Advancing bridge performance with UHPC
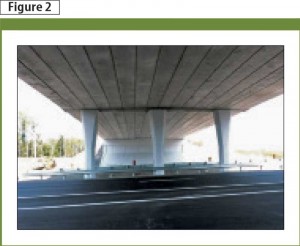
Finding success
The main pier cap was then re-designed using prestressed UHPC with a compressive strength of up to 200 MPa (29,000 psi)—this resulted in one less pier column (three, in total) and a more open appearance (Figure 2). This was the first time precast UHPC was used in this type of application in North America. The pier cap was actually an inverted T-shape that provided ledges on which the box girders could sit. It spanned continuously over the three pier columns, and was also cantilevered at the ends. For this reason, considerable prestressing was required in the member’s top and bottom.
Due to the amount of prestressed strand and other perforations and embedments, the precaster used building information modelling (BIM) to identify conflicts between the beam and box girders. It was then determined once the T-beam was released, it would significantly deflect under the prestress effects and would not sit flush on the seats at the tops of pier columns. This problem was overcome by simply anchoring and jacking to straighten the member and then filling gaps with high-performance epoxy grout.
Casting the UHPC T-section was relatively simple, using a steel form in the exact shape of the T-beam section as it was installed in the field. The UHPC material was placed from the top of the stem and gradually flowed to the top of the T-section (Figure 3). No vibration was applied.
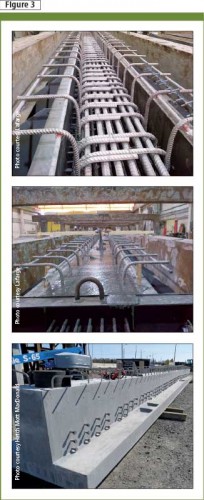
Middle: The T-beam steel form has been filled with UHPC.
Bottom: T-beam prior to installation.
UHPC was also used to produce the shell pier columns—members that would be exposed to winter de-icing salt spray, which has been known to cause considerable damage to similar reinforced concrete elements on other structures. Since UHPC is extremely low in porosity and essentially immune to water penetration, it was believed its incorporation into the pier columns would result in far more durable elements. A customized UHPC shell was then designed to act as a non-structural form which could be filled with reinforced concrete. In addition to durability, the UHPC shell pier columns were shaped with flared tops for esthetic appeal (Figure 4).
In 2010, a similar application at another Northwestern Ontario structure over the Wabigoon River near Vermilion Bay (shown on this magazine’s cover), was highly successful. For this bridge structure, the much shorter and circular UHPC shell pier column was rather simple.
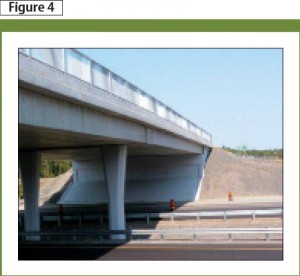
Photo courtesy MTO
UHPC pier column shells
The 8.35 m (27 ft, 4¾ in.) height and complex shape of the precast UHPC pier column shells proved to be challenging. The columns were cast on an angle, using an inner and outer steel formwork. The inner steel mould was self-collapsing to allow for initial shrinkage of the UHPC while the precast element was hardening. The transition of the octagon shape (from the constant cross-section to the flared cross-section) created challenges for:
• form manufacturing;
• casting of the UHPC;
• initial shrinkage allowances; and
• stripping of the UHPC precast element.
Due to the column’s height, the form was positioned on an approximate 15-degree angle; the material was placed slowly from the top of the column through an inlet funnel. When casting a long, thin and slender UHPC element, the pouring process has to be carefully monitored to ensure proper fibre dispersion throughout the plastic concrete.
Preferential fibre orientations occur due to the plastic material’s flow characteristics, which can be used as an advantage in areas where tensile forces in the finished precast element are expected. When UHPC is placed too fluid, the steel fibres of the plastic material can settle out, resulting in a potential weak plane in the hardened and finished precast element. Therefore, proper flow characteristics and placement methods of the UHPC must be carefully developed and controlled during the manufacturing process. (For more, see “Equipment and Production Techniques with UHPC,” by Vic H. Perry and Peter J. Seibert, in the April 2011 issue of CPi Magazine, published by Concrete Plants International).
The local geometry of the UHPC shell pier column form meant several casting challenges for the precaster. The tight radius corners at the intersection of the octagonal planes created local flow resistance and subsequent irregular fibre dispersion. (When casting thin, tall, slender, and complex precast elements, a prototype cast should be first completed to validate the form design and casting techniques). As mentioned, the height of the form made it necessary to cast the element at an angle because of height clearance within the precast plant. This created additional fibre dispersion issues at the flow planes where the UHPC met from opposite sides of the form, adjacent to the fill inlet funnel.
Since the shell pier form was intended as a non-structural element, minor fibre irregularities would not be a problem; however, if the internal form release is not completed at the proper time during the setting, the UHPC may crack during early setting, due to restrained shrinkage, low early strength, and irregular fibre dispersion.
To erect the UHPC shell pier columns, the original forms were shipped to the site. These were wrapped around the elements before concrete infill placement. A robust steel support structure was necessary to support the UHPC shell pier columns and T-beam until the concrete box girders had been placed and the entire superstructure was made composite with the pier cap.