Achieving net-zero goals with architectural zinc

A recent study calculated 65 per cent of zinc production’s carbon footprint could be attributed to smelting. Choosing zinc manufacturers that have minimized their already relatively low carbon footprint is one more step toward reducing overall GHG emissions.7
For architectural applications, raw zinc material is smelted, cast as a material of uniform and certified quality, and wound as a coil-in-one continuous operation. Rolled zinc sheet is produced by alloying special high-grade (SHG), 99.995 per cent pure zinc with minute quantities of copper, titanium, and aluminum. The alloy composition provides the material the necessary strength, while allowing the architectural product to be easily shaped.
IZA provides practical guidance on calculating the carbon footprint for SHG zinc, in compliance with the International Organization for Standardization (ISO) 14040 and 14044, and the Product Life Cycle Accounting and Reporting Standard by GHG Protocol.8 As a global average, the IZA calculated the carbon footprint GWP for primary SHG zinc production to be 3.64 kg (8.02 lb) CO2eq per 1 kg (2.2 lb).9 Many IZA member companies have committed to climate change policies to reach net-zero Scopes 1 and 2 GHG emissions by 2050. An increasing number also are working on Scope 3 targets.10
One IZA member has further lowered the carbon footprint of its SHG zinc product to achieve a 100-year GWP of 1.85 kg (4.08 lb) CO2eq per 1 kg (2.2 lb).11 This savings was gained through energy-efficient production practices that rely on electricity largely generated from renewable sources, including water and wind power. In addition, its product uses recycled zinc material. This investment reduced the product’s impact by 54 per cent and saves more than 36,000 tonnes (3,5431 tons) of CO2eq each year, equivalent to the GHG emissions of a small town with 5,400 people. Quantifying this to size and area, a standing-seam roof would have 12 kg (26.5 lb) CO2eq per 1 m2 (26.5 lb per 10.8 sf). This low-carbon architectural zinc material is now available in North America.
Composition, patination, and installation of architectural zinc
In North America, ASTM B69-21, Standard Specification for Rolled Zinc, is the primary reference document for Type 1 and Type 2 architectural rolled SHG zinc alloys and their expected characteristics.12 The zinc alloy composition determines the metal’s colouration. Type 1 tends toward blue-grey and Type 2 contains slightly more copper (0.80-1.00 per cent), which produces more of a graphite-grey colouration.
Untreated, architectural-grade zinc looks bright and shiny, and is light reflective. Over time, a natural matte patina develops, creating a dynamic appearance as the material ages. A patina’s formation is the process of zinc carbonate “freckles” gradually growing together. The rate of its formation is related to the slope of the surface. The patina will form more slowly on a vertical wall surface than on a slightly pitched roof. The patination speed varies between six months and five years or more, depending on climatic conditions. The more exposure to wetting and drying cycles, the quicker the patina will develop.
Some manufacturers offer pre-weathered zinc material that accelerates the patina formation under controlled conditions. Factory-finished options are also available to achieve an initial, uniform esthetic. Typically, these finishes are painted or phosphate architectural coatings applied in the factory under environmentally controlled conditions.
Architectural zinc coils are unwound, cut, and fabricated into panels, tiles, and other formed exterior and interior architectural products. Sheets also can be perforated and fashioned into ornamental accents. Since zinc is a lightweight material, it can help reduce the structural load and associated materials on a building.
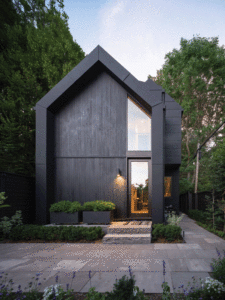
Qualified contractors can install zinc products as wall cladding and facade systems; on low-sloped, steep-sloped, flat, and mansard roofs; and as hip and ridge caps, drip edges, alleys, step flashing, dormers, cupolas, parapets, gutters, downspouts, and more. Fabricators can also customize seam profiles to the project’s requirements.
Meeting building projects’ sustainable goals, contractors, fabricators, and installers provide high-performance, low-carbon product solutions. Some are considering the environmental impact of their own practices. Federal agencies and other AHJs can require reports for operational, transportation, and equipment GHG emissions; energy and material sourcing, recycling, and landfill waste streams.
Climate-resilient, long-lived performance
Architectural zinc has been used in coastal communities for generations and can be seen on building projects across many climate zones. Installed properly, zinc roofing and wall systems will resist air and water infiltration, and withstand high winds reaching up to 241 kph (150 mph).