A primer on examining brick masonry
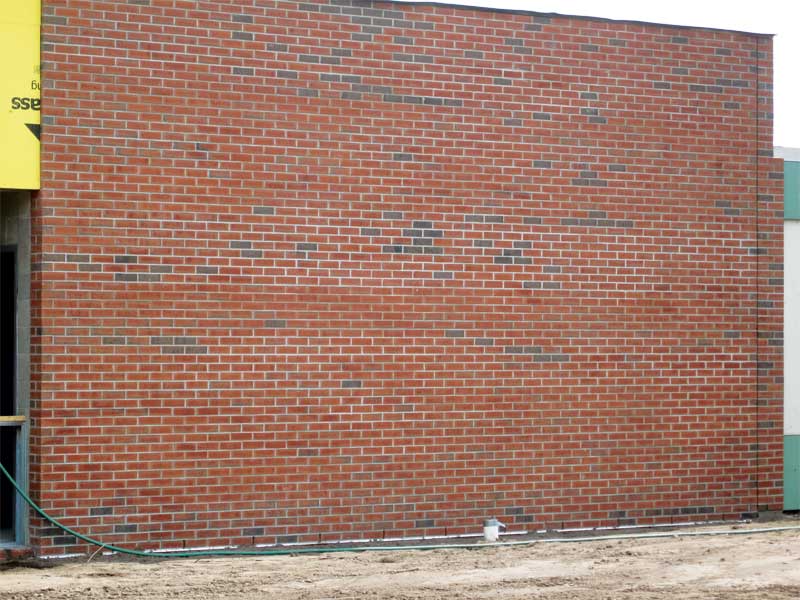
Retempering mortar
Workability is directly related to the amount of moisture remaining in the mortar. Retempering is replacing water lost to evaporation by adding a small amount of water to mortar on the board. Many specifications do not allow retempering mortar, likely due to prohibitions on rewetting concrete.
However, recommendations by ASTM and the Portland Cement Association (PCA) state mortar can be retempered as necessary, but should be discarded after two hours from the time it leaves the mixer. This time limit will be shortened in hot or dry weather. Coloured mortar should not be retempered, as it might dilute the colouring agent.
The mason must get permission from the architect-engineer before retempering mortar if it is prohibited by
the specifications.
Types and grades of brick
Face brick is classified by type (i.e. standards for dimension and shape), and grade (i.e. durability when exposed to extremes of weather). Types of brick are divided into FBX, FBS, and FBA. The first category has the highest standard of dimensional stability and uniform shape, and is preferred by most architects and designers. The irregular shape and dimensions of FBS brick are sometimes desired for their ‘colonial look.’
The grade is divided into SW–Severe Weather Exposure and MW–Moderate Exposure. Virtually all exterior brick in Canada and the United States is ordered as Severe Exposure (SW) grade. Bricks in Canada should be manufactured to CAN/CSA A82.1, Burned Clay Brick (Solid Masonry Units Made from Clay or Shale).
Cleaning brickwork
The safest way to clean brick is with a paddle and brush, using a proprietary cleaner. (Diluted muriatic acid is not allowed.) The mason must protect windows, doors, and other hardware and appliances from damaging effects of the cleaner.
Power-washing can also be effective, but precautions must be taken to prevent damage to the brick. The use of power-washing and the choice of the proprietary cleaner must be approved by the brick manufacturer as well as the architect-engineer. Additionally, some specifications do not allow power-washing, so permission from the architect or engineer must be obtained.
For high-pressure washing, the nozzle must not be too narrow and must not come closer than 152 mm (6 in.) from the face of the brick. Cleaning with power-washing is a four-step process:
- The mason scrapes any mortar smears or tags off the brick with a paddle.
- A power-sprayer completely saturates the wall with water—the more, the better.
- Using a low-pressure sprayer or brush, the mason applies the cleaner.
- The brick is then thoroughly rinsed and scraped as necessary using plenty of water.
Conclusion
This article has explored storage of materials onsite and workmanship practices that can be inspected during a walk-through, along with a discussion on weep holes and the rainscreen wall design. It examined the selection of mortar and workmanship practices leading to weathertight masonry joints, and suggested ways to select appropriate type and grade of brick for the desired esthetic effect and durability qualities. Further, it touched on proper mortar cleaning procedures and warnings about the hazards of pressure-washing.
While this is a good overview of what one should look for while surveying brickwork construction, it is not possible to explain each issue in depth within the confines of a single article. It is the responsibility of readers to do further research if they are interested.
UNIFORM JOINTS |
If the architect/engineer’s representative is concerned about the uniformity of the head joints and bed joints—usually indicated by fatter and thinner joints or poor alignment—the inspector can settle the question with a story pole. To do this, the mason first lays up a portion of the wall where the joints are acceptable to both. The inspector then makes a measuring pole using a 3-m (10-ft) long oak or birch board, marking off the joint spacing on the pole. From there, the inspector uses the pole to occasionally check the alignment and dimensions of the joints. |
Paul Potts is a technical writer and construction administrator. He has worked in the construction industry as an independent contractor and construction administrator for architects, engineers, and owners in Michigan. Potts can be contacted via e-mail at paulpotts1@comcast.net.