Air barrier considerations: Moving toward an impactful, sustainable building envelope
Weighing the contribution of each component
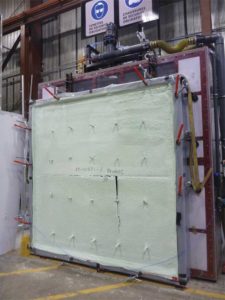
When analyzing air barrier systems, it is essential to not only think about how the system works wholly, but also the effectiveness of every component working in isolation. The validation and performance of these connections and the detailing of air barrier materials need to meet the requirements in the CAN/ULC S742-11 test method referred in NBC. The materials need to perform better than 0.02 l/(s m2) @ 75 Pa according to CAN/ULC S741-08.
Membrane
For example, the membrane itself should be installed around windows, doors, and sheathing joints. Columns or penetrations can be left without membranes if the opening is not greater than 12 mm in width. Air infiltration testing must be conducted and successfully passed with and without transition membranes at the column junction and penetrations. The installation of all types of membranes (self-adhesive, torch, or spray applied) must be done in accordance with the manufacturer’s membrane guidelines. If a primer is required, it must be installed in accordance with guidelines. Usually, all construction details must be exactly designed and installed according to the manufacturing guidelines. If not installed accordingly or it shows blisters or air pockets, corrections need to be done before the spray foam application. In doubt, a site meeting for quality control with the membrane installer and manufacturer should be conducted before the spray foam application.
Accessories
The membrane is accompanied by a few accessories. The most common types being brick ties, Z-bars, and thru-wall flashing that have been tested. Even the brick ties attached directly to the stud should have been tested.
Primer
Any steel deck, galvanized steel or polyvinyl chloride (PVC) must be primed before the foam application.
Sealant and single component spray foam
Single component spray foam and sealant must be used around all windows and doors. Manufacturers and installers will typically validate window installation with sealant and single component spray foam. Something to take note of is if a window connection is done any other way than what the installer and manufacturer recommends for their ABS, co-ordination and validation need to be done with all manufacturers. Windows are a tested component in the ABS but the connection between the components need to be tested as well.
Currently, there is no universal durability protocol applying to all the materials making up a sound ABS. What is available as a minimum requirement in material standard CAN/ULC S741 is an accelerated aging to determine UV degradation and heat aging over a minimum of 21-day period. The pass criteria is a maximum of 10 per cent loss of performance after the conditioning with a maximum leakage rate of 0.02 L/(s m2) @ 75 Pa. The materials need to perform before and after conditioning and are more representative of infield installation.
Considering the installation methods
In addition to stringent product testing, ABS installers should be trained and certified to set up each component in a specific system. Infield installation quality assurance audits should be conducted on building projects to assure the design community and building owners the chosen solution delivers on its promise. Consider a system installer that will work with the group on each phase of the project. Starting with the design phase to final inspection to guide builders, designers, architects, and everyone involved.
Building project leaders should also consider the expertise of a Leadership in Energy and Environmental Design (LEED) green expert who can provide guidance and answer questions about methods and products as it relates to making a better selection of an ABS with the minimum global warming potential (GWP) impact according to the LEED v4 program.
Looking to the future
Even today, the ABS is one of the most neglected factors in the building envelope assembly. If an efficient ABS in not built, then one cannot follow suit with the construction of R-30 walls for that sought-after effect of high R-value. The air exfiltration and infiltration are the second most common building envelope deficiencies justifying major building retrofits.
Lastly, as mentioned previously, the only way to validate the building envelope performance is through commissioning and infield testing. This should be approached as an educational process to all building envelope trades and as a continuity of the actual building code requirements.
François Lalande, an architectural technician, has more than 35 years of experience in the construction industry. Director of business development with Huntsman Buildings Solutions, he offers his expertise in building envelopes, energy efficiency, field quality control and building code compliance. Lalande participates in various research and development projects and is a member of the board of directors of the CEBQ (Quebec Building Envelope Council) in addition to participating on various technical committees including CAN/ULC S700 standards for insulation and polyurethanes.