Advancing bridge performance with UHPC
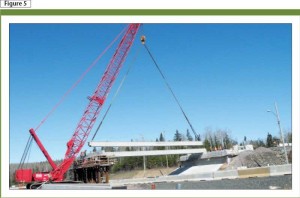
Photo courtesy Hatch Mott MacDonald
Field-cast UHPC connections
The ‘topless’ box girder superstructure has become fairly common in Northwestern Ontario. In this design, precast concrete box girders (Figure 5) are joined together using UHPC field-cast joints acting in pure shear. No topping slab is placed over top of the structure and asphalt is placed directly on the box girders. This is made possible through a combination of high performance materials such as glass-fibre-reinforced polymer (GFRP) reinforcing and UHPC field-cast joints, in combination with carefully designed details, to result in extremely durable connections between the elements (Figure 6).
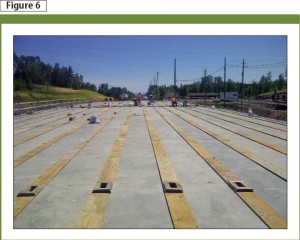
This Thunder Bay bridge is one of the best UHPC applications whereby precast elements, such as box girders or deck panels, are connected using a field-cast UHPC solution. Historically, precast elements are preferred for bridges due to their design efficiency, fast installation, and low initial costs. However, the standard grouting material in the joints is often the first part of the bridge to fail due to continuous highway impacts that cause the joints to leak.
The use of transverse post-tensioning (P/T) or a concrete topping slab across the joints ensures adequate shear transfer between girders, such that the deck effectively remains structurally monolithic under the constant pounding of truck wheel loads and seasonal conditions. While these construction techniques can resolve the majority of the performance issues, they are not without potential problems. For example, they:
• are expensive;
• add manufacturing complexity for the precaster;
• do not allow for installation flexibility in the field;
• have potential for corrosion; and
• can be challenging for bridges with varying cross-fall.
Further, the analysis is usually complex when determining the correct post-tensioning forces and corresponding creep losses. Potential long-term corrosion of the strands could also affect the durability of the structure.
In lieu of the concrete topping slab or transverse post-tensioning, UHPC is increasingly specified in North American bridge projects for cast-in-field connections between precast elements such as:
• box-girders;
• bulb-tee girders;
• reinforced bridge deck panels;
• curb connections;
• negative moment connections over piers; and
• bridge expansion joints.
Employing UHPC technology and eliminating P/T for precast elements enable the designers to simplify the precast panel fabrication and installation processes. This simplified design provides the owner with improved tolerances, reduced risk, increased speed of construction, overall construction cost savings, and a more durable, longer-lasting bridge deck solution.
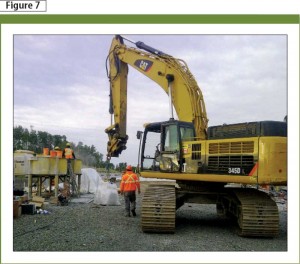
When field-casting UHPC, materials are either batched in dual onsite mixers or ready-mix concrete trucks. For the Thunder Bay project, all premix materials were shipped in 1116-kg (2460-lb) sacks and mixed in two 0.5-m3 (0.65-cy) high-shear onsite mixers (Figure 7). UHPC requires significant energy to mix and to lubricate all its raw material constituents (i.e. cement, silica sand, ground quartz, and silica fume) within the powder matrix. Higher energy completes the mixing process more quickly, resulting in a self-levelling UHPC.
After batching, the fluid UHPC was placed into all the joints using buggies and chutes. To control hydrostatic pressures throughout all connections, the joints were isolated to ensure complete filling. When placing the self-levelling UHPC material into joints, it is important to take advantage of its fluid characteristics. When discharged from the concrete bucket into the joints, UHPC spreads itself throughout (Figure 8).
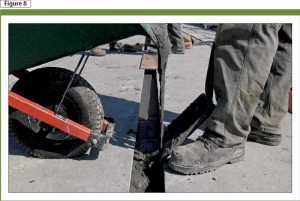
Moving the discharge point so it always stays behind the ‘leading edge’ of the flow, the joint can be filled in one continuous motion. Due to its self-levelling characteristics, UHPC was placed at the lowest end of the joint using a top form to contain the concrete and moving toward the high end of the joint where a ‘chimney’ was placed. (This chimney ensures proper hydrostatic pressure within the joint and prevents any low spots.)
To avoid any dehydration of the UHPC, all joints were immediately covered with resin-coated plywood (top form). After the initial hardened strength of the UHPC was reached, the joints could be ground flush to the precast elements if necessary.
To ensure proper quality of all field-cast UHPC material, the flow characteristics of each batch were tested using a modified version of ASTM C1437, Standard Test Method for Flow of Hydraulic Cement Mortar. This was completed immediately after mixing to ensure the consistency within all batches. Compressive strengths were also validated daily.