Architectural aluminum goes green
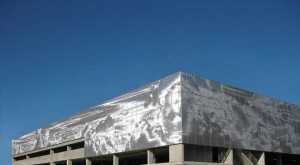
Photos courtesy Dri-Design
The coatings are created from the substrate itself, integral to the part on which they form. The anodize process passes a direct electric current between the aluminum and the electrolyte, with the aluminum acting as the anode. This procedure mimics the natural oxide film, but results in a thicker, more controlled formation of a durable oxide film. The process also contains no VOCs, making it a light-fast, durable alternative to high-VOC paints and organic coatings. Further, anodized aluminum is 100 per cent recyclable, lending itself to post-consumer recycled content during demolition or restoration of the building.
Architectural anodize finish provides excellent wear and abrasion resistance with minimal maintenance in most environments; it resists the ravages of time, temperature, corrosion, humidity, and warping. Anodize should also meet AAMA 611-98, Voluntary Specification for Anodized Architectural. This standard requires anodize finishes to meet rigorous testing performance standards, including 3000 hours of salt-spray resistance.
Unlike other finishes, anodize is an integral part of the substrate and therefore highlights aluminum’s metallic appearance. To help conceal some of the irregularities in aluminum, some anodizers have changed to an environmentally responsible process that involves a change in the anodize etch chemistry, from a traditional caustic etch with a pH of 12+ to a more neutral, frostier etch with a pH between five and six. Etching is an important step during the anodize process; it is designed to dissolve a thin layer on the surface of the aluminum to develop a smooth uniform finish. The result is an esthetically appealing, frostier, matte finish that helps hide small defects, such as the die lines, flow lines, minor corrosion, and scratches that may occur.
Other benefits include:
- secondary billet can be successfully anodized, contributing to recycled material content for LEED and other programs;
- reduced glare in bright sunlight (gloss level reading is reduced from 15 to 25 with conventional anodize, down to a gloss level of 3 to 12 with the ‘eco-friendlier’ anodize process);
- anodize etch process has the viscosity of water and will not collect in the small recesses of aluminum extrusions or narrow aluminum tubes, enhancing the finished product’s durability and lifecycle; and
- anodize process can reduce landfill waste that is used with conventional etch processes by 75 to 80 per cent (waste directly relates to GHG production).
Taking advantage of anodized aluminum benefits and technological innovations, the Parkade at Calgary’s Southern Alberta Institute of Technology (SAIT) used an advanced software system to sculpt 3-D images into its metal panels. The 1394 m2 (15,000 sf) of aluminum panels, shown above, are 100 per cent recyclable and finished in a clear anodize.
The Ombrae Imaging Technology used at SAIT calculates the optimal reflective position for each pixel of an image and punches it into the panel system. For the project, these punched pixels reflect controlled light to form images of clouds and sky. Designed by Bing Thom/Marshall Tittemore Architects, the resulting structure conveys a connection and a feeling of preserved landscape between the campus and downtown Calgary.
Repair and restoration
With its inherent corrosion resistance, the ability of aluminum to maintain structural integrity has been documented for decades. However, daily operation and occupation of a building storefront and other high-traffic areas may need to be periodically repainted. As good as it is, painted and anodized aluminum is not completely maintenance-free, nor does it last forever. Painted aluminum can chip and scratch on high-wear areas such as sliding doors and entrance ways.
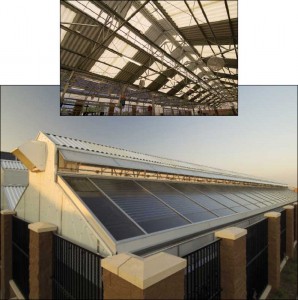
Photos courtesy Wal-Mart Stores Inc.
A building’s finish can become faded and discoloured after years of prolonged UV exposure, particularly if a PVDF coating was not used. In other cases, a new colour can be required as a result of a company brand change. Regardless of the reason, for any repair other than a small scratch or blemish, it is strongly suggested a licensed, professional, field service applicator of PVDF air dry systems (ADS) inspect the situation and determine the best suitable paint or repair procedure.
Onsite repair, refinishing, and restoration of architectural projects requires special equipment and an exceptional knowledge that only comes with years of experience. As even a minor mistake in any segment of repair can cause major problems over time, every step must be meticulously executed to ensure a long-lasting, field-applied finish including:
- meticulous surface preparation to remove dirt and mildew;
- sanding and buffing of minor scratches and defects;
- sandblasting for heavily-corroded areas;
- masking and protection to prevent overspray from contact of any non-finish areas;
- scuff-sanding the repaint area in order to provide an enhanced level of mechanical adhesion;
- solvent wipe to remove contaminants from the preparatory method;
- applying primer to bare metal; and
- using PVDF ADS coatings with a spray applicator.
PVDF ADS offers the same superior weathering properties as PVDF finishes and can be field-applied on almost any building material, restoring surfaces to last and look like new. PVDF ADS resists marring and abrasion, withstands airborne pollution without staining or discolouring, and retains appearance over time, just as the factory-applied equivalent. These coatings require little maintenance and can be easily cleaned with mild detergents.
A new, environmentally sensitive fluoropolymer coating system for onsite repair and restoration of architectural aluminum is being introduced. The proprietary formulation is water-based and created to meet the interior specifications for the Green Sea Environmental Standard and LEED, offering very low-VOC content.
According to EQ Credit 4.2, Low-emitting Materials–Paints and Coatings, architectural paints and coatings applied to the interior must not exceed the VOC content limits in Green Seal (i.e. GS-11 and GS-03) and South Coast Air Quality Management District (SCAQMD) Rule #1113. Along with the paint, any primer and cleaners must also fall within the LEED guidelines.
Beyond LEED, more communities and individuals are voicing their concerns about the chemicals and particulates used in restoring and renovating the interior of homes, schools, offices, and public spaces. Examples include:
- preservation projects with historical artifacts;
- healthcare facilities with sensitive medical equipment and patients with compromised immune systems; and
- residential and office towers with occupants reluctant to be relocated during renovations. These are the types of projects where property owners and managers should insist on finishing applicators certified in environmentally responsible practices.
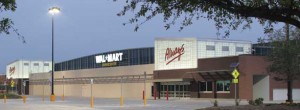
Regarding warranties
Due in large part to advances in esthetics and performance of architectural coatings, today’s buildings are looking better and lasting longer than ever. Even with this progress, the most sophisticated coating systems have the possibility to corrode, lose their gloss or colour, or crack and peel if the aluminum is not properly manufactured, applied, or installed, or if they are exposed to environmental hazards on location. Fixing these problems can cost millions of dollars. Coating warranties provide security and protection to building owners, architects, and specifiers from these types of failures.
For projects within North America, the most important warranty terms and conditions—those related to weathering—are outlined in voluntary standards published by AAMA. While anodize finishes may be warranted up to 10 years, and 70 per cent PVDF paint finishes up to 20 years, many more years of service life usually can be expected. The AAMA standards are tested in the most extreme conditions possible for adhesion, gloss, chalk, and fade. The testing grounds are in south Florida where the sun, salt, air, and humidity are among the most challenging on the continent.
The first, and one of the most important, defences against paint problems is proper pretreatment of the aluminum. Without this step, premature failure of the finish system can almost be guaranteed. Paint systems are designed to be applied over clean, pretreated metal. The most time-tested, proven pretreatment system for architectural aluminum products is a chrome phosphate conversion coating.
Offering the longest lifecycle, chrome phosphate conversion coatings continue to be recognized by coating manufacturers as the most effective, robust pretreatment for aluminum. As a result, products installed along the seacoast and other harsh industrial environments frequently have additional terms and requirements.
When reviewing a warranty document, one must verify whether each performance standard is covered through the warranty’s specified length, or if it is a gradual declining warranty with payout obligations reducing through the years. Warranty documents will most likely require care and maintenance in scope with AAMA 609 and 610-09, Cleaning and Maintenance Guide for Architectural Finished Aluminum specification.
All architectural coatings will accumulate dirt and grime, with the amount depending on the building’s environmental conditions, location, and finish. The frequency of cleanings will be required more often on the seacoast or in a heavy industrialized area as compared to a rural, centralized location. AAMA suggests routine aluminum cleaning schedules be integrated with other cleaning schedules for both efficiency and economy.
Painted material
When selecting a cleaning solution, one should use mild soap solutions safe for bare hands—the sort of products one would use to wash a car. Strong acid or alkali cleaners must be avoided as they may damage the finish.
Solvents or emulsion cleaners, no stronger than mineral spirits or denatured alcohol—and spot-tested and found safe—may be used to remove grease, sealants, or other materials. Cleaners should never be mixed as the result can have a harmful outcome. Abrasive cleaners or materials (e.g. steel wool or abrasive brushes) should be avoided as they can harm the surface.
Once heavy soil, grease, or sealant is removed, a mild soap solution should be applied with a cloth, sponge, or soft brush. The surface must then be thoroughly rinsed with clean water and dried with a soft cloth.
Anodized material
Much like painted surfaces, an anodized finish should be cleaned using mild soap solutions to retain its original beauty. Products safe for use with bare hands, including most commercial cleaning products, can be used. The cleaning solution should be applied with a soft cloth, sponge, or brush; strong acid or alkali cleaners must be avoided.
Severely soiled, anodized surfaces can be cleaned a little more aggressively than painted surfaces. For example, slight scuffmarks and rub marks on an anodized surface can be removed with a mild abrasive pad, and then cleaned using the mild soap solution. (The surface must be thoroughly rinsed with clean water and dried with a soft cloth.)
Conclusion
With minimal maintenance, finished architectural aluminum will retain the intended look and long life, while providing the desired performance in the harshest environments, including Canada’s cool climate and geographic diversity. These qualities help reduce the need to replace materials and components, which conserves resources, saves money, and preserves a productive, comfortable space for building occupants.
Tammy Schroeder, LEED GA, serves as the senior marketing specialist for Linetec in Wausau, Wisc. As an applicator of all architectural finishing technologies—paint, powder coat, and anodize—the company provides educational resource and advice to ensure the best finish for aluminum building products and metal construction projects. With a decade of experience in paint and anodize finishing, Schroeder develops and maintains Linetec’s American Institute of Architects/Continuing Education System (AIA/CES) and other educational presentations. She can be contacted via e-mail at tammy.schroeder@linetec.com.