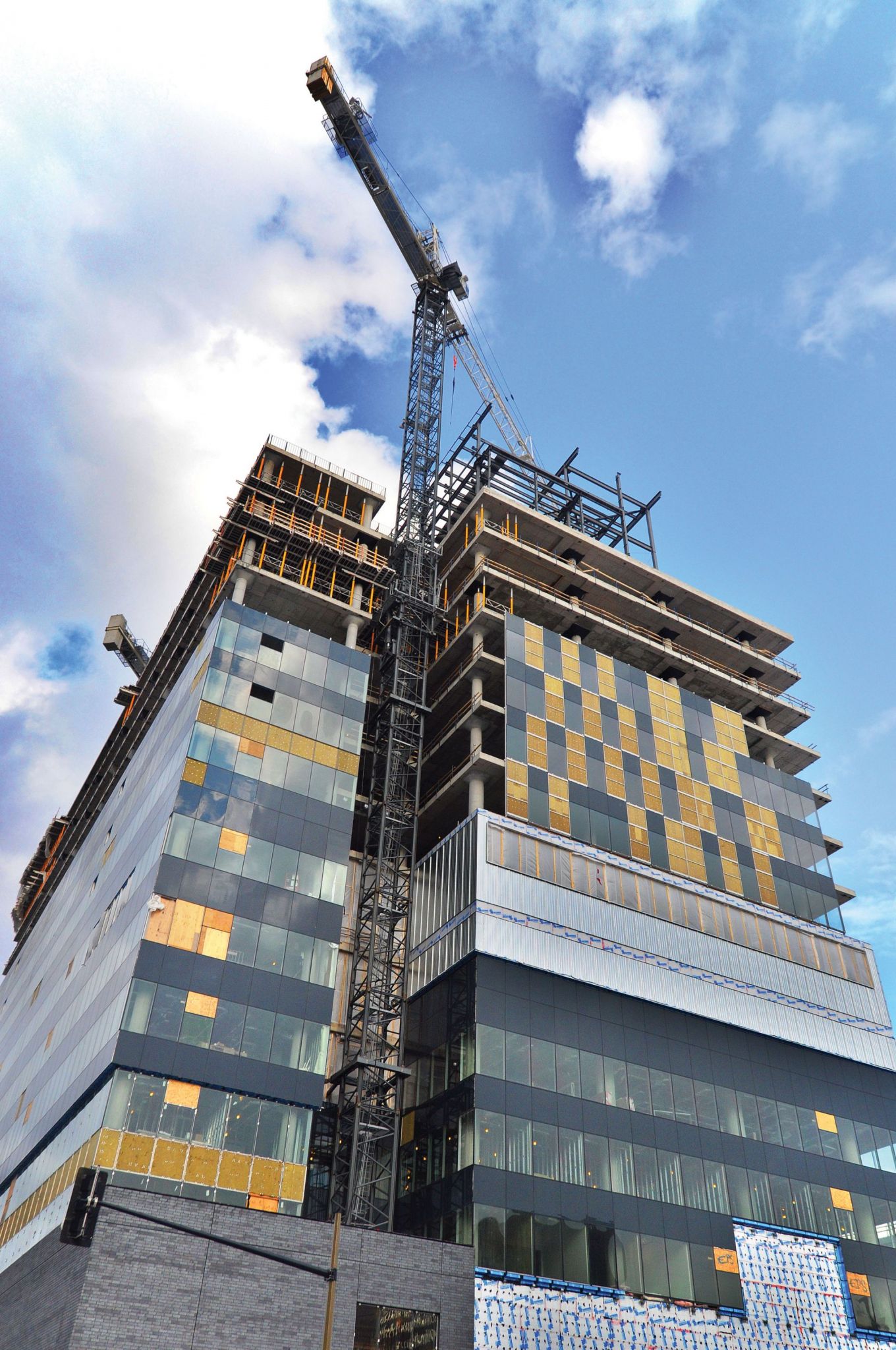
By Christian Dutil
Constructing the buildings that define communities is not simply a matter of enclosing a volume of space, but rather a complex blending of function, esthetics, needs, and owners’ desires. These criteria must fit within the practical constraints of climate, available resources, and schedule demands. As competition increases, successful contractors must continually find new ways to cut costs and protect margins without sacrificing quality or client satisfaction.1
The search for better, faster, and more efficient construction methods drives innovation and has brought about revolutionary changes in building materials and construction technology. One such example is the introduction of moisture- and mould-resistant gypsum panels, which facilitate changes to traditional job sequencing that can significantly improve both scheduling and installation quality.
However, it is important design/construction professionals consider more than just material substitution. All aspects of system performance must be taken into account, and only then can new construction practices be implemented in a manner that delivers the desired product faster, more efficiently, and with better cost-effectiveness.
Pre-dry-in construction
A significant development in the drywall industry has been the introduction of what is known as ‘top-down’ or ‘topping-out’ construction, referring to installing some portion of drywall ‘pre-dry-in’—well in advance of closing up the structure and making it weathertight as in conventional industry practice. This practice is still evolving across North America and an industry-wide glossary of terms and standard practices is being developed by the Gypsum Association. First introduced to speed construction, a specific problem in ceiling plenums, pre-dry-in construction now extends to include all interior drywall installation when the building has not yet been dried-in. This article discusses the advantages and limitations of this practice, including some of the important system performance factors to be considered when evaluating the suitability of pre-dry-in construction for a particular project.
Implementing the original concept
Any discussion of pre-dry-in work should begin with the original concept of top-down construction.2 Dry-in construction entails co-ordinating the trades so the drywall trade installs the interior metal framing and then hangs drywall only in the plenum above the finished ceiling plane before the mechanical, electrical, and plumbing (MEP) trades install ducts, conduit, and pipes that penetrate the plenum walls.
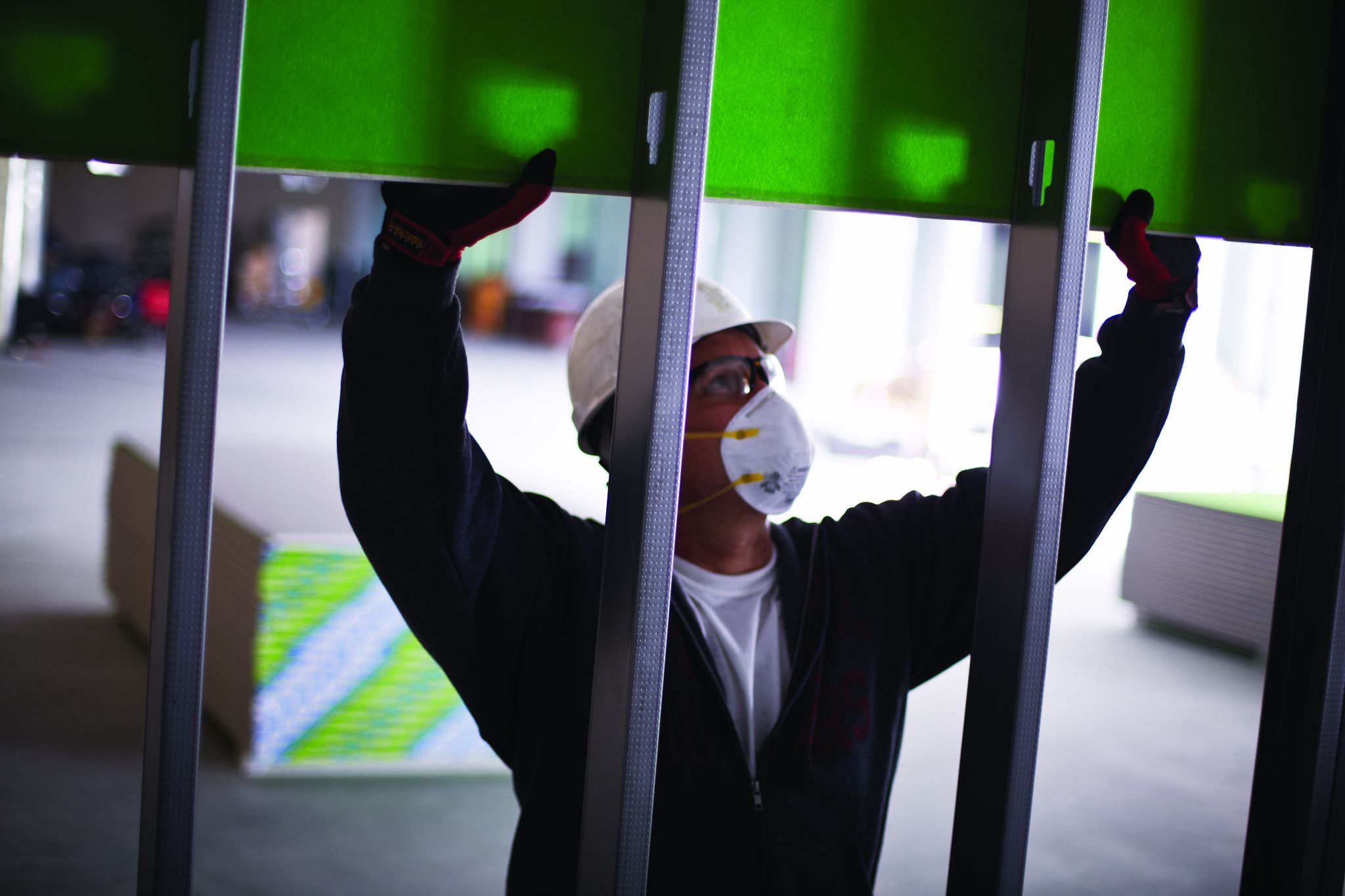
Traditional construction practices install MEP first, followed by the metal framing and drywall once the building has been enclosed and is weathertight, or dried-in. However, traditional sequencing leads to the cumbersome and time-consuming process of fitting and piecing together gypsum drywall around duct and pipe penetrations like pieces of a jigsaw puzzle. This creates the possibility for quality and fire-resistance ratings to be compromised at difficult-to-reach joints and penetrations.
In contrast, pre-dry-in construction avoids these difficulties and results in faster, easier installation of the gypsum panels with tighter fits around the penetrating items. In the plenum space, joint finishing can usually be done quickly and simply by fire-taping the joints.3 As a result, pre-dry-in construction can speed construction and reduce costs while simultaneously improving quality and finish.
Installing metal framing and drywall ahead of MEP requires drywall be hung before the building has been fully closed in. Therefore, the interior construction is not protected from weather for a period.
Restricting this practice to the plenum space above the ceiling plane provides partial protection from weather exposure for the roof or floor deck above, and also ensures water will not collect and pool where it will be in direct contact with the gypsum panels. However, the panels at the perimeter are more exposed to the exterior elements. As such, standard paper-faced gypsum board is not suitable for these limited outdoor exposures—special water and mould-resistant gypsum panels should always be used for this application.
Water and mould resistance
The water and mould resistance of glass-mat gypsum panels as defined in ASTM C1658, Standard Specification for Glass Mat Gypsum Panels, is considered superior to water-resistant paper-faced gypsum boards. As a result, glass-mat gypsum panels have become the preferred panel for weather-exposed applications. This logic is now being extended to interior spaces where pre-dry-in construction has come to include hanging the gypsum drywall over the wall’s full floor-to-ceiling height. It is no longer limited to just the partial wall of the plenum space above the ceiling plane. This practice creates much greater exposure risks, even for glass-mat faced gypsum panels, which must be understood and considered carefully.
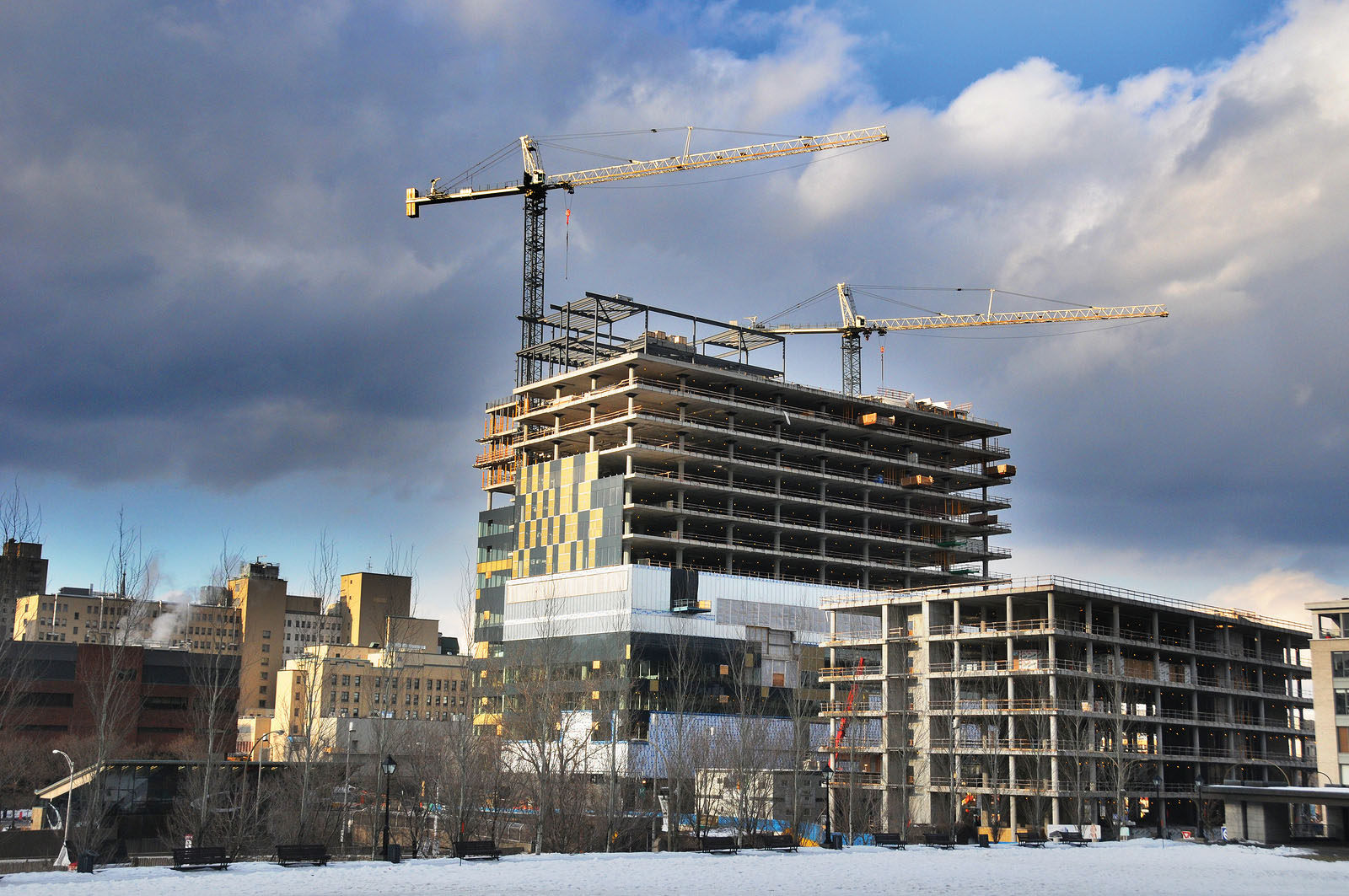
The pre-dry-in concept is essentially building inside-out with interior walls that are traditionally protected from the weather going up before the building envelope is closed in, thereby temporarily exposing interior systems to outdoor conditions. While glass-mat interior gypsum panels and other specialty gypsum panels are now commonly warranted for up to one year of exposure to the elements, there is still a risk too much water will compromise even water- and mould-resistant panels. As a result, all manufacturers exclude warranty coverage where there is excessive moisture, cascading water, or weather events such as tornadoes, hurricanes, and major thunderstorms combining wind and water.
However, moisture is not the only problem. Freezing conditions and high temperatures can also cause problems, especially when the panels are not suitably conditioned to the end-use occupancy conditions (i.e. temperature and relative humidity) before joint compound and paint are applied.
More than the drywall panel performance alone should be taken into consideration when deciding if this is the right option for a project. Many project-specific factors weigh on whether the contractor can anticipate benefits from pre-rocking or will increase the risk and liability for the job. There is no easy rule of thumb that can be used for this calculation. The risk factors associated with building in a Southern Ontario climate versus the Atlantic Provinces, or the Badlands of Alberta versus the B.C. Coast, are markedly different and affected by such factors as climate and season, project duration, and design details that can mitigate or amplify moisture exposures.
Risk factors and prevention
It has been established the most important and effective means of preventing mould growth in buildings is through moisture control. Mould spores are ubiquitous in nature and require only a film of dust or dirt to support growth, even on inorganic substrates. Dirt on the surface of the gypsum drywall, or collecting in wall cavities, may be enough to foster the germination of spores when environmental conditions are conducive to mould growth. Such is the case even if the gypsum drywall itself does not deteriorate from moisture exposure.
An additional source of concern is moisture pooling in the bottom track of the metal framing runner channels combined with dirt in the wall cavity, this can lead to mould growth, which, in turn, contribute to indoor air quality (IAQ) problems at a later stage of the building’s life.
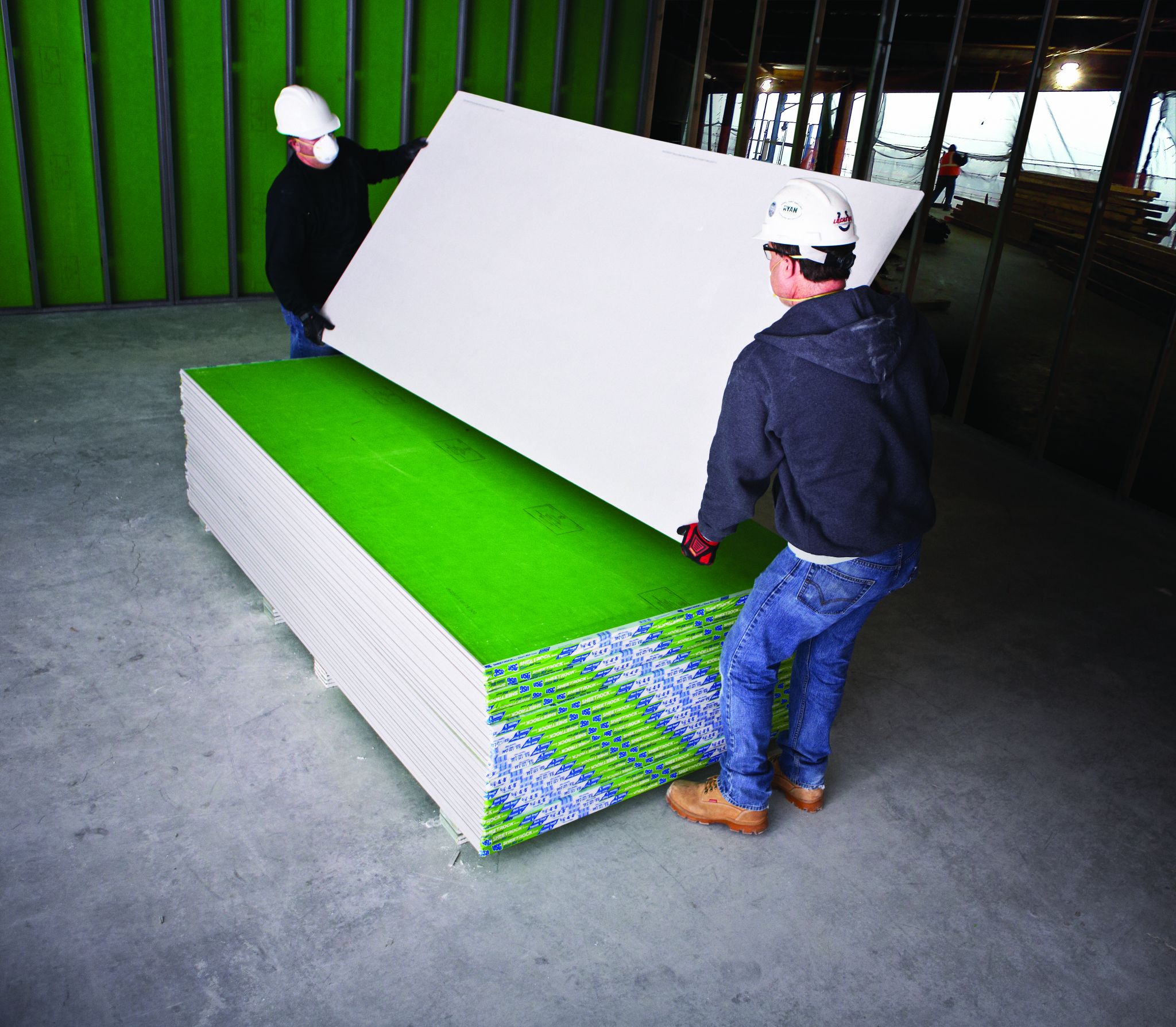
In some climates, and at certain times of the year, the expected amount of precipitation is small and presents a low risk. However, in other locations, or jobs that may have exceedingly long periods of exposure, the potential for mould growth and IAQ problems may unacceptably increase the added risk due to pre-dry-in installation of gypsum drywall. In all cases, contractors are advised to blow dirt out of framing members and dry the walls before enclosing wall cavities that have been exposed to water.
Metal framing and screw fasteners specified for interior applications are generally not manufactured to the same level of corrosion resistance as required of building components approved for use in exterior applications. The risk of corrosion with resulting staining or mechanical failures must be taken into account when deciding if the specified framing or fasteners can withstand the rigours of the outdoor exposures anticipated for the job.
One should also consider what other materials are being used in the wall and their suitability for pre-dry-in construction. Glass fibre, mineral wool, and cellulose insulations used for sound-dampening or fire resistance can absorb surprisingly large amounts of water, making it difficult or impossible to dry out afterward. Moisture trapped in the wall assembly may damage expensive wood trims, cabinets, and flooring, to permanently warp in a building that is not yet dried. Other materials—such as plaster, joint compound, and paint—may chemically react in a wet environment, whereas they normally experience no problems in dry interior applications.
Generally, interior assemblies are not designed to withstand wind loads and other mechanical loads from extreme weather. Again, in some climates and certain seasons, this may not be a concern, but if there is likelihood the structure will stand open during a period of storms and high winds, then fastener spacing and structural design need to be reviewed and revised as appropriate for the interior walls to withstand the resulting loads and movements.
Water that runs easily down a glass-mat panel will end up on the floor, sometimes disappearing from view into the subfloor. This must be dried out before the floors are finished.
Conclusion
The common thread in all these cautionary notes is moisture can affect many other materials in addition to the gypsum drywall itself. Secondly, project teams must not only take into account how much water can get into the building, but also how it will get out. New construction typically involves far more moisture than would be experienced in permanent occupancy. New concrete, paint, and other coatings introduce large amounts of moisture. Waiting until it dries out may not be practical or sufficient. In some cases, professional drying services will need to be brought in. The gypsum drywall manufacturer may warrant the performance of the gypsum drywall, but the contractor is responsible for the resulting assembly.
In conclusion, the practice of pre-dry-in installation of drywall has become an important new tool for contractors and construction managers to consider. It can speed construction, reduce costs, and improve quality by eliminating certain drywall installation and scheduling problems. Like any tool, however, it can also be misapplied and cause serious problems.
This article has examined the general considerations that should be taken into account when evaluating the use of this tool. There are projects for which pre-dry-in construction is an appropriate choice, but there will also be those for which it is not. As noted, the challenge is daunting and the risks can be large, but with proper consideration of all factors influencing the final outcome, the risks become manageable.
Notes
1 This article has been adapted from an earlier piece written by Paul H. Shipp, BS, MS, PhD, principal research associate at USG’s Corporate Research Center. (back to top)
2 For more information, see “The Lowdown on Top-down Construction,” WB2474/03-09, United States Gypsum Company. (back to top)
3 Fire-taping is the commonly used term for a Level 1 finish in the Levels of Finish specified by ASTM C840, Standard Specification for Application and Finishing of Gypsum Board. (back to top)
Christian Dutil is the product marketing manager for panels at CGC Inc. He has been with the company for 11 years and has gained knowledge and expertise in the building industry working closely with building designers and architects, drywall contractors, and dealers. Dutil can be contacted at cdutil@cgcinc.com.