An end to throwaway building envelopes
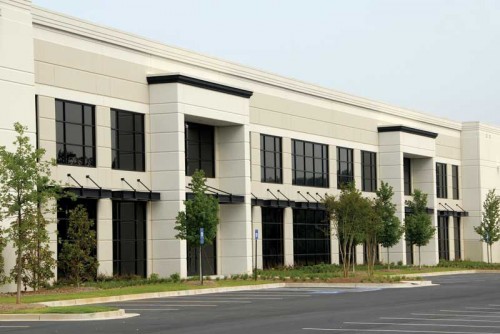
By Bob Marshall, P. Eng., BDS, LEED AP
When it comes to engineering its buildings, Canada has made great strides in durability and energy efficiency requirements with respect to codes and programs such as Leadership in Energy and Environmental Design (LEED). Unfortunately, despite these green leaps, it seems the basic lessons learned over the past decade or so still have not been applied to most building envelopes. In other words, we have structures designed to have service lives of 50 to 100 years, with enclosures only equipped to last for 10 to 15 years.
Even though ‘at-minimum’ laws are in place to provide resistance to deterioration, there are still significant costly premature failures. In British Columbia, less than 50 per cent of the leaky condominiums, part of a $1.5-billion class action, have been repaired. Now, failures reported in the media are suggesting some Ontario condominiums have inefficient glass walls and poorly designed building envelopes susceptible to premature problems. The legal fallout could well exceed its West Coast counterpart. What are the basic strategies for achieving envelope durability and energy efficiency, preventing ‘disposable’ or ‘throwaway’ buildings?
Last October, a Greenbuild session in Toronto on commissioning clearly showed the majority of participants believed in the importance of this quality verification process. Since January 2007, Part 5 of the Ontario Building Code (OBC) has mandated envelope assemblies be in accordance with good practice such as Canadian Standards Association (CSA) S478, Guideline on Durability in Buildings. Further, as of January 2012, there are higher energy efficiency requirements in the code. Nevertheless, energy-inefficient, predominately glass towers continue to be built. To prevent durability failures and energy waste, it is essential to apply five basic lessons learned from the advanced state of green building to all buildings.
1. Smart financial strategy
To achieve a sensible financial strategy, building owners can look at previous failure trends to prevent major payouts. From 1984 to 1994, Tarion Warranty Corporation—which issues warranties on Ontario’s residential construction—had about $23 million in high-rise claims. (Additional costs paid by builders and owners would be significantly higher.)
This author chaired a steering committee that focused on identifying solutions to the key causes of high-rise building failures based on 1991 research of 52 buildings. Most of the claims were related to moisture problems with the envelope rather than structural concerns. The main causes were missing and bad details, along with inadequate inspections. Tarion’s High-rise Residential Construction Guide was co-published in 1995 with the Ontario Ministry of Municipal Affairs and Housing (MAH), and is referenced in the appendix of OBC and the National Building Code of Canada (NBC) to help prevent claims.
In 2001, the Canada Mortgage and Housing Corporation (CMHC) undertook a research study to gain a better understanding of key failure areas that resulted in financial insolvency and to identify risk management measures to provide for healthier buildings and reduce premature problems. (Visit www.cmhc-schl.gc.ca/publications/en/rh-pr/tech/01-140-E.htm). This author looked at the failure trends for this study and compared them to the results of the aforementioned 1991 study. Significantly, about 78 per cent of deficiencies were (still) with walls and wall building envelope components, including windows and doors. To protect the financial health of high-rise condominiums, it was recommended property managers know which areas are potentially problematic; this way, they can ensure performance audits are conducted in the first, second, and seventh years. Identifying performance issues before warranty coverage expires reduces replacement costs and avoids the expense of special assessments.
What is the state of building failures in 2012? Anecdotally, according to Tarion, some building envelope problems continue, but it does not seem to be systemic. However, many of the façades on today’s structures are predicted to have a 10- to 15-year service life, which is significantly less than the structure. Durability of the envelope is important—after all, one can change a mechanical component or a countertop relatively easily, but re-skinning an entire building could cost millions per floor or hundreds of thousands per condo unit.
Notwithstanding the financial benefits of investing a little more into the building cost for durability or envelope commissioning to prevent premature failures and expensive rehabilitation, most owners and financial institutions do not specify these requirements. As a result, two-year-old buildings are being re-skinned and envelopes less than 15 years old are being rehabilitated.
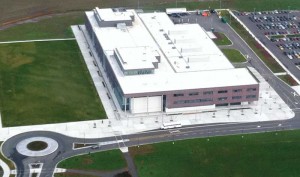
Photos courtesy Firestone Building Products
Durability strategies, as required by OBC and envelope
commissioning processes, must be implemented to prevent premature failures and financial distress. Poorly designed and inefficient building envelopes will be significantly expensive to rehabilitate and the cumulative costs could reach billions of dollars. Rather than wait for special assessments or major capital cost expenditures, it makes sense to require them before construction commences.
Infrastructure Ontario (IO) requires LEED’s Regional Priority (RP) Credit 1, Durable Building, and building commissioning (including the envelope) on all public-private partnership (P3) projects where operators are typically responsible for a 30-year operating period. It is smart from a sustainability perspective to select 30-year roofs and exterior walls for durability, along with daylighting, which has a direct positive impact on productivity. (For a discussion on durability and LEED, see the September 2010 issue of Construction Canada for this author’s article, “Five New Ways to Think Green with Concrete.” Visit www.constructioncanada.net and select “Archives.”) ‘Sexier’ components, like premium finishes, can always be added later.
2. Envelope rating for durability and energy use targets
It makes sense to specify durability categories based on the design service life for the building type. The OBC-referenced CSA S478 specifies residential and office buildings as examples of the ‘long-life’ category, requiring a design service life of 50 to 99 years. While this is great for the structure, an appropriate durability target should also be specified for the envelope. It is not smart to design a 15-year building envelope for something expected to last 60 years, especially for the owners who will have to make costly repeated rehabilitation/replacements four times.
Although building envelopes can be complicated, design professionals can find strength in lessons learned based on experience with LEED’s RP Credit 1.
This author has developed a complimentary Building Envelope Rating (BER) spreadsheet tool, based on more than 50 LEED projects. (For more information on BER, contact sustainableinfo@aol.com). Using various building envelope targets compatible with the CSA standard categories, the tool targets these levels:
- Platinum;
- Gold;
- Silver;
- Throwaway; and
- Temporary.
For example, the Platinum (top-performance) target is to last more than a century, while the Throwaway target is 11 to 24 years—ideally limited to buildings that are only going to be rented for short periods.