Addressing insulation challenges in cold regions
Residential
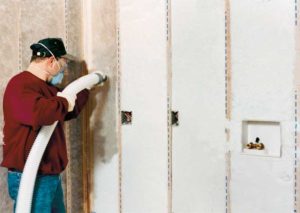
Home is where people spend the majority of their time and want to feel most comfortable, so it is important residential insulation systems successfully address airtightness, thermal performance, and moisture management.
Airtightness is a commonly overlooked aspect of heat transfer and can become a greater challenge as buildings age. For new homes, spray foam insulation that expands to fill potential air gaps can be a suitable solution for open spaces like attics, and can help create a more energy-efficient living environment. In many cases, more of the cost-efficient solutions chosen incorporate a combination of different types of components, such as housewraps (for large exterior areas), tapes (for sealing seams and protecting window and door leaks), caulks, and sealants. Entry and exit points of pipes and wires are potential areas of heat loss. Using caulk and sealants on the outside (and inside) of the home and spot treating with spray foam around plumbing and electrical penetrations can address porous areas where heat can escape. Even simple solutions like including gasket covers on all outlets and light switches can make a big difference in preventing the outflow of heated air. The baseboards where walls and floors meet tend to be drafty, so special care must be taken to ensure those junctions are properly caulked and sealed.
While less common in modern residential buildings, crawl spaces are still used by builders for convenience and upfront cost savings. Levelling a sloping lot for a concrete pad can be expensive, and a crawl space eliminates that need. It can also be a convenient place to route HVAC, water, and sewer connections. Crawl space insulation is not a big deal in hot climates. However, in colder regions, uninsulated crawl spaces can be money pits where heated air could exfiltrate the building. Despite the inefficiency, there are many homes in the United States and Canada with dirt-floored, vented crawl spaces. Insulating crawl spaces ensure a tighter building envelope, and places significantly less stress on heating systems. Additionally, fibreglass batts between floor joists (where pipe and wire conduits are located) help prevent heat loss between the floor and anything below it.
Properly insulating homes is all about finding balance. As insulation materials have improved in quality, moisture and mould prevention has become an increasingly important issue—the more energy efficient and airtight a home is, the less efficient it is at being able to dry out when moisture gets in. As builders have pushed for tighter building envelopes and lower Home Energy Rating System (HERS) scores, manufacturers have responded by developing thicker and more effective insulating materials. These additional insulating layers and new materials, however, have not managed to keep moisture from rain and vapour out of walls. Over time, trapped water can damage wall assemblies, create mould, and degrade critical framing assemblies. Employing continuous exterior insulation with interior cavity fibrous batt insulations in combination with a smart vapour retarder—one that ‘breathes,’ becoming more porous as humidity increases—allows trapped wall moisture to dissipate into the conditioned air space.
Commercial
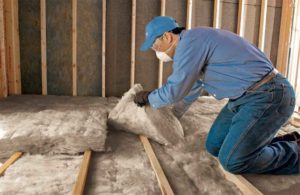
Due to an especially cold 2017 winter season, Canada’s GHG emissions actually went up that year—far short of its reduction targets under the Paris climate agreement. As Canada takes steps to become more energy efficient and eco-conscious, developers must pay close attention to commercial building designs that burden power grids and contribute to air pollution via energy generation. Using insulation products made with plant-based/organic binders (as opposed to formaldehyde and harsh acrylics and dyes) and containing high-levels of recycled content supports green construction, and helps buildings achieve Leadership in Energy and Environmental Design (LEED) certification and other sustainability credits.
Commercial buildings—typically built from concrete and metal—are rife with thermal bridging. Both concrete and metal offer poor heat flow resistance between exterior walls and the outside. Metal stud framing, common in commercial construction, is a major source of heat loss due to the material’s conductivity. Incorporating appropriate amounts of thermal insulation into the wall assembly is a good first step toward an effective thermal control strategy. Commercial thermal insulation options include cavity insulation, which occupies space inside the wall cavity, and insulating sheathing, which is installed over the exterior walls.
A steel stud cavity wall with a masonry façade is the most common type of wall assembly for commercial buildings. In cold climates, designers can improve thermal performance and control cavity condensation by:
- specifying exterior insulating sheathings in order to increase cavity surface temperatures and improve energy efficiency;
- incorporating exterior wind/air barriers to reduce air leakage; or
- specifying a smart vapour retarder to reduce convective loops and improve drying capability.
These are cost-effective ways to achieve thermal performance while managing moisture and reducing the saturation of substrate materials.
Insulating sheathings can be installed inside or outside of concrete block and tilt-up walls. A common insulating material for this construction is foam plastic insulation board. The location of the sheathing varies based on climate and material type. Interior non-loadbearing steel-framed assemblies can support cavity insulation. Fibreglass batt insulation inside the cavity increases the thermal efficiency of commercial buildings. It is moisture resistant and eliminates heat loss when combined with structural insulated panels. Since thick concrete has insulating value, some building codes have reduced insulation requirements. However, it is advised to exceed code requirements to achieve the highest level of energy efficiency.
Exterior insulation systems typically resemble traditional stucco and create a thermal break between exterior walls and the surrounding environment. If an exterior finish does not accommodate insulation, a continuous insulation (ci) board inside of the wall assembly is a good option.
ASTM C518, Standard Test Method for Steady-State Thermal Transmission Properties by Means of the Heat Flow Meter Apparatus, is used to measure the thermal properties of building materials. A heat flow apparatus measures heat transfer through homogeneous materials such as insulation. The performance of those materials is rated according to thermal conductivity (K), thermal conductance (C), and thermal resistance (R-value). Every region of Canada mandates a different mix of techniques and insulation requirements based on the annual rainfall, moisture, elevation, etc. For that reason, the Canadian Wood Council (CWC) sponsors a building product calculator, which displays the latest thermal-resistance code requirements in a selected climate zone and suggests the most appropriate materials.