Achieving continuous advantages with EIFS insulation
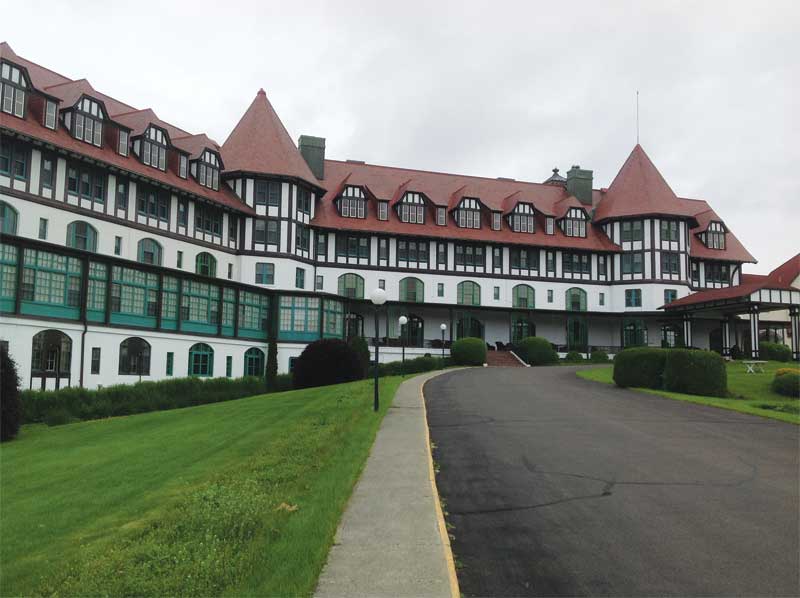
By Andreas Lueth
Continuous insulation (ci) has been a part of some Canadian code requirements since 2011, but the concept can still be confusing for design and construction professionals. In American Society of Heating, Refrigerating and Air-conditioning Engineers (ASHRAE) 90.1-2013, Energy Standard for Buildings Except Low-rise Residential Buildings, ci is defined as being “uncompressed and continuous across all structural members without thermal bridges other than fasteners and service openings.” (This article has been adapted from an earlier piece bylined by Brian Chang, which appeared in the June 2017 issue of The Construction Specifier, the official publication of CSI. Visit www.constructionspecifier.com.)
The insulation can be installed on the enclosure’s exterior or interior, or be integral to opaque envelope materials. Wherever it is located, the ci layer must span across or through thermally conductive elements such as steel columns, metal studs, and concrete masonry units (CMUs). Otherwise, thermal bridging through high-conductivity structural components can result in reduced insulation performance by up to 40 to 60 per cent in metal-framed buildings, and up to 20 per cent in wood-framed enclosures, according to studies by the U.S. Oak Ridge National Laboratories (ORNL). (For more, see “A Review of High R-value Wood-framed and Composite Wood Wall Technologies Using Advanced Insulation Techniques,” by Jan Kosny, Andi Asiz, Ian Smith, Som Shrestha, and Ali Fallahi. It appeared in Energy and Buildings [72], published in 2014 by Elsevier.)
Thermal bridges have other detrimental effects, including condensation and moisture accumulation in the enclosure, as well as occupant discomfort in localized interior spaces. Traditional non-continuous insulation—for decades, simple layers located neatly between steel columns or light-gauge studs—is insufficient in this regard. An exterior insulation and finish system (EIFS), which offers ci by design, offers an effective alternative.
Codes and certifications
Specifying ci can be essential to meeting key energy codes, as well as achieving certification under Passive House, Leadership in Energy and Environmental Design (LEED), or various net-zero-energy or reduced carbon footprint and greenhouse gas (GHG) programs. (Continuous insulation [ci] is found in National Energy Code of Canada for Buildings [NECB] Part 3–Building Envelope and the National Building Code of Canada’s [NBC’s] Article 9.36.2.5, “Continuity of Insulation.” ASHRAE 90.1-2013 is not referenced in NBC, but is applicable in Supplementary Bulletin 10 [SB–10] of the Ontario Building Code [OBC], British Columbia’s Building Code, and the City of Vancouver’s Building Bylaw.)
Some of these benchmarks offer prescriptive solutions. Using the project’s climate zone, the space’s conditioning category, and maximum allowable U-factor (i.e. rate of heat loss), ASHRAE 90.1 offers guidance on applying ci to achieve required performance levels. Using an example from Supplementary Bulletin 10 (SB-10) of the Ontario Building Code (OBC), a nonresidential building in Climate Zone 5 would see a minimum of R-12 ci, in combination with R-13 batt-type insulation in above-grade steel-framed walls.
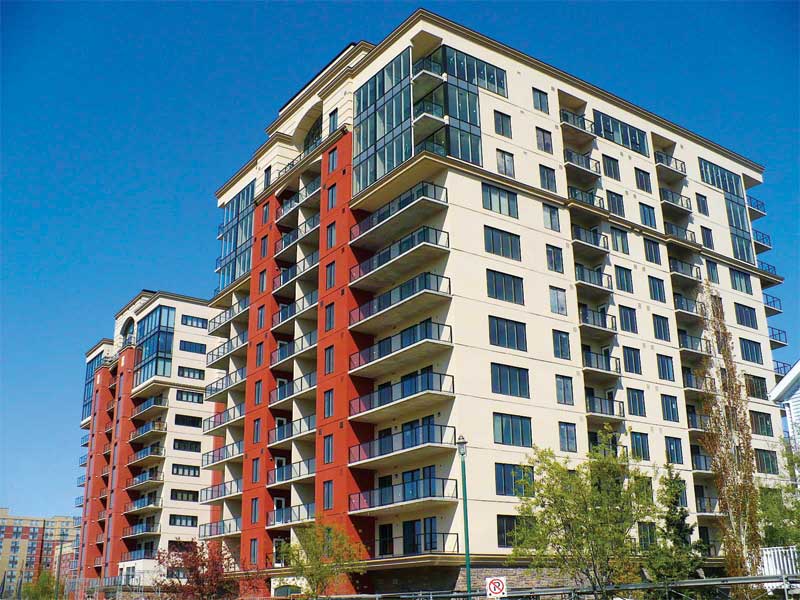
Occupant safety requirements affect use of ci. Most relevant for Canadian building teams are those dealing with the use of combustible components in exterior walls and the protection of combustible insulation. This subject area is deserving of its own article, but suffice it to say here, if use of the proposed wall assembly is not described in the code’s provisions (i.e. as it relates to combustible or noncombustible construction allowances), the design team should seek conformity assurance through the successful completion of code-referenced fire assessment standards. (Within the code there are a number of referenced standards allowing for the use of combustible components in a building, or a part of building required to be of noncombustible construction. Proponents undergoing fire assessment usually, though not always, conduct the testing under a certification program through Underwriters Laboratories of Canada [ULC], Intertek, or Quality Assurance International [QAI]. These certification bodies then publish directories listing the subject materials and/or assemblies. Design or certification listings serve as conformity assurance the given material meets the code-referenced standard and related pass/fail criteria.) For example, protection from adjacent space—as described in OBC Article 3.1.5.12, “Combustible Insulation and its Protection”—lists a number of thermal barriers that may be employed for the protection of combustible insulation. If the assembly does not include one of the code’s acceptable material solutions, a product shown to meet the code’s thermal barrier requirements through Underwriters Laboratories of Canada (CAN/ULC) S101, Fire Endurance Tests of Building Construction and Materials, may be used. From an exterior protection standpoint, wall assemblies containing any combustible components such as combustible exterior insulation may require testing under CAN/ULC S134, Fire Test of Exterior Wall Assemblies, as per National Building Code of Canada (NBC) Article 3.1.5.5, “Combustible Components for Exterior Walls.” A proactive policy of ensuring the proposed wall assembly meets any and all applicable code criteria, above and beyond those relating to energy efficiency, is best.
With the rise in use of ci and air barriers, National Fire Protection Association (NFPA) 285, Standard Fire Test Method for Evaluation of Fire Propagation Characteristics of Exterior Non-loadbearing Wall Assemblies Containing Combustible Components, has become a vital and ubiquitous requirement for building projects. Specifiers often check to ensure their proposed assemblies have already been subjected to the costly test, in which an impressive full-scale multistorey mockup is subjected to a fire intended to simulate a blaze originating from an interior room. In the 2015 International Building Code (IBC), six sections (including 1403.5 for weather-resistive barriers [WRBs] and 2603.5.5 for foam plastic insulation) reference NFPA 285.
In general, project teams must focus on NFPA 285 early in the design phase as the market may not offer enough compliant assemblies for walls of greater than 12 m (40 ft) above grade. Additionally, some rainscreens and other cladding types have yet to be tested with foam plastic insulations. In these cases, the design team can choose to employ a tested combination of products or have the proposed assembly tested.