Applying coating systems for labs
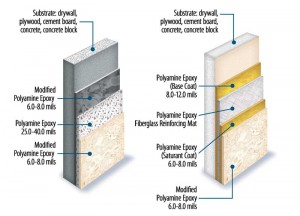
Image courtesy Tnemec Company
The critical areas required placing a fibreglass reinforcing mat into a bedding coat of 100 per cent solids polyamine-cured epoxy roller-applied at approximately 0.2 to 0.3 mm (8 to 12 mils) dry film thickness (DFT) while still wet. When placing the fibreglass mat into the bedding coat, its edges were butted together rather than double-cut after placement. Broad knives, trowels, or wallpaper brushes were used to smooth the fibreglass mat and force any air pockets out from behind it.
A second coat of 100 per cent epoxy resin was roller-applied at approximately 0.2 to 0.3 mm DFT to completely wet-out and saturate the reinforcing mat. After the coating had cured hard, it was pole-sanded with 50-grit resin-coated sandpaper to remove protruding fibreglass strands or imperfections. For additional abrasion resistance and enhanced colour and gloss retention, a topcoat of low-odour, low-VOC ceramic-modified waterborne polyurethane was applied.
Interior overhead drywall and less critical wall areas in the facility received the same coating system, but without the fibreglass mat reinforcement. The primary reason for using a 100 per cent solids epoxy coating system over high-impact drywall and wallboard is to offer additional protection against physical abuse or from frequent cleaning typically performed with mild chemicals, rags, or sponges. Such applications are usually limited to dry environments where moisture is unlikely to come in contact with the drywall, wallboard, or joint-treating compound, which could result in a breakdown of the substrate.
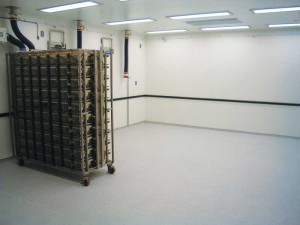
Photos © David Walker. Photos courtesy Avid Protective Products
Attention to details with choice of substrate is important at this juncture, as the cost of redoing critical animal areas is too high while research is being performed on animals operating within specific testing guidelines. The wrong substrate and coating system selections could jeopardize months of testing protocols that have been established for animals in these spaces.
Attention to metal doors and window frames and how they are detailed to the wall system was also important for MACF. Leaving leading edges of door frames exposed for clean termination is required to maintain cleanliness standards of the facility. These locations were coated with two coats of waterborne urethane as applied to the wall finish. All metal doors and window frames in the facility were coated with two to three coats of epoxy. A modified polyamine epoxy was trowel-applied to the flooring at 6.4-mm (¼-in.) thickness, followed by a coat of polyamine epoxy. Operating room floors also received a topcoat of an extremely hard, chemical-resistant aliphatic polyester polyurethane for added stain and chemical resistance.
University of Toronto
A fibreglass mat-reinforced coating system was specified for the walls of critical research areas at University of Toronto’s (U of T’s) Terrence Donnelly Centre for Cellular and Biomolecular Research. The award-winning facility offers a collaborative laboratory and classroom environment dedicated to research in bioengineering and disease.
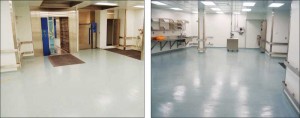
Walls in critical research areas were coated with a fibreglass mat-reinforced system roller-applied over an epoxy-modified cementitious resurfacer and prime coat of polyamine epoxy. The remainder of the block walls and cement-board ceilings were coated with waterborne cementitious acrylic filler and finished with two to three roller-applied coats of a high-build, low-odour waterborne acrylic epoxy. All voids in the face of the block and mortar joints were filled to create a smooth, seamless surface before the protective coating system was applied.
In the facility’s cage washroom area––which is exposed to frequent steam-cleaning, wash-downs, and chemicals––the fibreglass mat-reinforced wall coating system received a topcoat of an extremely hard, chemical-resistant urethane. Wash-down room floors were coated with a polyurethane modified concrete topping designed to perform under extreme temperature changes, followed by a clear novolac epoxy, and a topcoat of extremely hard clear urethane for increased abrasion and chemical resistance.
Surgery room floors received a layer of modified polyamine epoxy, trowel-applied at 6.4-mm thickness, followed by a durable polyamine epoxy used to seal the mortar and build thickness. An extremely hard, chemical-resistant polyurethane finish was applied as a topcoat for added abrasion resistance and colour and gloss retention.
The Donnelly Centre has been recognized with a Royal Institute of British Architects (RIBA) International Award, the Ontario Association of Architects (OAA) Award of Excellence, and the Business Week/Architectural Record Award, recognizing the most successful collaborations between architects and clients.
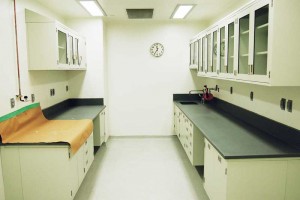
Surface preparation
Applying spray-applied or mat lay-up fibre-reinforced wall coating systems over common wall substrates requires proper surface preparation. Cement board is commonly encountered in research facilities and hospitals, such as Tufts Medical Facility in Boston, Mass., where a fibreglass mat lay-up coating system covers more than 3700 m2 (40,000 sf) of wall surface.
Since the face of cement board is porous, double priming with a high-solids moisture-tolerant polyamine-cured epoxy helps smooth the substrate to create a pinhole-free surface. Joints and screw holes also need to be properly treated using 100 per cent solids epoxy filler and surfacer or epoxy-modified cementitious mortar.
Both poured and precast concrete substrates should be prepared in accordance with Society for Protective Coatings (SSPC) SP13/NACE International No. 6, Surface Preparation of Concrete, by abrasive blasting or mechanically abrading the surface to remove laitance, form-release agents, curing compounds, hardeners, sealers, and other contaminants. (This comes from NACE Publication 6G191, Surface Preparation of Contaminated Concrete for Corrosion Control. Also see SSPC’s Guide No. 11, Guide for Coating Concrete). Laitance is a thin, weak layer of aggregate fines and non-reactive cement residue loosely bonded to the substrate. When coated over, this surface defect can compromise the coating system’s long-term adhesion. Removing laitance is critical before the application of any coating.
Concrete masonry units—commonly specified for walls in vivarium and animal care environments in the biomedical field—have surface voids and mortar joints that need to be filled before applying a fibreglass mat-layup system. This can be achieved through use of 100 per cent solids epoxy resurfacing material or modified cementitious mortar to parge the CMU’s entire surface. Depending on the block’s porosity and depth of the tooled joints, the parge coat is applied at an approximately 1.5-mm (1⁄16-in.) nominal thickness.
At the Merck Research Facility in Boston, Mass., a fibreglass mat-reinforced coating system covers more than 37,000 m2 (400,000 sf) of CMU substrate. Similar wall coating systems were used on CMU surfaces on nearly 16,300 m2 (175,000 sf) at the Genetics Institute’s Wyeth Building T Project, 7900 m2 (85,000 sf) at the Massachusetts Institute of Technology (MIT) Brain Cognitive Research Facility, and 3716 m2 (40,000 sf) on the MIT Koch Research Building in Cambridge. Brock University in St. Catharines, Ont., is currently installing these coating systems as well.
David Walker, BBA, MBA, NACE, is the owner of Avid Protective Products, a representative of Tnemec Company in Oakville, Ont. With more than 20 years of experience in the protective coatings industry, he is a NACE International-certified coating inspector and belongs to both the Society of Protective Coatings (SSPC) and the American Water Works Association (AWWA). Walker serves on many AWWA coating standards committees. He can be contacted via e-mail at avid@bell.net.
Greg Pope, NACE, is a coating consultant at Righter Group Inc., a representative of Tnemec Company in Wilmington, Mass. As a NACE International Level 2 coating inspector, he has more than 30 years in the coating industry and works with technologies for the architectural, water, wastewater, hydropower, and petrochemical refining industries. Pope’s technical expertise includes detailed knowledge of specification writing, surface preparation, and material application methods. He can be reached at gpope@rightergroup.com.