Achieving continuous advantages with EIFS insulation
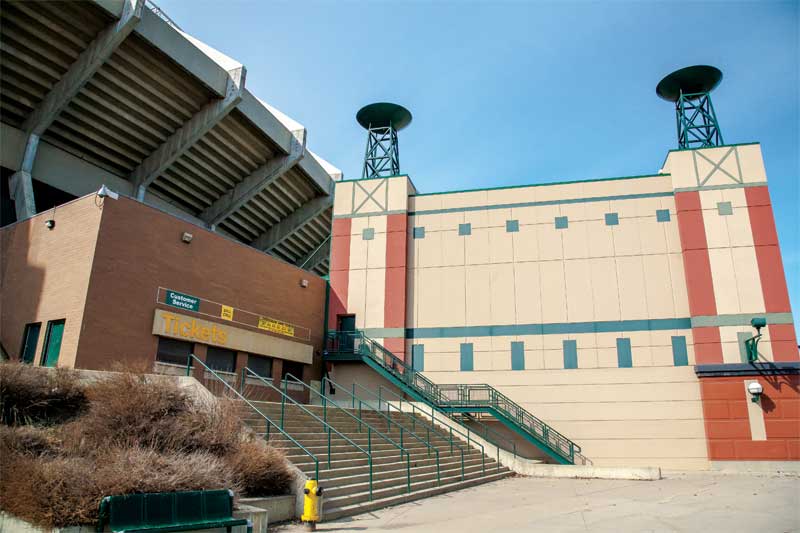
Expectations with performance
One primary benefit of ci is it maintains the enclosure and framing elements at temperatures closer to those of the building interior. With the additional R-value at the exterior, the dewpoint moves toward the outside and, in some cases, exterior to the insulation in the framing cavity. This effect can eliminate or reduce condensation in the enclosure that may otherwise prematurely degrade structural materials.
Further, ci protects against the thermal bridges where structural components, substructure, anchors, and other penetrations reach through to the exterior. For example, uninsulated steel-stud framing in contact with exterior sheathing is an efficient conduit for heat, regardless of how much insulation is packed between the studs. Adding ci across all the steel frame members dramatically cuts heat and cold bridges, boosting overall R-value and reducing U-factor.
Other penetrations through the façade can cause thermal bridging and compromise the ci layer as a result of inadequate detailing or misalignment of the thermal control layer. If the structure includes steel shelf angles without stand-offs, it will transfer heat. Exposed concrete floor slabs and steel penetrations for balconies or canopies can also cause problems.
Windows and doors with thermal breaks not coinciding with the opaque wall’s thermal control location, or where structural members hold off their lintels, can also result in bridging challenges. Sometimes, parapet walls are incorrectly detailed, becoming a building-wide perimeter heat sink. The enclosure design team must track all possible thermal bridging paths. Properly designed, the ci layer cuts U-factor considerably.
Use of ci can also reduce moisture accumulation due to transport of water vapour through envelope materials such as brick or CMU. This mitigation is especially effective when a properly specified and installed WRB is used. Attention to climate zone, the type of wall system employed, and the building’s intended use help ensure proper enclosure function.
Further, the ci layer can serve as part of an air barrier system and moisture barrier protections—an efficient ‘double use’ of a material. For example, extruded polystyrene (XPS) insulation boards can be an effective air barrier material, typically with taped joints and sealed penetrations using silicone- or latex-based sealants compatible with XPS. To determine whether the ci systems employed will perform as a code-compliant air barrier assembly, specifiers can refer to manufacturer data per CAN/ULC S742-11, Standard for Air Barrier Assemblies–Specification, and CAN/ULC S741-08, Standard for Air Barrier Materials–Specification, or ASTM E2357, Standard Test Method for Determining Air Leakage of Air Barrier Assemblies. (Specifications sometimes also refer to ASTM E2178, Standard Test Method for Air Permeance of Building Materials, or ASTM E1677, Standard Specification for Air Barrier Material or System for Low-rise Framed Building Walls.)
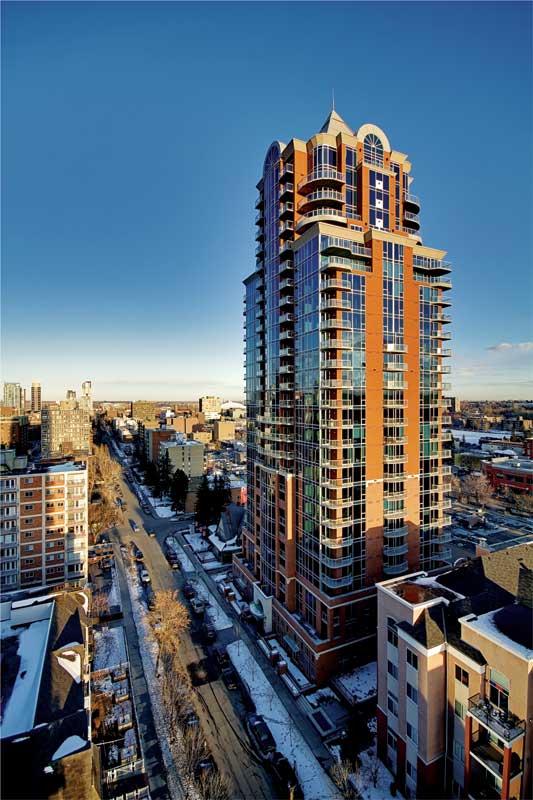
Choice of cladding and ci implications
Before choosing the ci solution, building teams generally select or recommend their cladding system. Esthetics, performance needs, and suitability to the application are among the considerations when choosing a cladding. Construction type, climate zone, and the intended building use help determine where the ci layer is placed in the enclosure assembly. Its location affects construction sequencing and cost, meaning construction preferences may drive the choice of cladding so the ci layer is easy to apply, inspect, and in some cases, repair. When the ci insulation layer is outboard of the structural framing, the detailing and construction tends to be much less complex than when it is interior to the structure, obviating such interruptions as floor slabs.
This usually leaves two options for ci location: behind the cladding or integral to it. Cladding options typically falling outboard of the ci layer include masonry and brick exteriors, as well as panelized metal systems (e.g. aluminum composites), often with mineral wool as the ci layer. Since the ci materials must be supported, the façade attachment hardware can serve in some cases to secure both the cladding and the insulation—examples include clips, horizontal girts, and screws with sealing washers. Other types, such as impaling fasteners, are designed to support insulation alone.
Also exterior to the ci layer are built-up façade cladding systems requiring no penetrating fasteners to attach the insulation, further minimizing thermal bridging. For example, EIFS assemblies can use fully adhered insulation boards to offer good wind load resistance and protect against cracking caused by thermal expansion and contraction.
For cladding systems such as precast or tilt-up concrete panels and masonry cavity walls (e.g. brick veneer), the ci layer is integral. XPS can be employed under various masonry veneer exterior finishes or over steel-stud framing, concrete, or masonry wall structures. Similarly, ci is a feature of rainscreens and rain barrier cladding designs made with metal or aluminum composite panels, fibre-cement board, glass-fibre-reinforced concrete, or other materials. In these assemblies, the chosen insulation must meet minimums for compressive strength and any relevant code requirements.
With many metal cladding systems/rainscreens, joint detailing can influence the selection of the ci material. Rainscreens with masonry veneer or open-joint panels are designed to admit moisture, which is then drained and/or dried through ventilation in the assembly’s cavity or air gap. If exposed to moisture, the ci material should be water-repellent. In some cases, the open joints may also allow ultraviolet (UV) light from the sun past the cladding. Therefore, exposed insulation and barrier materials should be rated for UV degradation. For buildings or parts of a building required to follow noncombustible construction provisions, metal cladding systems incorporating a combustible insulation are required to undergo CAN/ULC S134 assessment to ensure the assembly satisfies the code’s life-safety objectives.