Basics of tilt-up construction
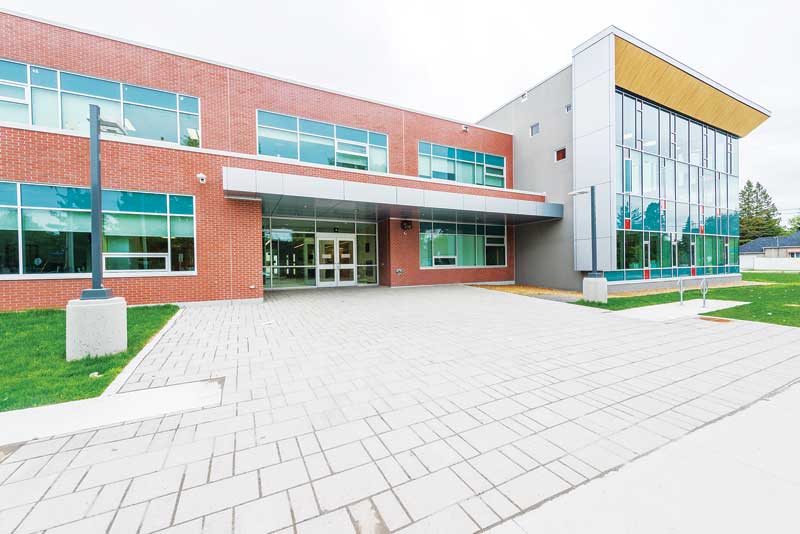
By Nicole Laidler
Tilt-up concrete has been around since the turn of the 20th century, when architect-contractor Robert Aiken used it to construct several buildings in the American Midwest. In an early claim to fame, Thomas Edison employed the tilt-up method to build concrete houses in New Jersey, some of which are still standing today. (For more information, read christineadamsbeckett.com/2012/04/03/thomas-edisons-beautiful-failure.)
Tilt-up concrete fell out of favour during the Great Depression when putting people back to work was the priority, but regained popularity during the post-World War II construction boom. The development of mobile cranes and advancements in concrete also solidified its reputation as an efficient and low-cost building method. By mid-century, it was being used almost exclusively for warehouses and other big-box structures.
Tilt-up remains a good choice for large-box structures, but the method also offers the flexibility to deliver a wide range of complex and creative projects. Today, tilt-up represents about 10 per cent of the total nonresidential building market in the United States. No figures are available for the Canadian building market, but the Tilt-up Concrete Association (TCA) estimates that the industry as a whole is growing at around 20 per cent each year. (The Tilt-up Concrete Association [TCA] is the international nonprofit trade association for the global tilt-up concrete construction industry. It provides training, certification, and other resources for tilt-up construction throughout North America. To learn more about the association, visit www.tilt-up.org.)
Although fairly new to Ontario, more than 200 tilt-up projects have been completed across the province, including 37 school buildings, multistorey office buildings, warehouses in excess of 9290 m2 (100,000 sf), and the Toronto Premium Outlets shopping mall in Halton Hills, Ont.
The basics of tilt-up construction
Tilt-up construction is similar to a traditional barn-raising. Regardless of the project type, the process begins with the preparation of the jobsite and the pouring of the concrete floor slab. Footings around the slab are also installed in preparation for the panels.
The concrete panels are cast either on the floor slab or on an adjacent slab, depending on the building’s footprint.
Standard dimensional lumber is used to create panel forms, which act like a mould for the concrete by providing the panels’ exact shape as well as openings for doorways and windows. The steel grid of reinforcing bars is tied into the form, and inserts and embeds for lifting the panels and attaching them to the footing, roof system, and to each other are also installed.
Tilt-up panels are built from the outside of the wall to the inside of the wall, so any exterior cladding or formliners are placed on the slab before concrete is poured into the forms. Insulation is also encased into the building panels—a feature providing tilt-up buildings with true edge-to-edge insulation, thereby eliminating thermal bridging.
Complete buildings are often lifted in a matter of days. Panels are temporarily braced until the structural connections of the building have been completed.
The building is now ready for any exterior wall finishes such as sandblasting, painting, or staining, if required. Joints are caulked, with typical panel joints consisting of a 20-mm (0.78-in.) gap between panels filled with insulation, backer rod, and caulking to prevent water penetration. Any imperfections in the wall surfaces are patched. At this point, the roof system can be installed—trades can then begin their work inside the building.