Are You Getting What You Paid For?: Quality control techniques for evaluating glazing assemblies
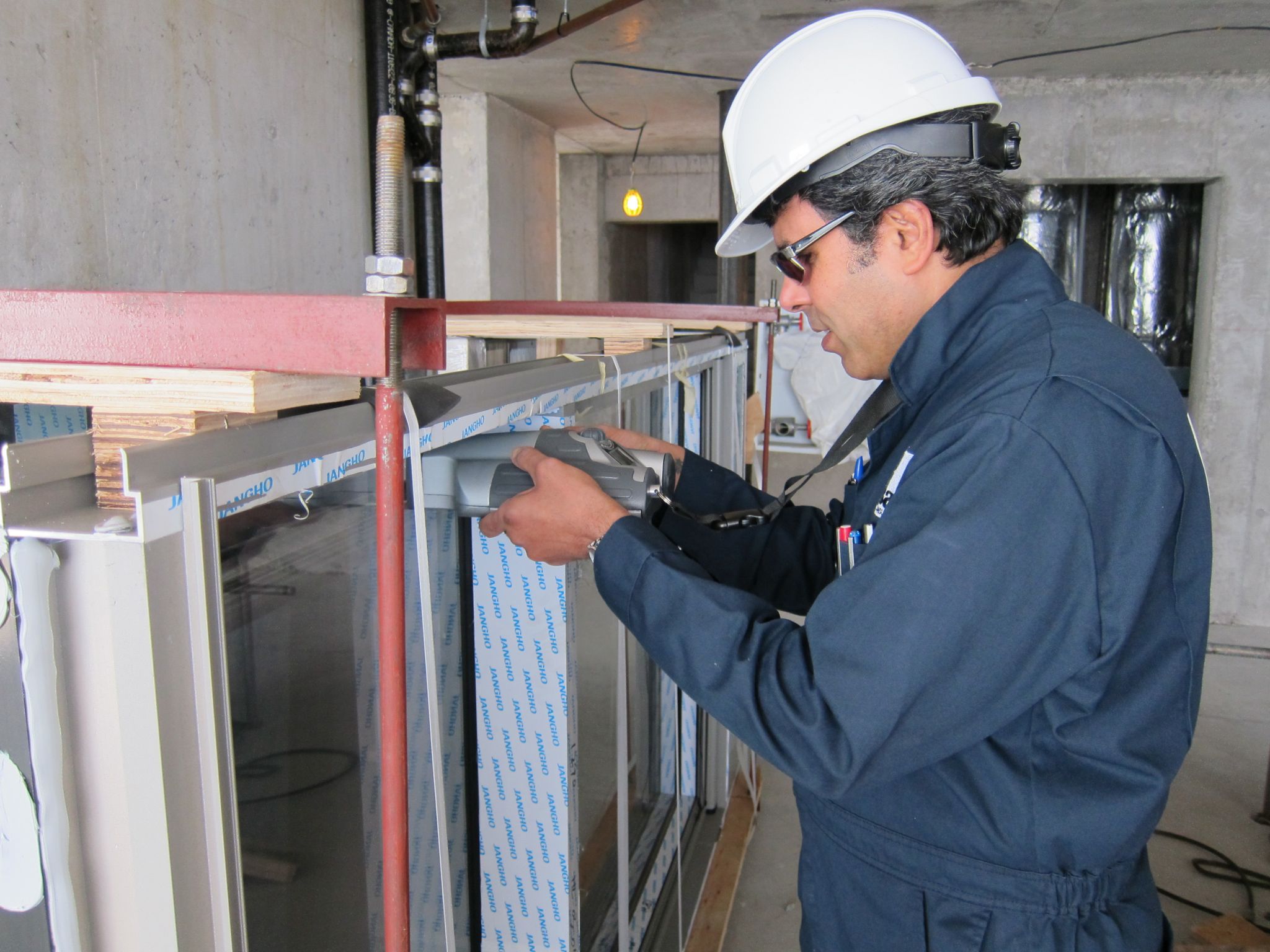
By Hamid Vossoughi, P.Eng., and Blair Gamracy, B.Arch.Sci.
Glass is the most common material in the construction of any building’s exterior façade. It is used in windows, doors, curtain walls, skylights, guards, and canopies, as well as in the form of single-pane, double or triple insulating glass (IG) units, and laminated assemblies.
Given the high demand for glass and glazing assemblies, and the recent amendment to the Ontario Building Code (OBC) that draws attention to the risks related to balcony glass, it is crucial glazed assemblies meet industry standards. This article provides an overview of a few of the glass/glazed assembly requirements, along with test methods that can be used to check performance.1
IGUs and tempered glass
IG units (or IGUs) are glass assemblies consisting of two or more lites sealed and separated with a gas space intended to improve thermal performance. Noble gases—such as krypton, argon, or xenon—are less conductive than air. When a high percentage of noble gas is inserted between the glass lites, it enhances thermal performance.
For example, a minimum of 90 per cent argon is required in the gas space to achieve improved performance under Canadian General Standards Board (CGSB) 12.8, National Standard in Canada–Insulating Glass Units, and ASTM E2190, Standard Specification for Insulation Glass Unit Performance and Evaluation. Argon-filled IGUs generally have U-values (i.e. overall co-efficient of heat transmission) ranging from 0.4 to 0.31 W/m2K (i.e. R-2.5 to R-3.2), compared to air-filled IGUs with U-values of around 0.5 W/m2K (i.e. R-2). While there is a cost premium for gas-filled over air-filled units, argon-including products are quite common and seen as ‘normal.’
Tempered, or ‘safety,’ glass is typically specified for glazing assemblies designed for doors, balcony guards, and windows/curtain walls that extend close to floor slabs. Glass is manufactured by having molten raw material floated through chambers to produce the most basic form of glass—float glass (per CGSB 12.3, National Standard in Canada–Flat, Clear Float Glass, and ASTM C1036, Standard Specification for Flat Glass). The glass is then treated through a heating and cooling process to produce heat-strengthened or tempered glass (varying in strength in relative nominal terms2) per CGSB 12.1, National Standard in Canada–Tempered or Laminated Safety Glass, and ASTM C1048, Standard Specification for Heat-strengthened and Fully Tempered Flat Glass. This process locks in stresses, increasing the strength of the glass to resist load.
When tempered glass breaks, the internal stress causes the glass to shatter into small fragments rather than larger shards typical of annealed and heat-strengthened glass. Thus, using tempered glass poses less risk for injury.
Glass and glazing quality standards
The National Building Code of Canada (NBC), which governs all provincial building codes, sets out requirements for manufacturing and fabricating glass and glazed assemblies. Requirements are also outlined in the aforementioned CGSB standards, as well as in the more current U.S. codes, American Nation Standards Institute (ANSI) and ASTM standards. Insulating Glass Manufacturers Association (IGMA) Canada and other associations also publish requirements and standards.
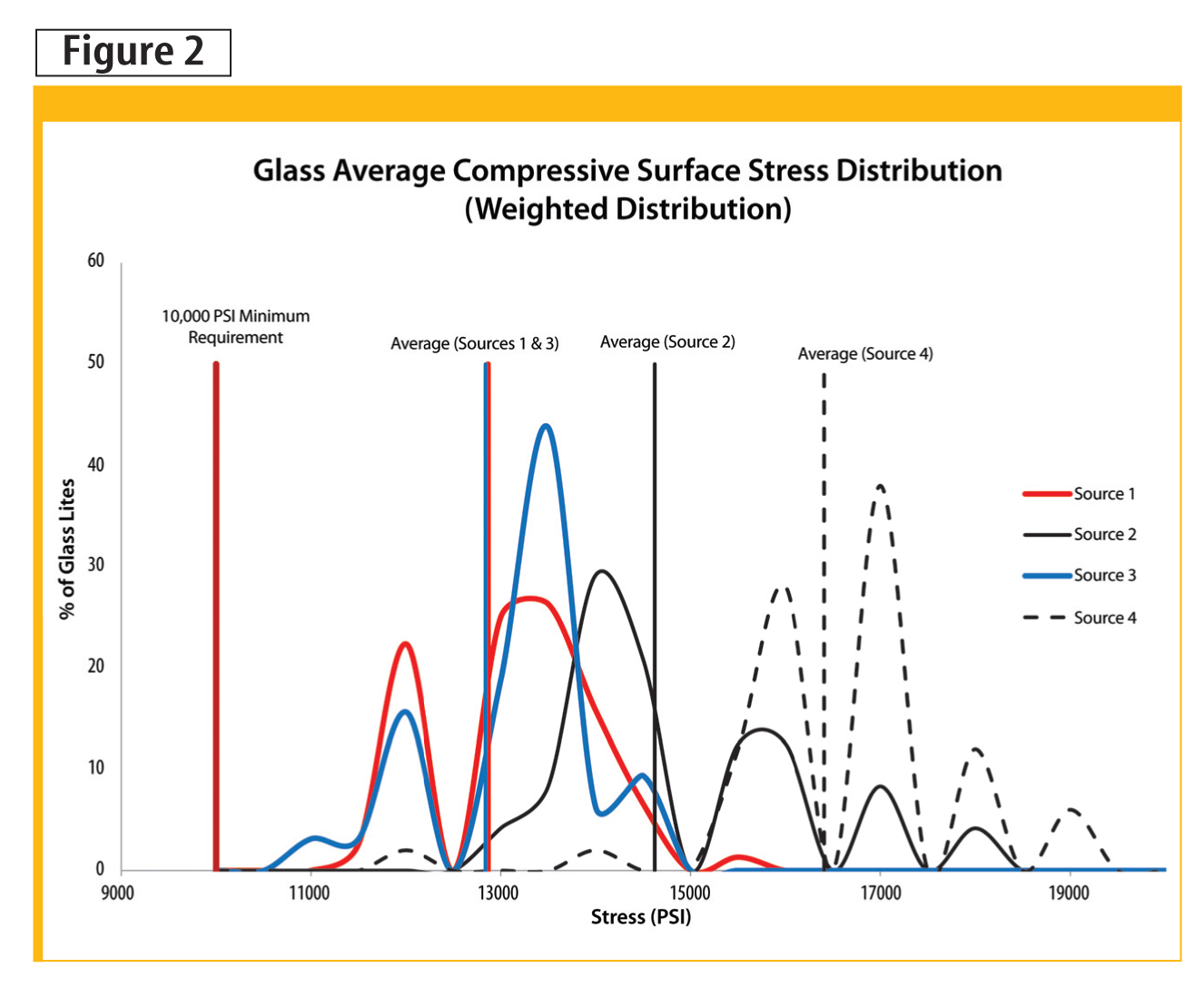
Both CGSB 12.1 and ASTM C1048 require tempered glass achieve a minimum level of compressive residual surface stress post-fabrication. They also offer criteria for fragment sizes after breakage. Tempered glass is generally stamped to indicate it meets the minimum level of specified impact load per CGSB 12.1 and ASTM C1048, along with ANSI Z97.1, American National Standard for Safety Glazing Materials Used in Buildings.
Glazing relies on many other quality control (QC) processes, including those of the manufacturer and fabricator, as well as their equipment and technician training. Glass manufacturers that sell their float glass to fabricators also have their own fabricator certification requirements to ensure quality for the final product. Even with all these checks in place, however, glazed assembly quality can still vary between manufacturers and fabricators.
Why does glass break and what can be done about it?
Glass can break due to defects caused by manufacturing or mishandling (especially during shipping and installation) or when subjected to loads in excess of that for which it was designed. One preventative measure used to minimize risk of breakage due to nickel sulphide (Ni-S) from manufacturing is heat-soaking. In 2012, due to a series of glass railing breakage in Ontario, this treatment became an OBC requirement for tempered balcony railing glass configurations. The code’s Supplementary Bulletin (SB)-13, effective July 2012, calls for heat-soaking of tempered glass when installed within 50 mm (2 in.) of balcony slab edges.
Heat-soaking induces failure in tempered glass with Ni-S inclusions.3 These imperfections are unintentionally incorporated into some glass lites through raw materials used in the manufacturing process. Ni-S inclusions have different thermal properties than the glass—namely, the rate of their thermal expansion is much higher. As such, this differential internal thermal expansion may cause critical Ni-S inclusions to induce spontaneous breakage.
While this process does not eliminate all potentially contaminated glass, it significantly reduces the likelihood of breakage due to Ni-S. Currently, industry consensus is a glass breakage rate of 0.2 per cent due to Ni-S (i.e. two glass lites per 1000) is typically within industry standards.
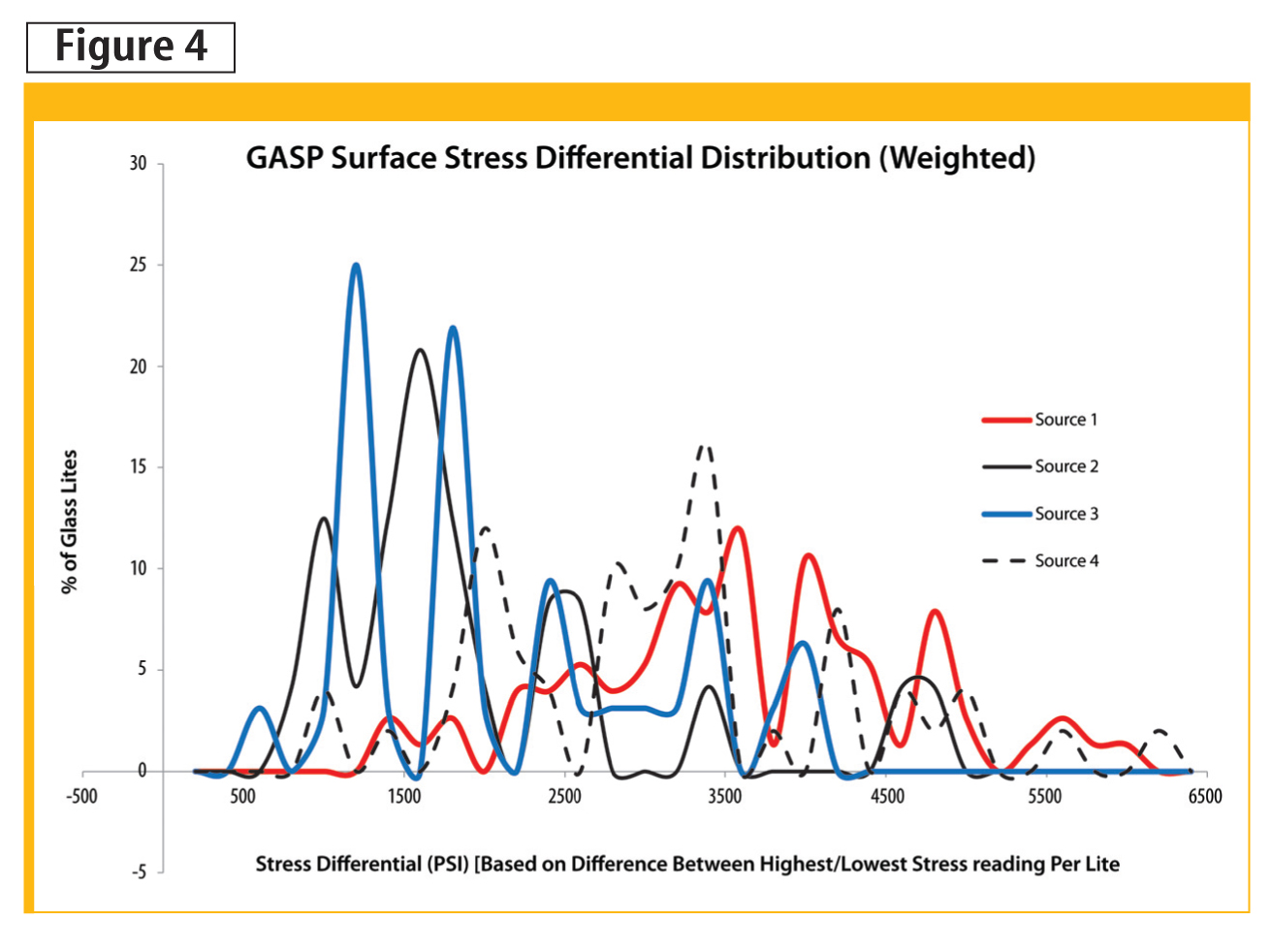
QC test methods
There are several quality control test methods that can be used to check whether glass or glazing assemblies meet performance requirements.
GASP analysis
Glazing angle surface polarimeter (GASP) is a common, standardized off-line technique for evaluating surface stress in tempered glass. The Laser GASP is a calibrated device designed to take non-destructive, photoelastic stress readings from a glass lite (Figure 1). It uses photoelasticity (i.e. the principle light will refract proportionally to a stressed medium) to determine the residual surface stress in a lite of thermally strengthened (annealed, heat-strengthened, or tempered) glass.
Using a series of polarizer filters and prisms, a laser is sent through a discretized segment of glass to generate a fringe pattern. This is then read by a camera and projected onto an LCD screen for visual analysis. Due to the effect of photo-retardation in stressed media, the fringe pattern’s angle directly correlates to the amount of stress in the glass and is calibrated specifically for each individual device to ensure accuracy. This means the stress level at any location on any given lite of glass can be determined with a reasonable degree of accuracy.
The level of stress due to tempering varies slightly from the centre to the edge of a glass lite and along a lite’s length and width. The stresses within heat-treated glass can be affected by other factors related to the manufacturing process, including varying quality control, type of oven used for the tempering process, and operator experience. For example, glass can be stressed non-uniformly if variability exists in the heat treatment process due to poor calibration of the tempering oven or quenching jets.
Large surface-stress variations may result in areas of the glass having strength levels below minimum requirements. This makes the glass more prone to breakage under loading conditions. It also affects the breakage pattern—in other words, larger glass fragments than expected can occur.
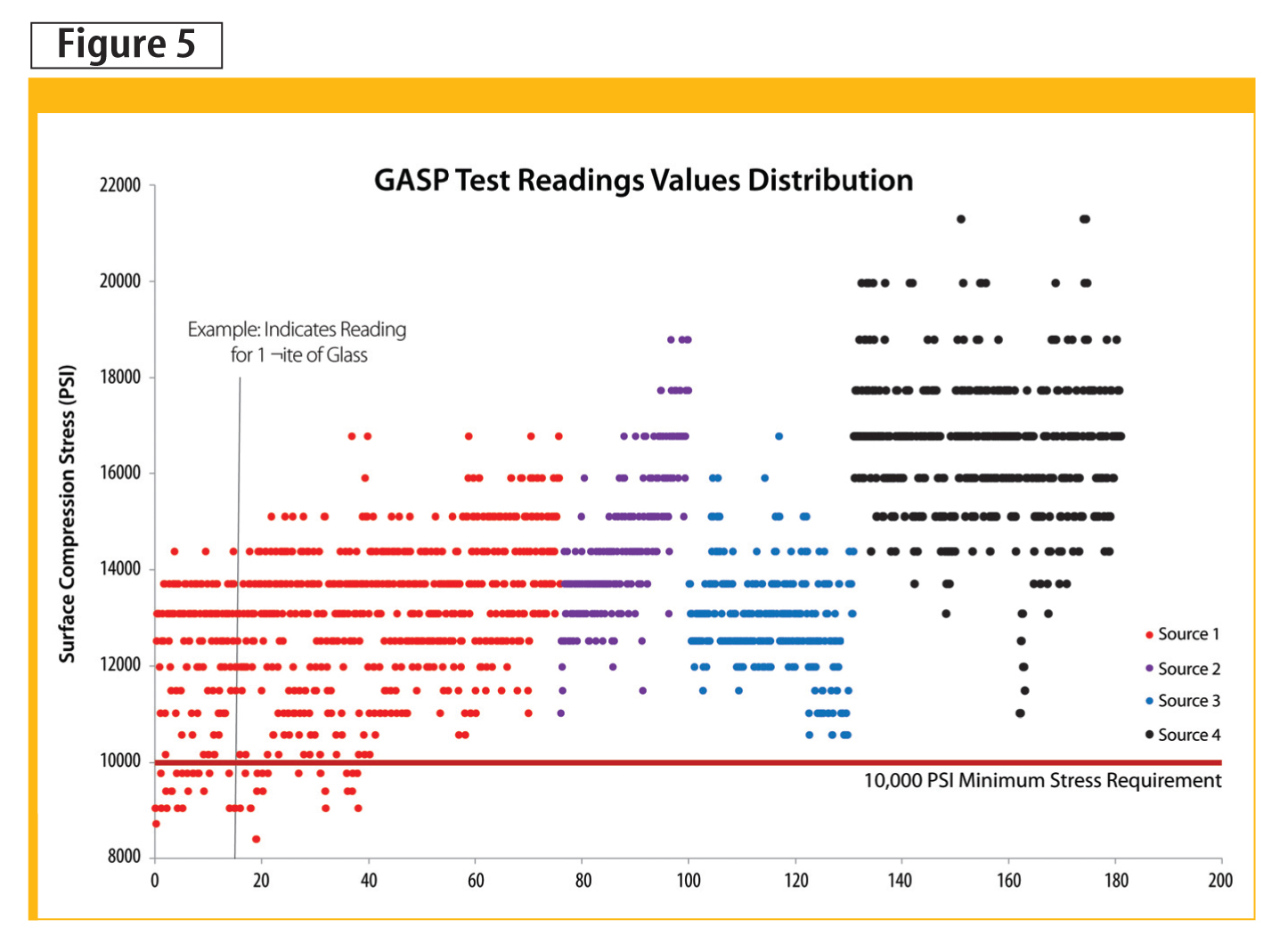
The average of stress readings in the glass plates is required to exceed the minimum stress level. Figure 2 shows average compressive residual surface stress (CRSS) readings (i.e. level of internal stress in the glass) from some tempered glass samples from different manufacturers. These are based on GASP readings per ASTM C1279, Standard Test Method for Non-destructive Photoelastic Measurement of Edge and Surface Stresses in Annealed, Heat-strengthened, and Fully Tempered Flat Glass.
The average stress readings for glass lites shown ranged from (11,000 to 19,000 psi). As shown, Sources 1 and 3 had lower averages (around [12,800 psi]) when compared to Source 2 ([14,600 psi]) and Source 4 ([16,400 psi]). While CRSS levels for all sources vary significantly, they all meet the minimum requirements of (10,000 psi).
To achieve an average CRSS, ASTM C1048 requires 10 readings for each glass lite (Figure 3). Figure 4 indicates the differential CRSS distribution per lite of glass manufactured from each source. As indicated, some lites had CRSS differentials of more than (6000 psi). A high surface stress differential typically indicates non-uniformity in the tempering process (and likely poor quality control).
The data shown in Figure 4 is reinforced by the cloud diagram of Figure 5, which shows the CRSS variation per lite of glass. A close look at Source 1 shows many individual readings were below (10,000 psi), while other readings from the same lite of glass were in the (15,000-psi) range. Again, this variation is indicative of a quality control issue that affects uniformity of the tempering process.
Fragmentation testing
Fragmentation is a destructive form of testing tempered glass outlined in CAN/CGSB 12.1. It is used to determine whether the breakage pattern and size of fragments of a broken lite meet standard requirements.
The breakage pattern and size of fragments are affected by the glass surface stress levels. Generally, the lower the glass surface stress level, the larger the glass fragment sizes when a tempered glass lite is broken.
The safety requirements for tempered glass mandate the 10 largest fragments recovered from a glass lite within five minutes of fracture are smaller than the weight of 6500 mm2 (10 si) of unbroken glass of equivalent thickness. Specifically, the 10 largest fragments away from the 25-mm (1-in.) perimeter of a glass lite must be below 97 and 162 g (3.4 and 5.7 oz) for a nominal 6- and 10-mm (1/4- and 2/5-in.) thick glass lite, respectively.
Even though a glass lite may pass CRSS average requirement of 10,000 psi, it is the authors’ experience a large stress range variation may produce fragment sizes that may not meet requirements for tempered safety glass (Figure 6).
SES testing
Spark emission spectroscopy (SES) is a non-destructive form of testing outlined by ASTM E2649, Standard Test Method for Determining Argon Concentration in Sealed Insulating Glass Units Using Spark Emission Spectroscopy. Using a device to spark the argon fill, it measures the percentage of gas fill between the glass lites used in an IGU.
Some of the inherent issues with respect to IGU gas fill are that an inadequate percentage of gas may be injected into the unit, or the gas may escape from breaches in perimeter seals through diffusion. For every 10 per cent reduction in the argon content, the U-value increases by 0.01 to 0.02 W/m2K, which causes a reduction in R-value. Since one cannot visually determine gas fill concentration, techniques such as SES can be used to check the percentage of gas content within IGUs.
In a recent sampling of IGUs from different glass manufacturers, the percentage of argon was evaluated through gas fill testing in both the field and manufacturing facilities. In some cases, manufacturers produced IGUs where the percentage of argon was greater than the specified minimum 90 per cent concentration. In other instances, IGUs measured onsite had less than the specified minimum concentration—in some cases, it was as low as 50 per cent. After quality control issues were addressed, subsequent tests produced results above the minimum requirements.
Conclusion
Quality control is integral to producing robust glazed assemblies that meet industry standards. While it is not uncommon for the end user to assume industry requirements have been met, some testing can diagnose potential issues with fabrication processes that can be adjusted to deliver product that meets expectations.
Notes
1 The authors acknowledge the contributions of Tim Campbell and Corey Wilson, both with Halsall Associates, in preparing this article. (back to top)
2 In relative nominal terms, heat-strengthened and tempered glass have two and four times the strength of the same thickness of annealed glass. (back to top)
3 This is per EN-14179-1:2005, European Standard: Glass in Building–Heat Soaked Thermally Toughened Soda Lime Silicate Safety Glass. (back to top)
Hamid Vossoughi, P.Eng., is a project manager with the Restoration Team at Halsall Associates—a national engineering firm with more than 55 years of experience designing, evaluating, and renewing buildings. He joined Halsall in 2007, following 16 years with one of the top consulting firms in the United States and more than four years as a specialty contractor. Vossoughi has a bachelor’s degree in civil engineering and a master’s degree in structural engineering, and specializes in the evaluation and rehabilitation of cladding systems. He can be reached at hvossoughi@halsall.com.
Blair Gamracy is also a project manager with Halsall’s Restoration Team. He has a bachelor’s degree (honours) in architectural science, specializing in building science. Gamracy is the glazing practice leader at Halsall. He can be reached at bgamracy@halsall.com.