An end to throwaway building envelopes
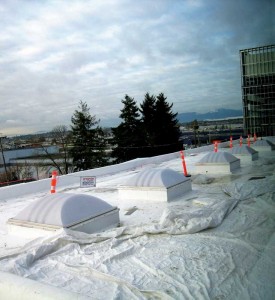
Gold (i.e. 50 to 99 years) should be the target for residential, commercial, office, and institutional LEED buildings. It should also be the goal for high-rises requiring extensive use of scaffolding and the potential for costly repairs.
For the roof portion of the envelope, a Silver BER target of 30 years is achievable; some industry suppliers can back up the roofs with warranty protection lasting this long. The wall part of the building envelope should be at least equal to the roof. Therefore, a Silver BER target should be specified, using pre-painted metal wall assemblies, as an example. Better yet, one could consider specifying a Gold BER target of 50 years by, for instance, using natural stone and curtain wall in a rainscreen configuration.
It is important to know, however, that RP Credit 1 allows building envelopes to have only 50 per cent of design service life for two CSA categories:
- costly repeated (failure category 4)—examples include face-sealed wall assemblies, which may be problematic for high-rises as regular maintenance is recommended; and
- costly repair (failure category 5)—examples include concealed barrier wall assemblies, which may be problematic for owners unaware of potential problems of structural deterioration, uncontrolled air/water, and condensation when regular maintenance is not practised.
Energy use intensity (EUI) targets can also be important to specify at the concept stage, as utility costs cannot be reduced unless the building’s consumption is measured and managed. To establish an appropriate EUI, one can specify a target consistent with good industry practice in terms of the standard measurement in kWh/m²/year. In Ontario, at minimum, a target should be derived from the three options in OBC effective (or, for other jurisdictions, the prevailing code):
- prescriptive approach—American Society of Heating, Refrigerating, and Air-conditioning Engineers (ASHRAE) 90.1-2010, Energy Standard for Buildings Except Low-rise Residential Buildings, with minimum R-values and other requirements;
- performance approach—ASHRAE 90.1-2010 plus five per cent; or
- 1997 Model National Energy Code for Buildings (MNECB) plus 25 per cent.
Improved energy-efficient building envelope (e.g. quick-installed insulated metal panels [IMPs]), lighting, and HVAC systems are recommended and a higher-performance EUI target should be considered. For offices, rather than target an average EUI of 170 kWh/m²/year, a target EUI for a 50 per cent reduction to 85 kWh/m²/year or more is possible. Significant improvements in the building envelope at the time of construction or system replacement are possible. For example, vacuum insulated panels (VIPs), with an insulation value of more than R-60 per inch (RSI 10.56 per inch) are available and are being studied at the National Research Council’s Institute for Research in Construction (NRC-IRC’s) Ottawa campus as part of a roof replacement.
Applications of VIPs that are thinner and provide superior condensation and mould resistance, along with higher-performance exterior walls, are being researched. Implementing the lessons learned with these types of innovative technologies can significantly lower the building’s EUI, resulting in higher energy cost savings and resale values.
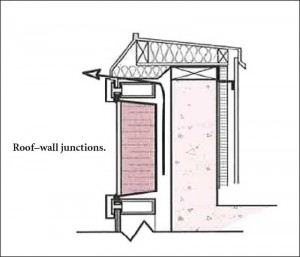
Image courtesy Tarion/MAH
3. Better building detailing
Improved building envelope detailing is mandatory for achieving better durability and energy efficiency. CSA S478 quality assurance (QA) activities include review of details for the envelope, HVAC, and other systems. For the building envelope, it is extremely important wall/roof interfaces and penetrations (e.g. windows and doors) be detailed to prevent premature deterioration and interior damage due to air and water leakage. There are examples available from CMHC and the aforementioned High-rise Condominium Construction Guide.
Additionally, architects, building science professional engineers, and major system suppliers can develop specialized details that work to achieve material compatibility between critical components in building envelopes. This will help achieve BER Platinum, Gold, and Silver targets.
It is also important to review details with the subcontractors at a preconstruction meeting to determine sequencing and tweak the details with the trades to improve constructability and reduce the need for rework.
4. Field review
Periodic third-party quality field reviews and audits of building envelope construction are good ways to ensure construction conforms to the details. Air barriers, insulation levels, and vapour retarder installation can be checked. Inspections by system suppliers (usually at no additional cost) will provide checklists. These help guide subcontractors to make any necessary repairs so good installations and full warranty coverage are provided.
Focused testing of critical components such as windows and doors for air/water penetration before completing construction is essential for the predicted service life to match the design service life. This author has worked on several landmark buildings where third-party field reviews and commissioning tests meant corrective actions were completed before leaks (and health-related damages) occurred. By completing these major corrective actions before turnover, there was no repair cost to the owners and bigger, future problems were prevented.
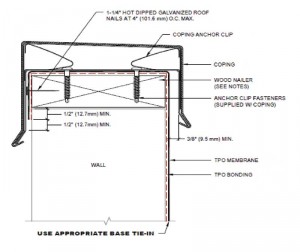
Image courtesy Firestone Building Products
5. Documentation by professionals
It is important to know many municipalities do not mandate Letters of Compliance for Part 5, as this is not an OBC requirement. Additionally, for Part 12 (“Energy Efficiency”), documentation of OBC compliance is not usually required. Partially as a result of the B.C. leaky condominium crisis, Letters of Compliance are required in the British Columbia Building Code (BCBC) and in Vancouver from professional engineers and/or architects to show the plans and supporting documents (including details and specifications) substantially comply with the code.
While many municipalities do not require these documents, it is still critical to have third-party professional Letters of Commitment for design/field review and code compliance provided. This helps reduce one’s risks before the money is turned over.
Conclusion
Following these five simple suggestions can help ensure building owners achieve the durability and energy efficiency they expect of their facilities. By specifying an appropriate building envelope rating and energy use intensity target, along with having documentation by professionals, a project team can have peace of mind, prevent throwaway construction, and protect its collective chequebook.
Bob Marshall, P. Eng., BDS, LEED AP, has been appointed to the National Research Council’s (NRC’s) Task Group on Energy Targets. He is Canada’s appointed expert on the International Organization for Standardization (ISO)/TC 163-TC 205 WG4, and a voting member for TC 163/SC 2 on calculation methods. Marshall chaired the U.S. Green Building Council’s (USGBC’s) Greenbuild 2011 ‘Best of Canada’ stream of educational seminars and is a member of the council’s education committees. He is a senior consultant at Yolles, A CH2M HILL Company in Toronto. Marshall can be contacted via e-mail at bob.marshall@halcrowyolles.com.