Advancing energy-efficient timber façades
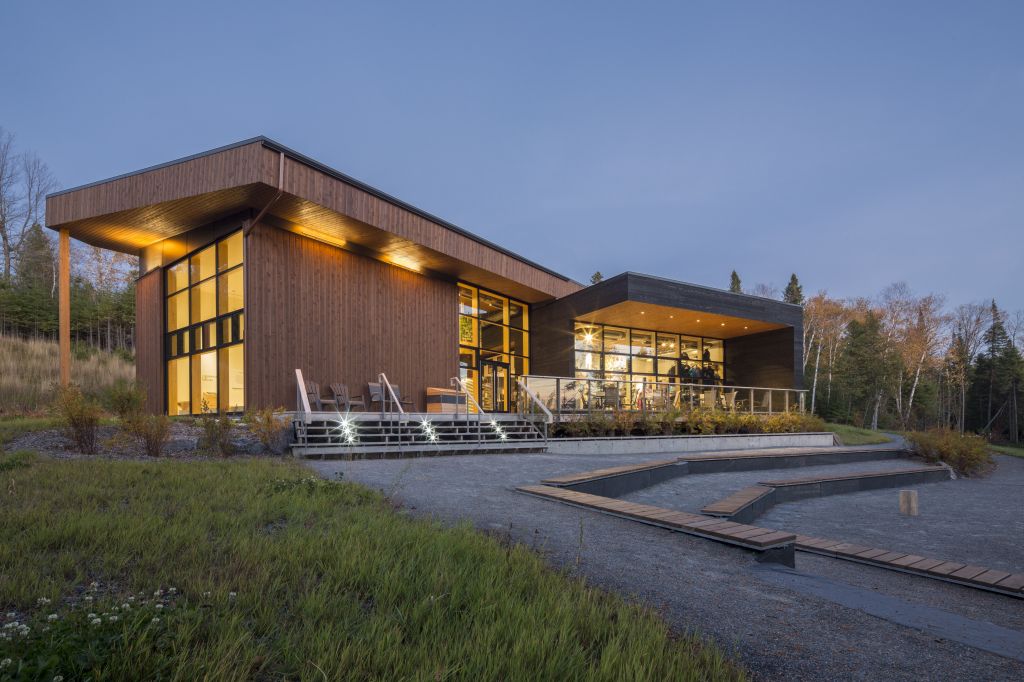
By François Bergeron
The building industry consumes 40 per cent of the world’s energy, and is responsible for more than 38 per cent of greenhouse gas (GHG) emissions, according to studies completed by the World Business Council for Sustainable Development (WBCSD 2009). Since the energy demand and its costs will continue to increase, this explains why Canadian building code requirements are becoming more stringent both nationally and provincially. It also explains why new European programs, like Germany’s PassivHaus,1 are progressively adopted by Canada and the U.S. Green Building Council (CaGBC and USGBC). The latest version of Leadership in Energy and Environmental Design (LEED)—v4—addresses the importance of high-performance building envelopes and glazed façades. It offers automatic achievement of the thermal enclosure system requirements to those buildings achieving PassivHaus certification. Moreover, buildings achieving the energy performance of that standard will earn additional points relating to the annual energy use LEED credit.
This article examines how a façade technology integrating laminated timber and glass increases the thermal effective resistance of glazed façades and building skins. It also provides some potential routes on how the current weakest element of a building envelope can progressively become an energy producer and help facilitate the construction of net-zero buildings, as well as contribute to meet the 2030 Challenge objectives.2
Higher energy-efficient envelopes with timber
Glazed timber façade technology meeting the energy efficiency requirements of PassiveHaus has been available in Canada since at least 2011. For instance, a new library is under construction in Varennes, just south of Montréal—it is expected to be the first net-zero public building in Québec.
In order to achieve this performance level, the architects (Labbé, Laroche, Gagné & Leclerc Consortium) and engineers involved in the schematic and design phase were quick to realize the energy-related objectives could not be obtained with regular North American windows and aluminum curtain wall technology.
Since any net-zero building has to produce as much energy as it consumes daily, it was important for the team to optimize the building envelope’s thermal resistance and to use systems that could reduce the yearly heating and air-conditioning loads. The choice of a German glazed timber façade technology rapidly became a technical prerequisite in reducing the annual heating and cooling loads of this library. A test simulation conducted by independent facility AIR-INS suggests this technology can be 30 to 60 per cent more efficient than other North American curtain wall options.
Figure 1 shows the detailed section of the timber façade that provides a minimal effective thermal resistance of R-8 with triple glazing (reduced to R-4 with double glazing). As illustrated, this assembly has been designed to provide an effective thermal barrier between the building’s outside and inside. Its efficiency resides in the small details of the assembly, which include:
- a continuous ethylene propylene diene monomer (EPDM) gasket that fully covers the aluminum base profile and acts as the first thermal bridge barrier as well as a complete weather seal with the wood;
- a flexible thermal break profile made of effective insulating material stretching between the pressure plate and the top of the EPDM gasket that, along with the insulated glazed (IG) units, acts as the second thermal bridge barrier; and
- a second set of EPDM gaskets on both sides of the pressure plate that mechanically retain the IG unit to the screw channel of the aluminum base profile and act as the third thermal bridge barrier/weather seal.
The mechanical glass-sealing of this technology guarantees stable and long-term performance. Such a system helps minimize both the heating loads during colder periods of the year and the cooling loads during warmer months. This is a significant feature since glass skyscrapers tend to be the main architectural building types in Canadian urban centres—such large-scale reduction in consumption would have a positive impact on lowering energy demand.
In addition to the aforementioned library, residential projects in Québec have used this timber technology. They are currently going under the certification process with the Passive House Building Canada organization.
For projects seeking LEED certification, the timber assembly can provide up to 19 or 21 points in the Energy and Atmosphere (EA) category for the New Construction (NC) and Core and Shell (CS) programs, respectively.
Structural capacity and vast curtain wall surfaces
Curtain walls are typically defined as a form of vertical building enclosure that supports no load other than its own weight, ancillary components, and environmental forces acting on it. A big advantage of the glazed timber assembly is it can act as a structural façade, also supporting the weight of the roof and/or superior stories. This reduces the need of additional bearing structures that would, most of the time, obstruct direct line of sight to the outdoors.
This feature also contributes to keeping the design to its purest form by using an optimized natural and comforting live material like laminated timber to support large glazed units. It maximizes natural light, and outdoor views, as well as provides an appreciable connection/transition between indoor and outdoor spaces. For buildings pursuing LEED, the visible light transmission (VLT) as well as the window-to-floor area ratio remain two important criteria along with the selection of glass that contribute to obtaining points under the Indoor Environmental Quality (EQ) category.
Figure 2 shows a commercial building where the timber façade on the right is structural—that is, it supports the first-floor beams—and the one on the left is not load-bearing. As is easily noticeable, the section of the load-bearing mullions of this building area opened to the public are much larger than the non-load-bearing ones since the fire resistance and the propagation of the flame were the two structural-driving design parameters.
Figures 3 shows two houses where the timber façade mullions were structural. A clear fir glued-laminated timber (glulam) made in British Columbia and a black spruce glulam produced in Québec were respectively used for the fabrication of the timber assembly’s mullions and transoms for this pair of projects.
The left section of the timber façade shown in Figure 3b is structural and incorporates a triple IG unit. This load-bearing section also integrates a large lift-and-slide door in its frame that maximizes the natural light transmittance and eases the accessibility between the outdoor and the indoor.
Pre-unitized and unitized modules fabricated in controlled conditions
To guarantee a high-quality, durable product, all modules for the timber assemblies are delivered pre-unitized on the construction site. The preparation of the shop drawings and the design of all anchors that fix the assembly to the main structure are greatly simplified by the use of advanced 3D modelling and analysis software. The main focus of this design phase is to identify the best strategy to successfully install the timber façade while identifying any potential interference between the different structures and construction systems that could delay its installation.
Once the drawings are approved by the architect, the modules are fabricated in a controlled environment. To minimize the site installation time, all anchors at the top and bottom of the mullions and all membranes along the timber assembly’s outside perimeter are also installed during this fabricating phase. This manufacturing approach contributes to glazing and sealing the building rapidly for subsequent construction indoor-finishing phases.
Figure 4 shows the typical steps needed to install the pre-unitized modules in place. All pre-unitized modules are delivered on a covered trailer so the timber modules are protected during shipping to the job site from snow, rain, and road salt.
The installation time of all timber façade modules (including levelling, gluing of the membrane along the perimeter, and attachment of the anchors) for a team of four glaziers (two seniors, two apprentices) is estimated to be about three to four days per 150 m2 (1615 sf). The next steps are the installation of all IG units with temporary pressure plates, followed by the pressure plates and aluminum covers.
This pre-unitized approach is the most economical way to proceed for curtain wall surfaces of less than 500 m2 (5382 sf), especially when the timber modules can be installed by carpenters who will be followed by glaziers for the installation of IGUs, pressure plates, covers, and cladding around the façade perimeter.
For larger façades, the unitized approach becomes more appealing since these projects tend to be towers of more than five floors with repetitive curtain wall geometry and limited access around the site, as this renders obligatory the use of a large crane to lift and position the modules in place.
This approach depicted in Figure 5 is commonly used for timber façades in Europe. In Canada, the unitized approach for timber façade is under development for some of the large projects (i.e. façade surfaces beyond 1000 m2 [10,765 sf]) when the architectural concept is well-suited for this approach. It is important to mention this unitized method requires a lot of planning with all project professionals (i.e. architects, structural engineers, manufacturer, and contractor) during the early schematic and design phases so the installation phase flows easily.
For this particular approach, the following parameters have to be closely evaluated:
- additional braces required to support the TCW modules when raised to prevent any permanent deformation before installation;
- best handling techniques to guarantee high-quality product once the installation is completed; and
- engineering of the membrane overlaps to obtain a good seal between the modules.
Like aluminum curtain walls, timber assemblies will be as good as the quality of the installation. This is the reason why the construction of highly energy-efficient buildings not only requires a solid integrated design approach at the early design phase, but also the appropriate measures/feedbacks of the real thermal performances once installed (i.e. validation by infrared camera or measure of airtightness).
In Figure 6, the measurement of the temperature on the external covers of the timber façade integrating double-glazed units indicates a temperature of −3 C (26 F) while the outside air temperature is −18 C (0 F). In Figure 7, the temperature on the aluminum covers for a standard aluminum curtain wall is 8.5 C (47 F) while the outside air temperature is −9 C (16 F). Although the outside temperature is two times colder in Figure 6, this outside temperature gradient of 11.5 C (25 F) clearly demonstrates how effective timber assemblies can be compared to regular aluminum systems.
For projects pursuing LEED, the highly energy-efficient timber system can provide in the Innovation in Design (ID) category up to three ‘exemplary performance’ points.3
Net-zero and LEED projects
Besides the energy efficiency provided by the timber façade, wood provides additional benefits to building users. The first important characteristic is the comfort and warmth forest products offer, thanks to their intrinsic properties. On this topic, many studies on the therapeutic power of plants and natural environments have been conducted.4 They show the restorative effect and reduction in stress levels that come about through contact with natural materials like wood, regardless of their varied theoretical backgrounds.
This was understood by architect Tye Farrow, who designed Credit Valley Hospital’s Peel Regional Cancer & Ambulatory Care Centre in Mississauga, Ont.5 More than 10 years after its construction, this project demonstrates a smart way to integrate wood’s beauty and warmth into buildings (Figure 8).
The other important characteristic of timber involves its environmental responsibility. Timber is the only renewable resource amongst the other traditional structural materials for buildings, concrete and steel. Timber has low production/transformation energy requirements and is a net carbon-absorber.
Canada is a large producer of timber products. Further, LEED v4 evaluates building materials more holistically using multiple attributes through approaches such as lifecycle assessment (LCA) and Environmental Product Declarations (EPDs).6 This change could encourage a wider use of the material where traditional curtain walls would be specified.
Another interesting feature of the timber assembly is the design flexibility it provides to the architects for new buildings or existing ones that need to be retrofit. For instance, a potential market for retrofit projects are the schools constructed more than 40 years ago across the country with a façade assembled with a single glass. Just replacing these curtain walls with a double-glazed façade would increase the thermal resistance by a factor of four (by eight when triple glazing is used). This provides an easy solution for all architects and engineers involved in upgrading these public buildings and improving energy efficiency that will contribute significantly at lowering their greenhouse gas (GHG) emissions. Regarding this last point, Figure 9 provides the tonnage of carbon dioxide (CO2) emitted during the fabrication of structural materials largely used in the construction industry.
In addition to the various LEED points already discussed in this article, timber façades could help a project achieve:
- one point for the adhesives and sealant used on the construction site and on the interior of the building in the ID category;
- up to three points in the Regional Priority (RP) category if it could be recognized as having additional regional environmental importance (one example is the Maheu & Maheu commercial building currently undergoing LEED certification);
- one point in the Materials and Resources (MR) category if the glulam is certified by the Forest Stewardship Council (FSC); and
- up to two points in the same MR category if the wood has been extracted, harvested, and recovered within 800 km (500 mi) of the final manufacturing site (or 2400 km [1500 mi] if shipped by boat).
Conclusion
Reducing the CO2 footprint, as well as improving the thermal envelope of new and existing buildings, is a must across Canada. Highly energy-efficient timber façade technology developed in Germany is already available in this country to offer a proven technical, passive, and active measure for improving the building enclosure.
Other emerging innovations—such as solar-power-producing transparent glass combined with the use of high-performance vacuum-insulated spandrel panels—are progressively transforming the weakest skin element of a building into an energy-producer. This definitely reshapes the industry by providing off-the-shelf proven façade systems contributing to minimize all the impacts of the built environment.
The use of engineered structural timber is also contributing to increase occupant comfort—this is especially significant for Canada, where people may spend more than 80 per cent of their time inside. It also allows easing the LEED accreditation of new buildings by providing points for the different categories presented throughout this article.
The specified slider id does not exist.
Notes
1 The term ‘passive house’ (from German Passivhaus) refers to a rigorous design and building standard that focuses on the building envelope and results in cost-effective, low energy homes, with less complex heating and cooling systems. The Passive House standard has grown rapidly since its inception, with now over 40,000 homes worldwide having been built to its specifications. Its design uses these techniques in an aim to achieve an 80 to 90 per cent energy performance savings for each building constructed, and have been applied to many building types including homes, schools, grocery stores, and commercial office buildings. (back to top)
2 Visit www.architecture2030.org. (back to top)
3 This has been validated by the third-party company Vertima, which specializes in guiding the development of LEED tools dedicated to ease the certification and accreditation of buildings. Visit www.vertima.ca. (back to top)
4 See Hartig et al’s “Tracking Restoration in Natural and Urban Field Settings,” which appeared in the Journal of Environmental Psychology (2003, vol. 32). See also S. Kaplan’s “The Restorative Benefits of Nature: Toward an Integrative Framework,” which appeared in that publication’s 1995 edition (vol. 32). (back to top)
5 For more, see the article, “Healthcare in the Mist: Innovation Allows Wood Architecture at Credit Valley Hospital” by Sean Stanwick in the September 2006 issue of Construction Canada. (back to top)
6 For more on LCAs and EPDs, see two articles—“Transparency in the Built Environment: Calculating and Assessing Embodied Energy of Construction Materials” by Francesca Desmarais, Marion Lawson, LEED AP, and Thaddeus Owen, LEED AP and “Carbon, Environmental Product Declarations, and Brickwork – Reducing footprints through masonry” by Maranda Bennett—that appeared in the October 2013 issue of Construction Canada. (back to top)
François Bergeron is the president of IC2 Technologies. A mechanical engineer with a master’s in science, he worked more than 20 years in the aerospace and automotive industries. As the founder of IC2, Bergeron transfers his integrated design approach expertise to the development of advanced product in the construction of more energy efficient timber façades. He is a member of the Québec Order of Engineers as well as Passive Buildings Canada. He can be reached at fbergeron@ic2tech.com.