How to avoid common channel glass pitfalls
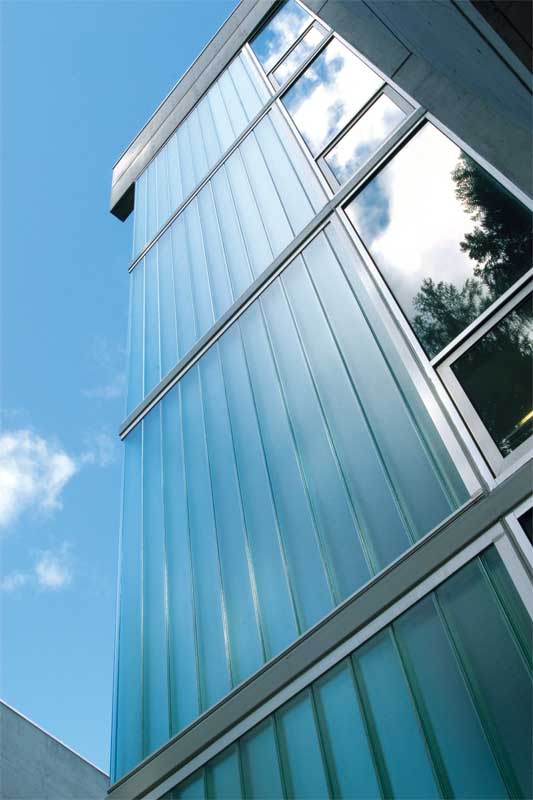
Involving the structural engineer of record late in the project life cycle
When designing with channel glass, it is critical to receive the input of the structural or professional engineer as early as possible during the project life cycle. This person’s direction on anchoring the channel glass assembly to surrounding structural elements and the allowable structural loads imposed on the glass has the potential to change the fabrication and installation approach. It may also change the design of the glass, or even the building itself.
One might consider channel glass specified in sweeping vertical installations. While the cast-glass channels can span up to 7 m (23 ft), design-imposed wind loads will ultimately determine the channels’ maximum length. As such, one should consult with the structural engineer of record early in the project development phase to determine how design loads may impact the desired esthetic, and if alterations are necessary. If wind loads do limit the length of single- or dual-glazed channel glass segments and constrain the design intent, the project team will then have adequate time for problem solving.
For instance, the design team may be able to split the elevation to achieve desired outcomes (Figure 6). This requires adding a structural member within the large framed opening at or below the upper height limit for the desired wind load, creating two separate openings to independently support the channel glass perimeter framing and emulate the esthetic of a tall, sweeping glazed wall. Framing should always be installed plumb, level, and square.
Alternately, in instances of dual-glazed configurations, the addition of a wind load anchor (a small multiple-part clip that secures the inboard and outboard glass planks at each joint while tying back to a structural member internal to the building envelope) can provide the desired glass height in a single framed opening while keeping the bending allowances of the glass below their critical values.
Whatever the solution, early engagement of the structural or professional engineer of record is the best way to avoid costly, last-minute project alterations or impractical solutions that fail to achieve critical performance and design goals.
Improperly weather-sealing the framing
To create the desired esthetic, it may be tempting to reduce the size of perimeter sealant joints. The reality is appropriately sized sealant joints help weatherproof the glazing system by not allowing water or air to pass around the frame or between the channels. Since the sealant type and joint depth define how much allowable movement the joint can withstand, it is crucial to research this component or consult with the sealant manufacturer.
It is also important to seal accessories such as flashings, shims, expansion joints, splice joints, and trim so they do not interfere with the perimeter joints. Manufacturer guidelines are designed to aid in this process. Improperly sealed accessories can affect proper sizing and movement of the system’s primary and secondary seal.
For exterior installations, the weep system of the sill framing must also be properly sealed at the ends, as well as be baffled at the exterior weep exit points per the manufacturer’s instructions.