Achieving advanced thermal performance in steel structures
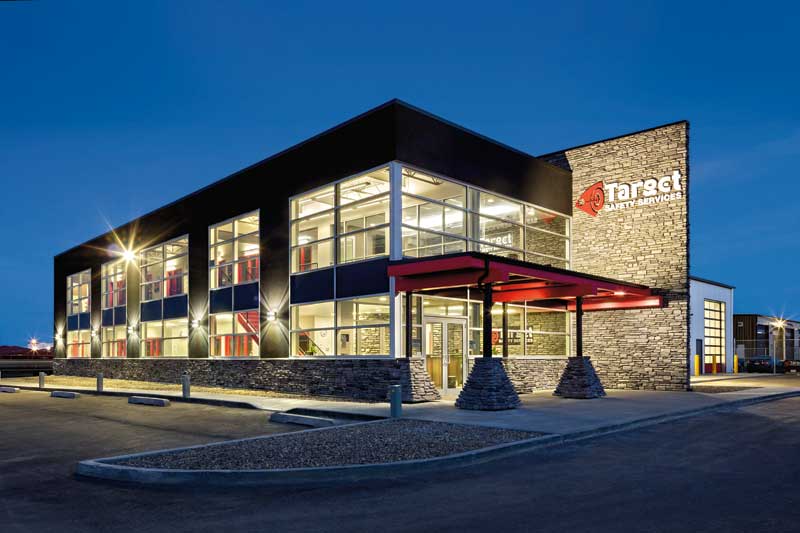
By Rich Grabmeier RRC, LEED AP, and Mark Henry, PE
Canadian energy codes will never be less stringent than they are today. Therefore, it is important to have a firm understanding of the building options available to achieve and outperform regulations. Contrary to some conventional thinking, a ‘systems’ approach to construction can prove an ideal building approach even when high thermal performance is required. Currently, both steel and conventional structures must meet the same code, so there are no real thermal performance advantages by building with a more conventional approach.
In fact, employing a systems building solution can offer numerous energy efficiency benefits. With this building method, each component has the potential to impact thermal performance. Therefore, there are numerous opportunities to enhance efficiency across the building’s envelope.
This article focuses on accurately measuring thermal performance, identifying opportunities to limit thermal bridging, and offering considerations for selecting roof and wall systems. The first step, however, is ensuring the correct energy code requirements are considered. While it seems obvious, double-checking the climate zone and local energy code for the building’s location is always necessary.
Accurately measuring thermal performance
Thermal performance cannot be optimized if it is not accurately measured. U-values quantify heat flow through an entire insulated assembly, providing the most detailed assessment of actual thermal performance. Mathematically, the U-value is equal to the inverse of the R-value (U= 1/R). However, in most assemblies, the R-value of the various components is not additive or accurately calculated and will not predict the performance of the assembly in its entirety.
Focusing on U-values when assessing building assemblies is important because it also accounts for such things as insulation compression and thermal bridging that may occur in an actual assembly.
ASTM C1363, Standard Test Method for Thermal Performance of Building Materials and Envelope Assemblies by Means of a Hot-box Apparatus, outlines the procedure for testing thermal performance and providing accurate insulation information via its namesake equipment. Hot-box apparatuses are state-of-the-art, computerized data-acquisition systems that collect information from multiple sensors used to measure the surface and air temperatures, humidity, airflow, and the total energy consumed during the test period.
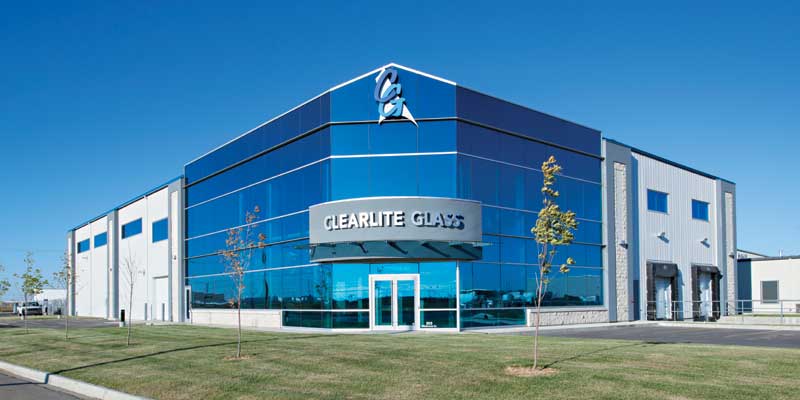
An assembly test specimen representing all the components of the desired building envelope construction is placed in the apparatus. Chambers are installed to both sides of the test specimen. The temperature is dropped to a specified level on one side of the specimen, and the energy needed to achieve and maintain a specified different temperature on the opposite side is measured. A single test can take several days to complete. These results measure the actual heat flow through the assembly, expressed as the actual U-value of the assembly in W/m2K (Btu/hr●sf●F).
A few building product manufacturers test their building products and systems to ensure their systems deliver the energy efficiency promised. While knowing the U-value of the building envelope is necessary to ensure energy codes are met, the actual thermal performance of the building envelope can have a significant impact on the lifetime operating costs and occupant comfort. Knowing the U-value of the building envelope is essential for ensuring HVAC equipment is properly designed for the building—a right-sized mechanical system can have an impact on the long-term cost of operating the building.
Mitigating thermal bridging
Thermal bridging presents a challenge to maximizing thermal performance with any building assembly, and systems construction is no exception. Thermal bridging can occur whenever a more thermally conductive material allows an easy pathway for heat flow. This can occur at the locations where the exterior building skin is attached to the structural system. As steel is thermally conductive, heat can be transferred at these connection points. It can also occur where fibreglass insulation is compressed. If not properly mitigated, thermal bridges can reduce the thermal performance of a steel structure.
When employing a systems construction approach, quality solutions will mitigate thermal bridging. This is accomplished by reducing the compression of the mineral wool or fibreglass insulation at the roof purlins or wall girts, as well as installing thermal spacer blocks along the purlins and girts.