Applying the carbon equation to insulating glass units (IGUs)
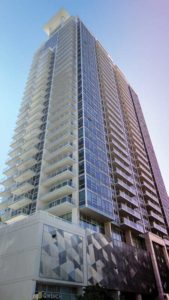
By Helen Sanders, PhD
Embodied carbon, or upfront carbon emissions, is the amount of CO2 or equivalent emitted during raw material sourcing and product manufacturing. Minimizing embodied carbon emissions is critical because of the time-value of emissions, since earlier emissions have the most impact on planetary warming. Operational carbon—the emissions from the operation of the building—can be reduced over time through improved efficiency and grid-decarbonization, but today’s embodied carbon emissions, will be warming the planet for centuries to come.
Building lifetime and components’ service life are often-overlooked drivers of low-carbon design. Replacing components frequently compounds embodied carbon emissions, and operational carbon performance is only as good as their lifetime and can degrade over time. Specifiers can have a significant impact on building component service life through careful architectural specifications.
Since its introduction, insulating glass units (IGUs) have provided significant reductions in operational carbon emissions from buildings—yet, they increase the embodied (upfront) carbon. This is because the amount of energy (and carbon) intensive glass used is doubled in an IGU compared to monolithic glass and the service life is significantly reduced from many hundreds of years to 20 to 40 years. Since it must be replaced more often during the building’s life cycle, it adds to the carbon emissions debt that has to be repaid by operational carbon savings during its service life (Figure 1). Glass is an energy- and carbon-intensive material since it is made in a high-temperature gas-powered process, which is challenging to electrify.
The graph in Figure 2 illustrates the embodied carbon investment per square metre (square foot) of glass for a building with a 50-year service life, comparing monolithic 6-mm (0.25-in.) glass, monolithic heat treated 6-mm (0.25-in.) glass, a dual-pane IGU with a low-e coating, and a triple-pane IGU with one low-e coating. The IGUs must be replaced once during that period, whereas the monolithic glass does not need replacement. Reduced IGU lifetime increases the frequency of replacement, leading the total lifetime carbon to rise as well.
That is not to say monolithic glass is a better choice than dual-pane IGUs on a life cycle carbon basis, and other factors such as occupant comfort and thermal resiliency need to be considered. Using dual-pane IGUs rather than single-pane glass typically results in lower total life cycle emissions, since the operational emissions saved outweigh the upfront emissions investment, given a sufficiently long service life. Also, when replacing single-pane windows with double-pane units in a retrofit, there is generally a fast embodied carbon payback through operational emissions reduction.1 However, the embodied carbon payback through reducing operational emissions in moving from double- to triple-pane glazing is more varied and not always positive.
It depends on the climate zone, the building and base-case performance, and relative service life assumptions and, where there is a payback, it can also be much longer.2 Also, for any life cycle carbon assessment, if the as-built IGU lifetime performance deviates substantially from the assumed IGU lifetime, then the payback evaluation will be incorrect.
The service life of IGUs is therefore an important driver of building life cycle carbon emissions. Specification choices that preserve and/or extend expected IGU lifetime are sound long-term investments for reducing total life cycle carbon emissions.
Figure 3 illustrates the relative embodied carbon impacts of the processes used to create a dual-pane IGU.3 The float glass production itself is responsible for 75 per cent of the embodied carbon, with approximately 12 per cent coming from the heat treatment process. The insulating glass process contributes approximately 10 per cent to the embodied carbon, with half of it coming from the materials (e.g. spacer, sealants, desiccant) and the other half coming from the electricity to run the equipment.
While the impacts of the IGU process on embodied carbon are minor, the design and quality have a much more significant impact because of the service life. Adding more edge seal material, and wisely choosing components and designs has a significant positive change on service life, but a minor difference on the embodied carbon at the point of manufacture.
The specified slider does not exist.