Avoiding waterproofing errors in showers
By Matt Valore and Erin Bullock
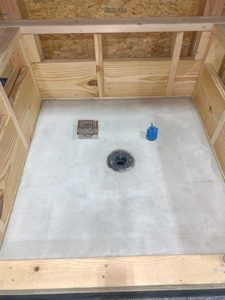
The Ontario Building Code states shower receptors should be constructed and arranged so water cannot leak through the walls or floor. The National Plumbing Code of Canada details the use of leak proofing material in showers, but not much else is stated regarding the construction of showers.
However, the Tile Council of North America (TCNA) bridges that gap with the TCNA Handbook for ceramic, glass, and natural stone tile installation. The TCNA establishes the American National Standards Institute (ANSI) standards used for tile installation in showers through a consensus process. It involves manufacturers of tile and tile installation products, and these recommendations are compiled in the TCNA Handbook. The handbook is a source for tile specifiers and installing contractors, and details shower receptors, including limitations, membrane options, materials, and installation specifications.
When it comes to shower installation and waterproofing, taking shortcuts can lead to disastrous results, especially when a floor is not properly sloped and/or a waterproofing membrane is carelessly installed. To avoid these issues, construction professionals should have a higher level of knowledge of waterproofing techniques and how they can accommodate jobsite variabilities.
This article highlights common installation and waterproofing mistakes which heighten the probability of shower system failures.
Adequate structural support of subfloor
Shower failures can stem from many different issues. First and foremost, when constructing a shower, whether using a preformed pan or a mortar bed, be sure the subfloor is free of defects as per TCNA guidelines. Any movement in the shower system because of an unstable substrate will most likely result in failure. A waterproofing membrane is only effective when properly supported.
Subflooring needs to be provided beneath a floor finish, where the finish does not have adequate strength to support the design loads.
Understanding the difference between waterproof and water-resistant wallboard
Another common issue is improper use of wallboard for the application. Many installers use wallboards, which are water durable but not waterproof. A water durable product or material can withstand water penetration to some degree but not entirely, whereas a waterproof product or material is impervious to water.
TCNA states, “A waterproof membrane or vapor retarder membrane must be specified to prevent moisture intrusion and protect adjacent building materials.”