Architectural polished concrete: Defending design intent
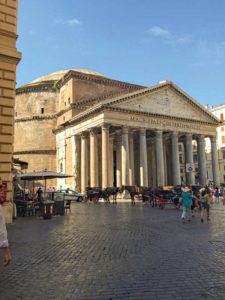
Verification and definitions (or lack thereof)
The Ancient Romans figured out how to make concrete resilient and sustainable—the evidence remains standing today (Figure 3, page 26). However, specifying the physical properties of exposed concrete flooring seems to remain a nebulous challenge. This is primarily because the industry has not had a clear way of quantifying the exact definition of polished concrete.
According to the International Polished Concrete Institute (IPCI):
Polished concrete is a process which enhances the natural beauty of existing concrete by hardening and applying a sheen to the concrete. There are two primary methods to create this sheen: Topical or Mechanical.
However, this can be vague. Traditionally, it has been entirely up to the contractor to deliver a shiny floor by means of a prescribed process, but polished concrete is not simply “a shiny floor.” There are inherent understandings in polished concrete’s performance such as abrasion resistance, stain resistance, coefficient of friction, and life cycle maintenance. The owner is not only expecting a shiny floor. Who is to argue, given a vague specification focused only on esthetics which prescribes a process rather than a quantifiable and verifiable result? Polished concrete also requires more than esthetic benchmarks to protect against substitutions.
Defending design intent
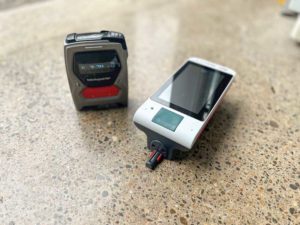
The goal is an esthetically pleasing, durable, easily maintainable, slip-resistant, sustainable, and resilient floor. Taking the steps explored in the following section, these attributes can be established by way of the specifications and verified in the field.
Esthetically pleasing
It takes a good slab that has been placed correctly to get controlled results. Flatness is important—one will not be able to get an even and consistent appearance if the slab is wavy and improperly cured. This is particularly true when a “cream” finish with minimal aggregate exposure is desired.
Aggressive grinding, at additional expense, to expose more aggregate can even out the appearance, but does not guarantee the desired look. In fact, it forces the owner to accept another level of aggregate exposure. Sheen is also an esthetic that can be achieved ranging from a dull/matte finish to a highly polished/mirror-like glossy finish. Of course, the shinier the finish, the more noticeable the flatness. However, it is important to keep in mind “shiny” is not the definition of polished (or refined) concrete; in many cases, a highly reflective finish is inappropriate. For example, a highly reflective floor in a restroom compromises privacy between stalls.
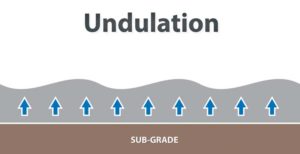
By specifying the industry standard for floor flatness and floor levelness, ASTM E1155, Standard Test Method for Determining FF Floor Flatness and FL Floor Levelness Numbers, an appropriate degree of flatness may be specified to suit the function and esthetic of a space. Higher flatness/levelness numbers are easier to achieve with better concrete curing, and for polished concrete, this generally means wet curing or internal curing with nano silica-based supplementary cementitious materials (SCMs) (hydro cements, nano infused cements [NIC], certain colloidal solutions, etc). Using a standard cast-in-place specification will also potentially land a project in trouble, as those slabs are not generally built to maintain higher standards in Ff/Fl. Specifiers may also want to expand their approach with Ff/Fl benchmarks by expanding language to account for smoothness.
Early methods of specifying exposed concrete surfaces were based on “grit levels,” and then later measuring reflected light (and its clarity) from the floor. However, this has proved too subjective, often unintentionally distorting original design intent with Division 09 coating substitutions also able to meet these benchmarks. While gloss measurements are useful in understanding esthetic benchmarks, measuring the surface refinement of the concrete itself requires taking measurements of the surface with Averages Roughness (Ra) measurements. With the help of standards like ASME B46.1-2009 (R2002), Surface Texture (Surface Roughness, Waviness, and Lay)3 easy to measure physical benchmarks helps create a common language and direction for specifiers, contractors, and the entire project team. As an example, a project could require a minimum Ra of 0.6 to 0.4µm (24 to 16µin) on flat polished surfaces, 0.9 to 0.7µm (36 to 28µin) for inclined polished surfaces and then select a sheen and image clarity level from ASTM D5767-18, Standard Test Method for Instrumental Measurement of Distinctness-of-Image (DOI) Gloss of Coated Surfaces, to satisfy certain esthetic requirements (matte finish 10 to 45 per cent, semigloss 46 to 75 per cent, glossy 76 per cent and higher). Now, the design decision-maker and contractor have a familiar, quantifiable language to not only express design intent, but also ensure it has been met.