Applying the carbon equation to insulating glass units (IGUs)
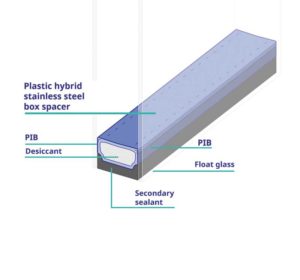
Since the operational carbon and comfort benefits of IGUs are needed in buildings, focus should be placed on specifying to maximize IGU lifetime. Several factors affect an IGU’s lifetime:
- Edge seal material choice and design.
- Climate stresses and other application-specific loads.
- Manufacturing quality.
- Installation quality and conditions.
IGU seal design considerations
Contrary to popular belief, the IGU seal is not hermetic. The service life of an IGU is primarily determined by how long its edge seal can prevent moisture accumulation between the lites of glass. There is always a finite moisture permeation through the seals, which is absorbed by the desiccant held within the spacer of the edge seal. The IGU fails when the absorption capacity of the desiccant is used up.
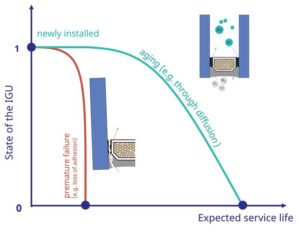
In noble-gas-filled units, gas loss can occur over time via diffusion through the edge seals. While gas loss reduces thermal performance, it does not result in a noticeable unit failure, since the main function of the window—the ability to see through it—is still maintained.
The goal for IGU design is to minimize the rate of moisture ingress and gas loss over time by creating a robust edge seal design that is resistant to degradation from environmental stresses. The edge seal design includes choices of spacer, primary and secondary sealants, and desiccant, including the quality and quantities of these materials used. These are critical to the seal’s moisture permeation performance over time (Figure 4a). The design must also be appropriate to support consistent, high-quality manufacturing, and the units must be installed properly to maintain service life (Figure 4b).
Material choice
Although there are several options for secondary sealants (e.g. silicone, hot melt butyl, polyurethane, polysulfide), the typical secondary sealant of choice for IGUs being used in non-residential applications in North America is silicone. This is because of its structural strength and high resistance to ultraviolet (UV) radiation, high temperature, and water exposure, which is optimum for these more demanding applications.
While having great durability and strength, silicone has high water vapour and argon gas transmission rates. This means the primary seal, and particularly the spacer, must have excellent vapour- and gas-barrier properties, since there is no secondary barrier as a back-up.
The presence of a solid metal vapour barrier as part of aluminum, stainless-steel, and plastic hybrid stainless-steel (PHSS) box spacers is one of the reasons these spacer types have become the benchmark for durability in North American commercial IGUs. Another benefit of solid metal vapour barriers is their adhesion to silicone. Adhesion is important for several reasons:
- Without good adhesion, water vapour can travel through silicone and condense next to the primary seal. Water will then degrade the primary sealant and cause a failure.
- For flexible spacers, good sealant adhesion prevents the spacer moving into the cavity as the lites move under climate loads.
- Adhesion to the back of the spacer and the two glass lites create a three-sided edge bond which is much stiffer than a two-sided edge bond (Figure 5). As a result, under climate loads, a three-sided edge bond results in a smaller strain on the primary seal under climate stress, reducing water vapour and gas transmission, with an expected positive impact on service life.
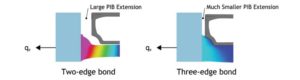
In addition, PHSS warm-edge box spacers deliver the same thermal performance improvement to fenestration systems as spacers made of only non-metals which do not have a solid metal vapour barrier. Typically, a PHSS warm-edge spacer will deliver a fenestration U-factor reduction of 0.1 to 0.2 W/m2K (0.02 to 0.03 Btu/F•hr•sf) in edge captured systems, or up to 0.3 W/m2K (0.05 Btu/F•hr•sf) in structurally glazed curtain wall systems. It is an easy, low-cost strategy to improve thermal performance and condensation resistance and to meet increasingly stringent code requirements.
An important takeaway is that for edge seals using silicone, the vapour barrier of the spacer is a critical component. The IGU edge seal should be considered as a system with components that work together to deliver performance. Swapping out components (e.g. spacer) without evaluating the impact with the particular sealant system (especially when using silicone) can have negative consequences for service life.