Active Thoughts on Passive Design: Designing with wood for next-level green projects
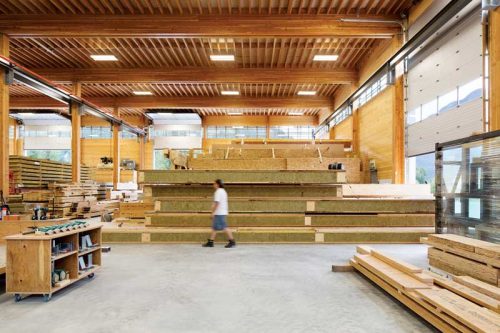
Photo © Ema Peter Photography
Designing with wood
A passive design building can be built using any of the major structural materials—wood, steel, or concrete. Most smaller buildings, however, tend to use wood products if the prevailing code permits. There are many reasons for this.
Since energy efficiency is a driving concern, great efforts are made to reduce the impact of heat loss through thermal bridges. Wood transfers thermal energy at a much lower rate than either steel or concrete. This in turn reduces the amount of time, labour, and materials required to offset thermal transfer associated with other materials.
As a material, wood can also be machined to extremely tight tolerances. Since many PH buildings are fabricated in panels, components, or volumetric units, precision assembly is important to avoid any air leaks—and the energy and moisture therein. Further, wood has a low mass when compared with other structural materials. Reducing the mass of transport for prefabricated elements has both environmental and cost savings. Other sustainability-related implications include the fact wood is renewable, sequesters carbon, and has a lower embodied energy than other traditional structural materials.
PH in Europe… and Canada
Energy performance is increasingly being incorporated into building codes around the world. More than 50 jurisdictions in Europe either require or reward buildings built to a ‘passive’ level. The metrics for certification of a PH building are the same globally, with projects certified in severe cold and hot/humid climates. (For an international database of PH projects, visit www.passivhausprojekte.de/index.php?lang=en). However, in the United States, there has been vigorous debate on the merits of having adaptable standards to reflect different climate regions. This would result in variable performance levels depending on location.
In Vorarlberg, Austria, PH design is a requirement for all social and affordable housing projects. The rationale is the occupants of these buildings are least able to afford the high energy costs associated with imported natural gas and fossil-generated electricity. Social and environmental aspirations mesh seamlessly with economic considerations.
In 2008, the European Union passed a resolution calling on each European member state to adopt the Passive House Standard by 2016 for all new construction and major renovation projects. Ultimately, this resolution will alter the construction industry in all parts of Europe, as the continent recognizes the need to build for long-term economic benefits, improved indoor air quality (IAQ), and personal and national energy security.
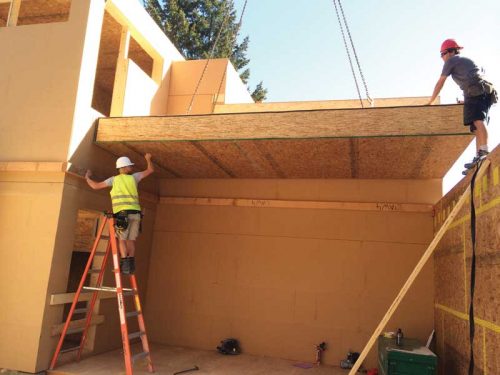
Photo © Karel Jonker
Uber-high-energy-performance building culture may well have been refined in Europe over the past 20 years, but it has firm roots in Canada. Now, it appears those roots are bearing fruit with a number of projects being certified across the country. (To see a listing on CanPHI projects, visit canphi.ca/our-resources/projects). Passive House is gaining ground in Canada as an ambitious, but practical, approach to energy efficiency. However, the concept is not just about energy. Many people invest in PH buildings because of what its occupants experience—comfort and quality of living.
BC Passive House has established a fabrication plant to build passive and high-performance buildings; there are other prefabrication companies building components to the PH standard across North America, with more expected. A recently completed project, Alta Lake Passive House in Whistler, demonstrates the level to which pre-fabrication, exemplary design, and high performance can mesh into one amazing structure.
Case study: Alta Lake Passive House
The objective of the design for this lakeside home was to create a modern, high-end interpretation of ‘green housing.’ (In addition to BC Passive House, the project team included Murdoch and Company Architecture and Planning, Mountain Resort Engineering, Dürfeld Constructors, and Arbutus Interiors). Focusing foremost on energy reduction, the clients mandated the project must embody the PH Standard with the caveat there would not be a compromise on the esthetics of the design. The use of wood was a natural choice for the design team to fulfil these requirements and meet all of the expectations for the home.
Preliminary discussions focused on typical planning and programming within the home, given some very difficult site constraints. The topography and compact nature of the site posed significant challenges. The waterfront site slopes sharply down to the east with panoramic views over the lake to the mountains across the valley. Fortunately, the desired placement of windows complemented the need to optimize passive solar gains and losses.
Windows are a significant contributor to the overall performance of a building. In the case of the Alta Lake residence, the windows were also the focal point of the design strategy to ensure the surrounding views were captured and highlighted. The residence was fitted with aluminum-clad, PH-rated wood windows.
Shading from a neighbouring home and its stand of coniferous trees interfered with solar gains on the lower levels of the south orientation. The massing of the home, therefore, was stepped and jogged on the upper floor to optimize the glazing and views without sacrificing privacy. Exterior window blinds and overhangs were used to prevent overheating in the shoulder and summer months.
Analysis of the residence using design modelling software—called the Passive House Planning Package (PHPP)—forecasts that by constructing the residence to the PH standard, the clients will save approximately 50,000 kWH/year on energy required for heating and cooling compared to an equivalent residence built to code. (PHPP is based on an MS Excel workbook that accurately describes the thermal building characteristics and performance. It can be combined with the 3D tool, designPH—a plugin for SketchUP). This represents an 80 to 90 per cent reduction in energy required for heating and cooling. The reductions are achieved through efficient design, the use of passive heating and cooling techniques; an optimized, super-insulated airtight building envelope that is fitted with high-performance windows, and a heat-recovery ventilation system.