Active Thoughts on Passive Design: Designing with wood for next-level green projects
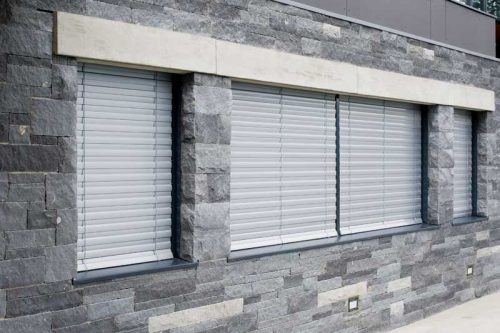
Photo © David McColm Photography
Wood assemblies in the project
The use of wood was pivotal in enabling this project to achieve the PH efficiency requirements with an envelope system that was healthy, sustainable, comfortable, and architecturally pleasing. The envelope for the residence was constructed using a high-performance, prefabricated panel package. The main structural wall consists of standard stud 2×10 framing (406-mm [16-in.] engineered I-joist for floor and roof) sandwiched between oriented strandboard (OSB) and a wood fibre diffusion board.
OSB was used for the interior sheathing; it provided structure, shear, and both an air barrier and vapour retarder. All panel connections and penetrations to the OSB were taped and sealed with high-performance building tapes, providing a continuous, robust air barrier—this feature is critical in reaching the required airtightness thresholds. The pre-drywall blower door test achieved 0.33 ach at 50 Pa.
OSB is also classified as a Class II Vapour Retarder that works in conjunction with the exterior wood fibre diffusion board to ventilate excess vapour in the system to the exterior. In addition to reducing thermal bridging, the exterior wood fibre diffusion board provides protection from the elements while permitting drying to the exterior. A combination of blown cellulose, recycled paper products, and stone wool batts were used for insulation. An interior service wall, constructed of 2×4 lumber, provides further insulation and a cavity to run services, limiting penetrations to the air barrier. Effective R-value is 44 for the walls and 69 for the roof and floor.
The use of prefabrication further contributed to the environmental performance of the home. Through the shop drawing, ordering, and manufacturing process, the team was able to optimize the use of building materials, reducing construction waste to less than three per cent. Additionally, the prefabrication process is performed in a controlled indoor environment, increasing efficiency, quality control, and precision while reducing the occurrence of changes (e.g. swelling, mould growth, warping) in the material from exposure to weather.
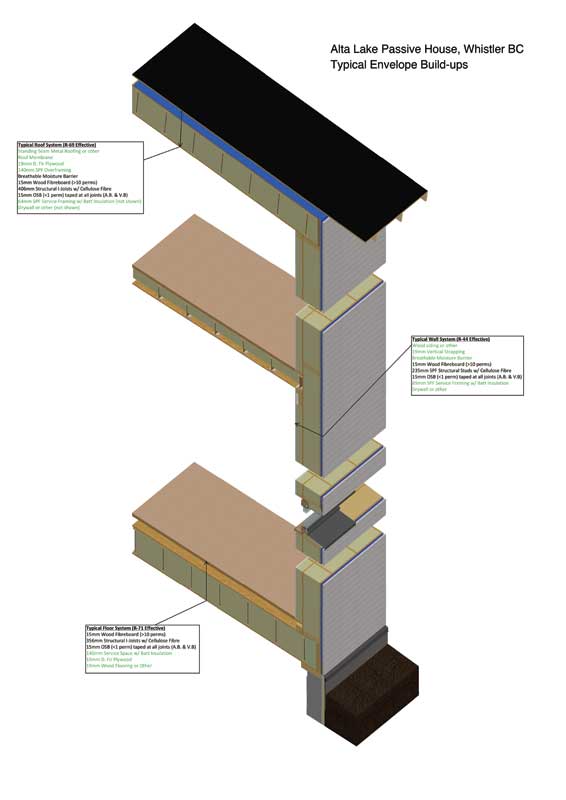
Image courtesy BC Passive House
Prefabrication was crucial in overcoming the challenges, increased costs, and time considerations faced due to the site conditions. Framing for the project took place offsite, in a controlled environment at the same time the foundation and site works were underway. Prefabrication offered efficiency, quality control (QC), and precision that would have been difficult to achieve with onsite construction. Once onsite, the panels were installed and the project was out of the weather within five days, dramatically reducing the onsite construction time and ensuring the materials were protected from weather damage.
The use of wood in the prefabrication enabled the design and fabrication team to be scrupulously accurate, enhancing the precision of assembly and the resulting airtightness requirements. This level of accuracy is often difficult to achieve with either onsite construction or other materials, prefabricated or site-built.
In addition to energy efficiency, the clients were focused on material choices. Through use of wood and other ecologically responsible materials, significant environmental and architectural value was achieved for a modest premium compared to conventional construction. Products were chosen for their lifecycle environmental impact, with the project team opting for materials that were sustainable, natural, and de-constructible at the end of their lifecycles.
The main building component of the facility is wood or wood byproducts. Utilizing a wood first approach for the structure of the building avoided approximately 206 metric tonnes of carbon dioxide (CO2) emissions. (This was calculated using the web tool at cc.woodworks.org/calculator.php). This does not include any operational savings of carbon emissions.
Interior design for prefabrication projects requires preplanning and an understanding of the interior volume of the space. It is difficult to adjust window heights or reposition an opening once the panels have been manufactured so previsualization tools, including the 3D models, were used in the design of the project. A collaborative approach on the window package to determine the position, opening placement, and finishes was required in the design phase to ensure correct placement to achieve the views and maintain privacy and performance goals.
Hiding mechanical corridors when roofs and floors did not have exposed floor joist cavities set up challenges that in the end created beautiful solutions. Dropped ceilings were constructed on the main floor to conceal the mini-split system. The exterior wall containing the fireplace was protruded out to accommodate a mechanical cavity, which in turn influenced the jugular angled marble block of the fireplace. The bulkheads in the family room were contained by a wood ceiling detail.
A staircase ‘tower’ was introduced early on in order to create a stack effect, allowing excess warm air to be expelled from this building. This plays an important role in maintaining a comfortable interior temperature. The feature was played up with a floating staircase and a decorative pendant installed into a complementing wood ceiling detail.
Passive buildings can be constructed with virtually any structural material. However, the use of wood fulfilled many of the owner’s and design team’s aspirations for high performance design—energy performance, comfort, quality of construction, accuracy, and low environmental footprint compared with alternative materials.