A comprehensive scrutiny of building enclosure design and construction
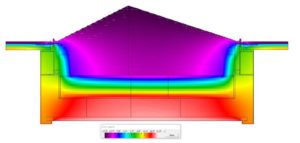
Reviewing specifications
During the design phase, the specifications are recommended to be reviewed by the building envelope specialist in conjunction with the drawings. The evaluation would include:
- durability of specified materials and if they have a demonstrated history of effectiveness;
- potential compatibility/adhesion concerns between different materials (e.g. pressure preservative treated wood reaction to metals, bituminous materials reaction to some plastics);
- requirements for project-specific thermal analysis (effective U/R-value calculations) of window and wall assemblies and roofs;
- applicable performance standards (e.g. for window performance);
- shop drawing requirements and specific information needed for each work result; and
- inclusion of quality assurance and control (QA/C) measures such as site air and water testing.
The author recommends including a separate Division 1 building envelope QA/C section to highlight to the contractors the required level of site reviews and testing.
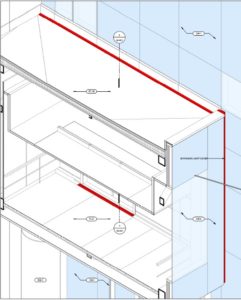
Test reports
Manufacturer and contractor test reports, such as window performance testing or thermal calculations (i.e. U/R-value calculations and condensation resistance), are recommended to be evaluated in detail by the design team/building envelope specialist to verify the testing/modelling is in conformance with the performance requirements of the specifications and associated specified standards, as this could impact the in-situ performance of the building enclosure and overall energy efficiency of the facility.
Preconstruction phase
The preconstruction phase of a project is where the design team/building envelope consultant reviews the contractor’s understanding of the design intent and fundamental building science principles. This is completed through shop drawing and other submittal reviews and pre-installation meetings.
Submittal reviews
Building enclosure submittals typically include product data sheets, manufacturer installation instructions, and applicable test reports. Data sheets often include product limitations that should be reviewed along with the planned time of installation and potential issues with transitions to other materials or assemblies.
Similar to the design phase, isometric details in shop drawings can be very useful to illustrate complex relationships before they are installed. They can help identify potential concerns, critical sequencing, and provide a clearer picture for the contractor and all trades on how to execute the work. In Figure 7, the detail illustrates the sequencing of installation of a curtain wall stack (movement) joint at a custom vertical fin, and shows the continuity of the control layers. Similarly, Figure 8 illustrates a curtain wall with an extended guardrail supported by internal aluminum posts penetrating the top of the curtain wall. Continuity of both and air and water barriers is critical at these penetrations, and these isometric details help both the contractor and specialist better understand how this detail should be installed, reducing the potential for error, such as an in-situ discontinuity, and future leaks.
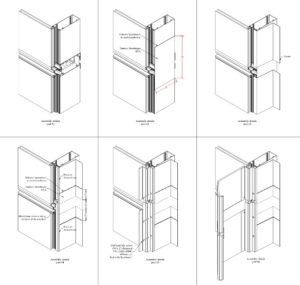
Pre-installation meetings
Pre-installation meetings are often ignored or overlooked. These meeting are recommended to include the general contractor (GC), architect, building envelope specialist, site foreperson, and trades. These meetings allow the contractor to explain how he or she intends to execute the work and discuss critical installation procedures, sequences, or compatibility concerns with the design team. It provides the opportunity for feedback and collaboration between the design team and contractor, and to get a thorough understanding from the trades so everyone is working toward the same goal—a durable, well-performing enclosure. It can also be an opportunity for the contractor to get acceptance from consultants on how they plan to execute the work and any unique installation procedures they may be employing.
Construction phase
The construction phase of the project is where the all the above is executed. To achieve the contract documents’ design intent, the following QA/C activities should be implemented:
- building envelope assembly mockups;
- enhanced building envelope site review;
- in-situ performance testing; and
- onsite quality control (QC) including co-ordination between trades, checklists, and a dedicated building envelope superintendent.