Applying the carbon equation to insulating glass units (IGUs)
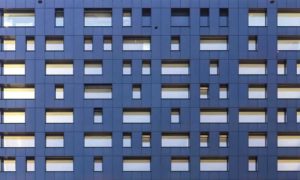
For building projects, IGUs are then fabricated with configurations (e.g. lite thicknesses, cavity size, number of cavities) based on the needed wind and snow load, impact resistance and safety requirements, and the thermal and acoustical targets of the project. Service loads (e.g. wind, snow, impact) determine the lite thicknesses based on the largest unit. The acoustics and thermal performance determine the size and number of the cavities. The resulting IGU configuration is then applied to all IGUs in the project, whether large or small (Figure 7).
This current design approach can result in small, stiff IGUs alongside larger IGUs with more flexible lites. For example, in some curtain wall designs where the typical repeated module width is 1.5 m
(5 ft), the modules at the transition to the opaque wall on each side may be narrower.
Depending on the size of these environmental loads and the stiffness of the smallest units, the resultant edge seal loads may be greater than the loads at which the edge seal was qualified in the durability tests, adding risk to the service life.
However, the impact of climate loads on IGU edge seals is not routinely evaluated in projects, so these potential risks are not typically identified nor mitigated. A recommended procedure for evaluating edge seal loads relative to the qualification loads has been proposed by the author along with Adam Nizich in a paper they co-authored.5 Their proposal is summarized in the following section.
How to design for climate load
The following steps provide an outline for assessing the edge seal forces for IGUs in project applications and identifying whether action is needed to adjust the IGU configuration, size, or edge seal dimensions to reduce these environmentally induced strains to a level qualified to the standard IGU weathering tests. Typically, this evaluation may be done by a building envelope consultant or by the IGU fabricator. It is recommended that specifiers ask for such an analysis. Decisions on how to address any potential risks are likely to be made collaboratively, because of the impacts on design esthetics, cost, and risk.
- Identify stiffest units. Review the fenestration schedule or project take-off to identify the smallest and narrowest IGUs. These will typically be the stiffest units. Bent IGUs or those with atypical supports may also have high stiffness.
- Estimate maximum environmental loads:
- First, estimate the temperature and barometric pressure conditions under which the IGUs were manufactured.
- Second, estimate the expected in-service low and high cavity temperatures and pressures the IGU will experience. Consider the impact of absorbing coatings and tints, spandrel insulation, and solar orientation. Lawrence Berkeley National Laboratory’s “Window” software provides the capability to effectively estimate cavity temperatures under a range of environmental conditions.
- Third, calculate the change in temperature and barometric pressure from as manufactured to in-service conditions.
- Lastly, calculate the cavity pressure prior to any partial pressure equalization. This is the pressure that would be exerted if the glass is not able to deflect and stays rigid. This is often called the “isochoric pressure.” The calculation is done by converting the change in temperature and/or altitude to a change in pressure at a fixed volume using the ideal gas law.