Architectural zinc roofing considerations
by Richard Strickland and Peter Gatto
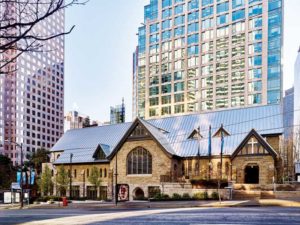
Proper specification, design, and installation of a zinc roof can provide an esthetically appealing, cost-effective, durable system capable of lasting for up to 80 years. To realize the full potential of a zinc roof, it is important to understand not only project-specific conditions, but also the material’s composition and colour palette, seam types, attachment, and installation.
Zinc composition, colour, and curves
Zinc is a natural, soft metal. Rolled zinc ‘strip’ (sheet or coil) is produced by alloying special high-grade, 99.99 per cent pure zinc with small quantities of copper, titanium, and aluminum. The rolled zinc alloy provides improved mechanical properties required for architectural applications, including roofing, roof-edge flashing and trim, gutter systems, façade cladding, and exterior ornamentation.
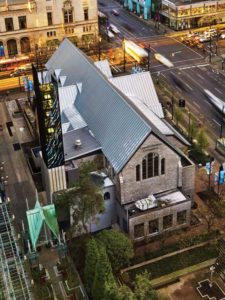
With solid, rolled zinc, no paint, varnish, or sealants are required. It resists corrosion, and the run-off is non-staining and non-toxic. It requires minimal maintenance, and if scratched, it self-heals. The key to this durability and to zinc’s unique appearance is its patination. Just as copper ages from shiny orange to powdered green, zinc develops its distinctive patina from bright silver to matte blue-grey or graphite-grey, based on the alloy composition.
In North America, ASTM B69-16, Standards Specification for Rolled Zinc, is the primary reference for this material. Two types of rolled zinc are outlined in this standard. Type 1 is the most common architectural zinc alloy; and Type 2 contains slightly more copper than Type 1. This alloy results in a natural patina generally darker in colour than Type 1. The actual colour of the patina is specific to the micro environment.
To minimize variations, zinc roof specifications may note, all material should be provided from the same manufacturer as a single batch.
When a roof’s design calls for rolled zinc to be curved into a radius, zinc-appropriate tooling and practices should also be specified. To avoid causing fractures or micro-cracks in the zinc, qualified fabricators use bending equipment with a radius, that must be at least 1.75 times the material thickness.
To achieve specified appearance and performance, one must be aware zinc manufacturers are not synonymous with system suppliers, fabricators, or installers of zinc products. Specifying an experienced zinc manufacturer can offer a high-level of knowledge and service through design, specification, and installation.