Architectural polished concrete: Defending design intent
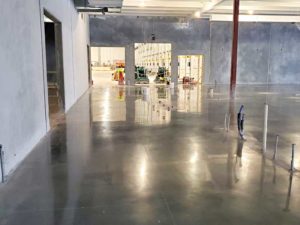
By Bill DuBois, CSI, CCS, AIA, and Chris Bennett, CSI, AIA
Construction documents need to be clear, concise, correct, and complete—but is this enough to fend off the twists and turns of executing the contract for construction? One may begin with the very best in design intent, but it is the responsibility of the entire project team to understand and adhere to this for it to become a reality. Too often, team members will alter the intended design from lack of understanding the material or even to accommodate their own business advantage. Construction administration is critical to ensure the design intent is achieved and owners are properly protected.
To demonstrate the humanistic aspect of construction, this article makes an analogy between two complex assemblies of infrastructure—the human body and a constructed facility. Both exist to support life, have a life cycle of their own, and require planning and nurturing before they can take on productive roles. With a little creative flexible thinking, Figure 1 shows the comparisons, while Figure 2 (page 24) offers another analogy—CSI’s facility life cycle process and a possible life cycle of a human being. Similarly, a facility and certainly its concrete must be well-configured with a healthy foundation to increase the chance for a successful, long life.
While the authors could go on examining how buildings compare to biology, that is another story being developed by the field of biomimicry. Instead, this article focuses on the facility’s design intent around Division 03, one of the “muscular/skeletal” systems. To start off on the path of being strong and healthy, and living a long, prosperous life, a person requires a strong foundation of bones and muscles to carry them through. In the built environment, concrete and concrete flooring systems are essential in maintaining a strong facility life.
Concrete thinking
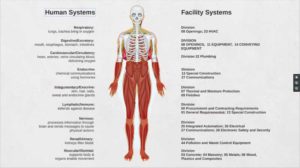
One of the unforeseen gifts that came with the popularity of polished concrete was the realization of how poorly concrete is built. With the demand of polished concrete floors growing, finishes like carpeting, tiles, and epoxies were removed in many buildings—in frequent cases, this enabled project teams to see right underneath the skin, the building was an infected, unhealthy environment. Suddenly, questions arose:
- Why are corrections always needed for curling and curvature remediation?
- What is behind crazing, spalling, and random cracking?
- Why, despite all the products injected into the mix and onto concrete’s surface is there still delamination, and multiple densifier applications?
- Is there a way to stop efflorescence, blushing, and other types of extreme discolouration?
- Why do some buildings that are only a decade or so old still experience expensive, often preventable concrete failure?
Many ideas have been offered to resolve these problems, but they have proved only to be temporary solutions, merely addressing the symptoms of a chronically unhealthy system and not the root cause. To make matters worse, industries have sprouted up around creating such stopgaps, taking away the incentive for suppliers and contractors to meet a healthy, sustainable design intent. This includes a variety of clear coating topical finishes which mimic polished concrete, but do not provide the same performance.
One of the first places to see these problems was flooring, which takes the most physical abuse in most spaces. With the help of gravity, it collects the most dirt and debris, requiring the most routine maintenance. The traffic atop the slab from hard-wheeled equipment or children’s snow boots crusted with rock salt on school floors compounds the abuse.
Project conception | Parents think about starting a family |
Project delivery | Approach the method of birth |
Design | A child develops through stages of growth and elementary education |
Construction documents | A young adult matures in high school to learn the basic skills and get a sense of direction |
Procurement | College selection and settlement on cost |
Construction | College education to build a career |
Facility management | Healthy adult lives, filled with purpose |
Concrete should be able to address these issues for flooring. When done correctly it is durable and long lasting and there are the additional esthetic benefits that should also be built to last. Concrete can be dyed, stained, integrally coloured, textured, or polished. Broken glass, seashells, marble chips, and other media can also be introduced into the concrete matrix to expand the visual possibilities.
However, for a concrete floor to be as maintenance friendly as possible and maintain its original appearance, it must be non-absorptive to resist moisture, dirt, and movement from changes in volume. A facility cannot maintain its clean and healthy status when the floor is dirty or unable to be resilient to abuse.