Advancing bridge performance with UHPC
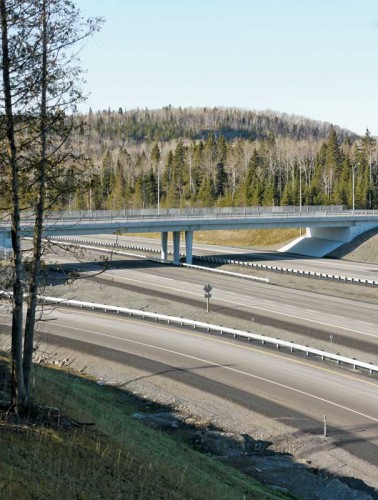
By Raymond Krisciunas, P.Eng., Peter J. Seibert, M.Sc., MBA, P.Eng., and Philip D. Murray, M.Eng., P.Eng.
Over the past several years, ultra-high-performance concrete (UHPC) field-cast joint connections have become a common bridge solution in Ontario and gained acceptance in various states, such as New York, Iowa, Montana, and Oregon. However, the Ministry of Transportation Ontario (MTO) recently enabled this material to be used in new ways, relying on its combination of superior properties—including improved strength, durability, and bond development—to overcome significant bridge design obstacles. (For past Construction Canada articles on UHPC, see “Whitemans Creek Bridge” by Vic H. Perry, Wade F. Young, and Brent I. Archibald (July 2012), “An Ultra-high-performance Upgrade” by Gaston Doiron and Kelly A. Henry (December 2011), “Precast Solution for Performance Cladding: Ultra-high-performance Concrete for B.C. Building” by Don Zakariasen and Peter Seibert [September 2010], and “Restoring the Rialto: Specialized Precast Cladding Revitalizes an Old Hotel,” by Perry and Lisa M. Birnie [Sept. 2009]. Visit www.constructioncanada.net and select “Archives.”)
Currently, MTO is embarking on an aggressive four-laning project in Northwestern Ontario that involves construction of about 30 km (19 mi) of highway and up to 30 structures in an area with extremely rugged terrain, ranging from deep swamps to massive rock cuts.
As part of this project, a new ‘parclo’ (partial cloverleaf) interchange was required at the intersection of Highway 11/17 and Hodder Avenue in Thunder Bay. The structure, founded on a combination of hard till and bedrock, spans over a total of six lanes. (The authors would like to thank the Hodder Avenue Underpass project team, which includes the Ministry of Transportation Ontario and Hatch Mott MacDonald, for their collaborative partnership throughout the design and construction of this project).
The need for a striking design
Since the interchange is the first structure drivers encounter when approaching the city of Thunder Bay, it was desirable to elevate the appearance from the somewhat utilitarian style frequently encountered in urban highway settings to a clean, slender, and open design. Given the location and exposure, it was also desirable to use precast elements throughout. Consequently, a two-span concrete box girder configuration was the most practical and cost-effective solution—however, these structures are typically rather bland and can appear bulky.
To counter this challenge, a design concept was developed whereby the pier cap beam could be incorporated into the superstructure, appearing to be integral with the box girders while providing a frame that seems to go directly into the superstructure. This appearance is achievable with the use of conventional post-tensioned cast-in-place superstructures, but extremely difficult to achieve using pre-fabricated elements.
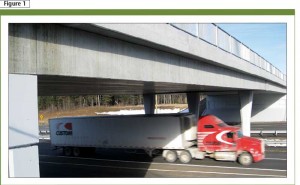
Other challenges included a relatively shallow superstructure in which to incorporate the main pier cap/cross beam and analytical complexity of two-way behaviour by virtue of the continuous box girders intersecting the transverse cross beam. In the final configuration, the pier cap/cross beam had to become integral with the box girders in the longitudinal direction and provide a continuous span between the piers and cantilever over the ends (Figure 1).
The initial design, using 60-MPa (8700-psi) concrete, necessitated no fewer than four pier columns to support the superstructure. Visualizations using this configuration demonstrated the structure still appeared bulky because the superstructure and pier cap depths could not be increased without dramatically affecting the rest of the bridge. An alternative was required.