Firestopping and effective compartmentation
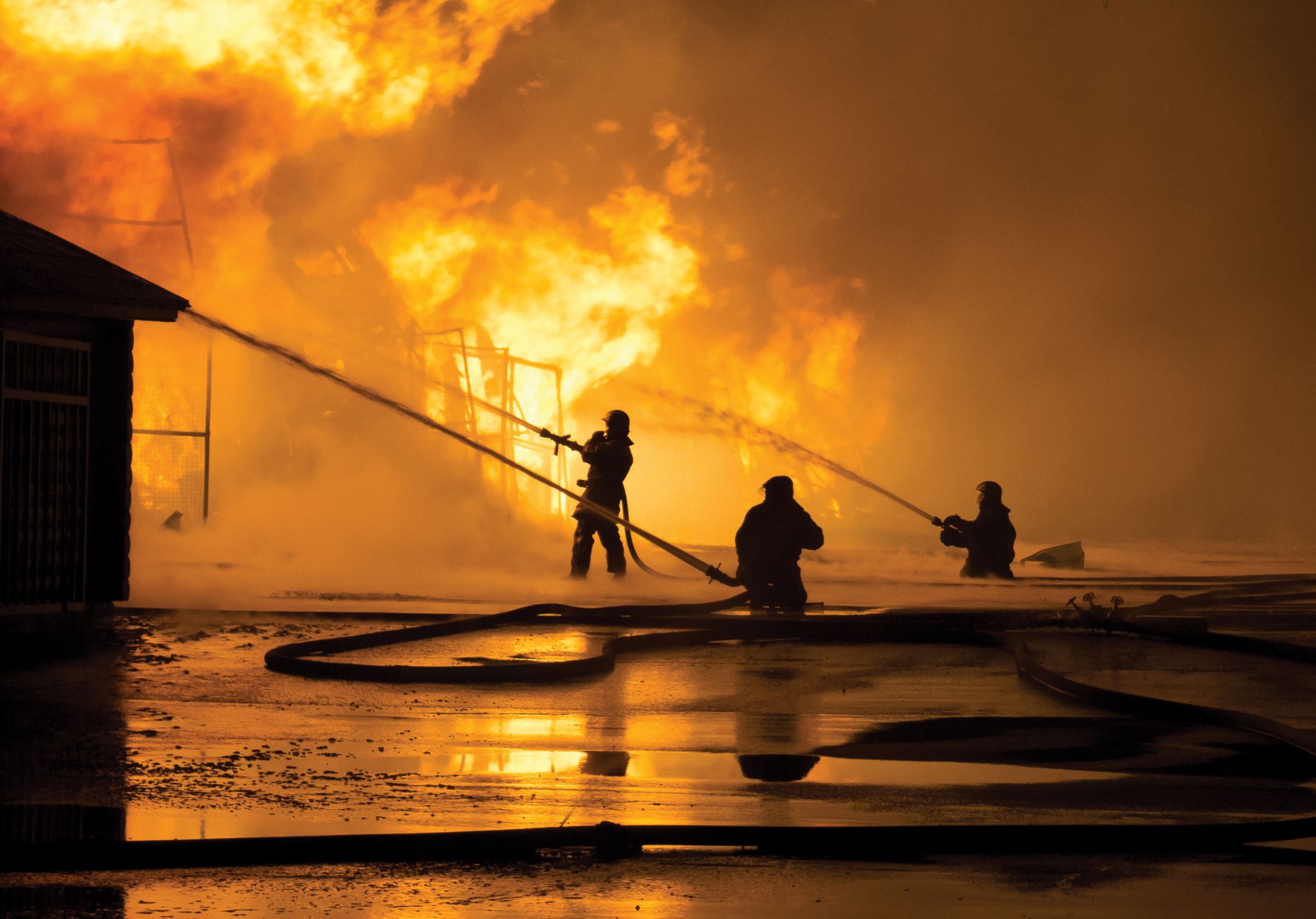
By Bill McHugh, CSC, CSI, MBA
Fire resistance is one of the oldest fire protection strategies. Fire-resistance-rated walls and floors, joined together continuously, mean ‘effective compartmentation’ for a room of any size. Materials specified in MasterFormat 07 84 00−Firestopping maintain the continuity of this fire-resistance-rated construction through treating the holes made for cables, ducts, pipes, and joints.
This continuity is specified in the National Building Code of Canada (NBC) in Appendix A, 3.1.8.3:
The continuity of a fire separation shall be maintained where it abuts another fire separation, a floor, a ceiling, a roof, or an exterior wall assembly.
In addition to installed firestop systems, fire and smoke dampers, fire-rated glazing, and both rolling and swinging doors (and their hardware) round out effective compartmentation. These tested and listed systems provide fire resistance continuity and smoke-resistant properties protecting people, property, and providing continuous service in buildings as well.
In 3.1.7.1, 3.1.7.1, NBC states fire-resistance ratings shall be determined on the basis of tests conducted in conformance with Underwriters Laboratories (CAN/UL) S101, Standard Methods of Fire Endurance Tests of Building Construction Materials, which provides the requirements for testing the wall or floor to determine suitability for use of products. There are also calculated methods for fire resistance used with concrete assemblies.
NBC 3.1.8.1.(1)(b) states the intent of the code for compartmentation:
Although a fire separation is not always required to have a fire-resistance rating, the fire separation should act as a barrier to the spread of smoke and fire until some response is initiated. If the fire-resistance rating of a fire separation is waived on the basis of the presence of an automatic sprinkler system, it is intended that the fire separation will be constructed so that it will remain in place and act as a barrier against the spread of smoke for a period of time until the sprinklers have actuated and controlled the fire.
This passage sets up the need for firestopping that provides both fire and smoke resistance; NBC’s 3.1.9−Penetrations specifies CAN/UL S115, Fire Tests of Fire stop Systems. Including the air leakage rating—L—adds the resistance to smoke to those assemblies needing it. The requirement the barrier resist the passage of smoke invokes the need for an L-rated firestop system.
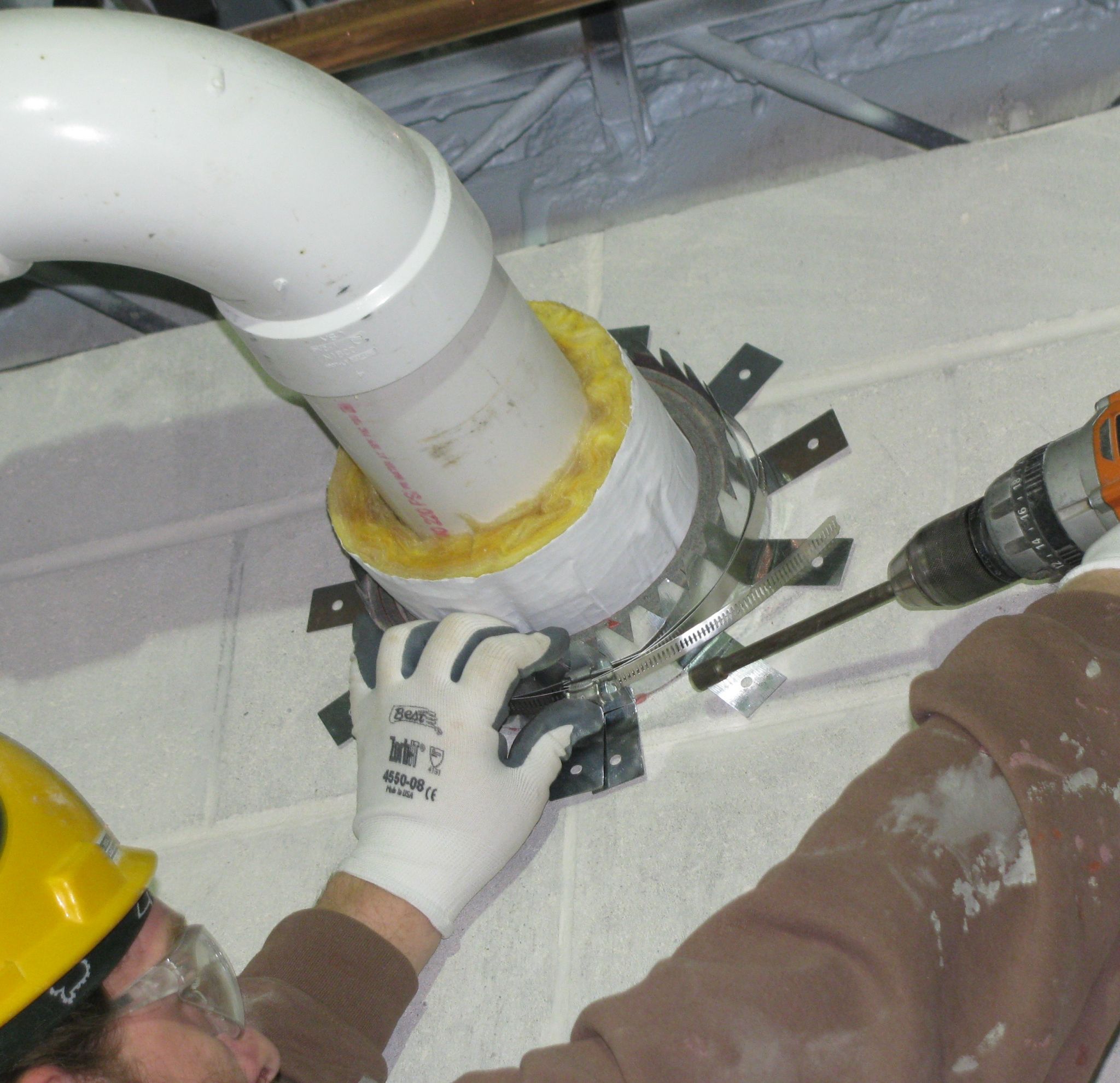
In NBC 3.1.9.1.−Fire Stopping of Service Penetrations, it states:
Except as required by Sentence (2), piping, tubing, ducts, chimneys, optical fibre cables, electrical wires and cables, totally enclosed noncombustible raceways, electrical outlet boxes and other similar building services that penetrate a fire separation or a membrane forming part of an assembly required to have a fire-resistance rating shall be:
a) sealed by a fire stop system that, when subjected to the fire test method in CAN/UL-S115, “Fire Tests of Firestop Systems,” has an F rating not less than the fire-protection rating required for closures in the fire separation in conformance with Table 3.1.8.4., or (50pa, plastics)
b) cast in place (see Appendix A).
The (b) is the exception that allows concrete, equal thickness to the wall or floor, for a limited number of penetrating items and opening size. However, some penetrating items may not be compatible with cement-based products, so one must verify with the penetrating item manufacturer compatibility of the items with products used for firestop systems.
In short, penetrations and joints through fire-resistance-rated construction that forms effective compartmentation are to be treated with firestopping that has been tested and listed to CAN/UL S115. Without systems, there is no idea how long or short a fire-resistance rating duration may be. Some manufacturers provide engineering judgments when no tested and listed system exists from any manufacturer to address a field condition. Engineering judgments are provided by the manufacturer, testing laboratory, or fire protection engineer in conjunction with the manufacturer.
DIIM
Those in the fire-resistance-rated construction industry have been working to improve the installed product reliability from many perspectives. Each industry has been working to design and build better systems, focusing on the proper design, installation, inspection, and maintenance (DIIM) of each component to ensure the continuity of effective compartmentation.
Design
The first component is the design, where tested and listed systems are designed by manufacturers who submit products for testing at labs such as UL/ULC, FM Approvals (FM), or Intertek. The tested and listed systems provide ‘suitability for use statements’ for the fire- and smoke-resistant products that become systems once installed by those who understand the specific application’s installation instructions. Testing the products continues to provide more competitive and better systems, designed by manufacturers of effective compartmentation products.
While product design is obviously important, the rest of the ‘DIIM’ acronym can be just as critical. In other words, while testing provides suitability for use of products in specific applications, how do the products get handled once they leave the factory or manufacturer/distributor warehouse? This is where the focus to make these products really work begins—with the installation, inspection, and maintenance of barriers and their fire and smoke protection features.
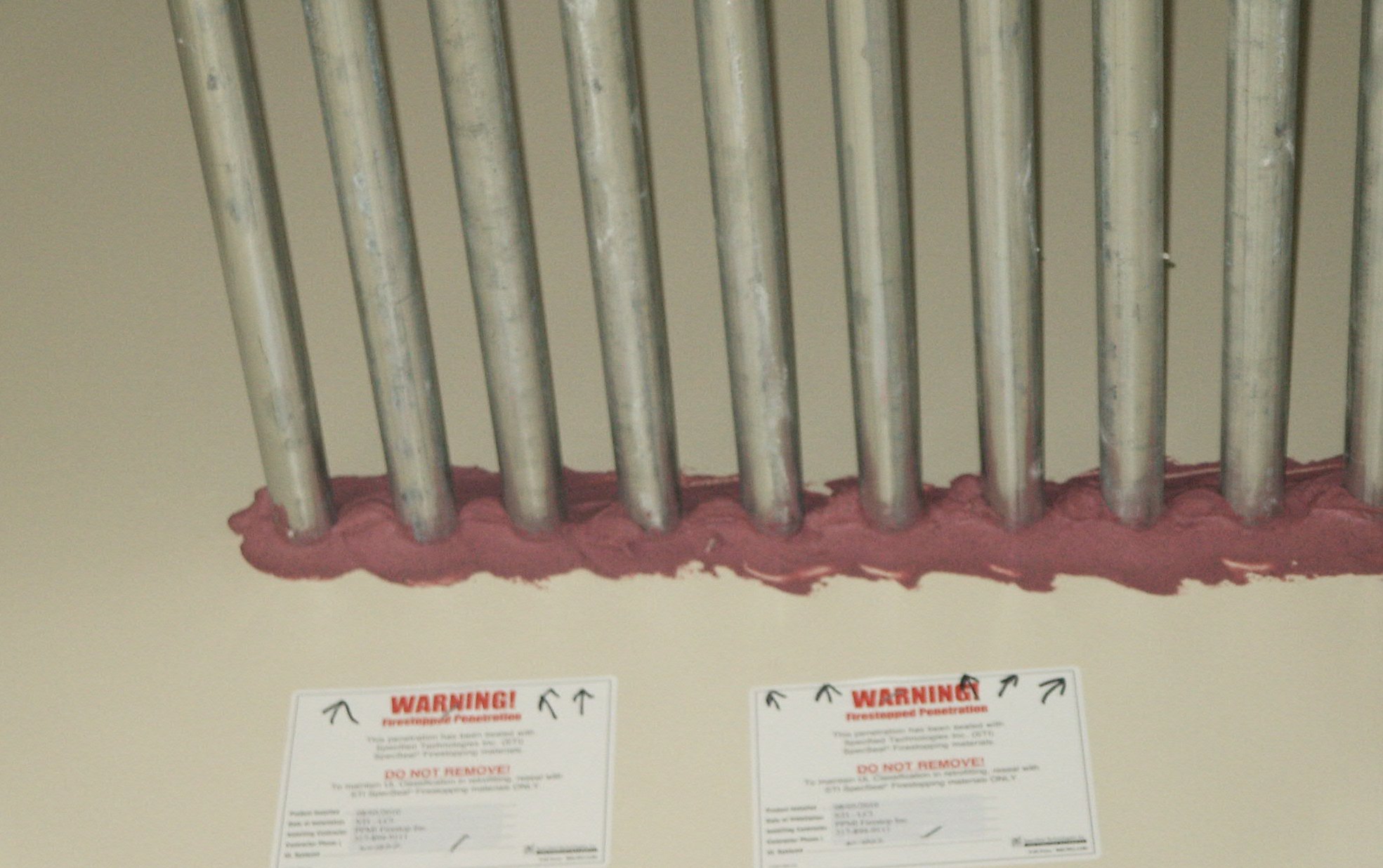
Installation
In North America, each component of the fire-resistance/effective compartmentation industry has targeted the ‘installation’ aspect of DIIM through focus on the company and the workforce in different ways.
Third-party contractor company management system audits by laboratories like FM Approvals and UL/ULC, plus firestop/containment worker apprenticeship education for the workforce enhances quality and reliability of the installed systems. Focusing on firestopping as a trade means the systems are understood by management and the workforce, which is critical for success.
The Firestop Contractors International Association (FCIA) collaborated with FM Approvals to build FM 4991, Standard for the Approval of Firestop Contractors, and with UL/ULC to develop the UL/ULC Qualified Firestop Contractor Program. Both programs provide general contractors, building owners and managers, fire marshals, and building code officials a way to quantifiably qualify firestop contractor companies. The FM 4991 and UL Qualified Firestop Contractor Programs showcase those who have invested in their company’s understanding of the zero-tolerance quality installation process. While not used by other industries, those companies who are FM-approved or UL/ULC-qualified have procedures in place to understand the installation protocol for fire and smoke protection features.
FM 4991 or UL/ULC Qualified Firestop Contractors become approved or qualified after a company and onsite audit of their management system takes place. A person who has passed a rigorous FM or UL/ULC industry exam based on FCIA’s Firestop Manual of Practice and systems selection/analysis becomes a Designated Responsible Individual (DRI) once appointed by the FM-approved or UL/ULC-qualified company.
Inspection
In the United States, the 2012 International Building Code (IBC) has a requirement for third-party, independent, special inspection of firestop installations using ASTM E2174, Standard for the Inspection of Installed Penetration Firestops, and ASTM E2393, Standard Practice for Onsite Inspection of Installed Fire Resistive Joint Systems and Perimeter Fire Barriers.
Firestop special inspection is required for structures that are 23 m (75 ft) and higher above lowest fire department access and critical occupancies found in IBC’s Table 1604.5. Buildings such as education, assembly, and other occupancies may be subject to these inspections from the 1604.5 reference.
In Canada, under NBC, there is no code requirement for special inspection. However, in the construction documents, some specifiers may use Part 3−Execution to require ASTM E2174 and ASTM E2393 independent inspection. This provides the check the management system of the contractor installing firestopping is working properly. Installation plus inspection, by both contractor and inspection agency, determines reliability of the installed products.
There is also a program that qualifies the special inspection agency to perform these inspections. The International Accreditation Services (IAS), a subsidiary of the International Code Council, (ICC) has Accreditation Criteria (AC) 291, Special Inspection Agencies. IAS provides accreditation to building departments, testing laboratories, and other organizations throughout North America. In Canada, building departments in British Columbia have become accredited.
FCIA’s Standards Committee worked with IAS to build the firestopping section of AC 291. Sprayed and intumescent fire-resistive materials used for fireproofing are sometimes specified to have special inspection as well.
FCIA was the code proponent that petitioned to include ASTM E2174 and ASTM E2393 in the U.S. codes, having collaborated with manufacturers and consultants in the industry. Now, the National Building Code of Canada (NBC) is the standards committee’s next focus.
Regardless of where the inspection takes place in North America, the inspectors and special inspection agencies need to have qualifications. FM Approvals and UL/ULC both offer a firestop exam that provides individuals a quantifiable level of knowledge. This complements the IAS AC 291 accreditation with people who have knowledge of the DIIM protocol.
Maintenance
Firestopping is included in the fire-resistance-rated system maintenance sections of codes throughout the world, including the National Fire Code of Canada (NFC) and the International Fire Code (IFC) in the United States. In the IFC, there is a requirement for annual inspection by the building owner under Section 703.1. The NFC, in Division B–Part 2, “Building and Occupant Fire Safety,” also has a short but specific reference to maintenance:
2.2.1.2–Damage to Fire SeparationS: where fire separations are damaged so as to affect their integrity, they shall be repaired so that the integrity of the fire separation is maintained.
In other words, where fire separations are damaged, they shall be repaired. The requirement does not state whether the breaches need to be repaired immediately or in a period of time acceptable to the authority having jurisdiction (AHJ).
The interesting thing about fire-resistance-rated construction is the apathy that exists about breaches in the assemblies. Regardless of whether the breach is from a hole in the separation, a door not latching, or other reason, building occupants really do not perceive there is a safety risk. However, the breach may be just as serious as a fire alarm or sprinkler system not working. As with anything, some building occupancies are better at maintaining fire separations than others.
Firestopping as a system
Throughout North America, firestopping is a systems-oriented installation; the product alone does not get a rating. This means products must be installed to the tested and listed ‘system’ from a nationally recognized testing laboratory before the entire assembly becomes a fire and life safety tested and listed firestop system.
It takes a firestop specialty contractor to understand all the details involved to get this done correctly so it works. He or she also knows how to supervise the workforce so people do not get ‘creative’ in the field and veer away from the tested and listed systems. Then, a special inspection agency that focuses on firestopping is needed to determine whether a tested and listed system is properly installed. Special inspection agencies need to have the same diligence judging the contractor personnel to have adhered to the tested and listed system.
Once the tested and listed firestop system is installed and the building is turned over to the building owner and/or manager, it must be managed and maintained. This is, of course, easier in theory than in practice. After the building is constructed, new pipe and cables are placed to serve building occupants. These make holes in the walls and floors that need to be treated to keep the continuity in place for fire and smoke resistance.
Specialty firestop contractors understand how to maintain continuity of fire resistance. They also know what needs to be done to keep the rest of the fire- and smoke-resistant system effective, including fire-rated doors and dampers in addition to restoring the continuity to the wall itself.
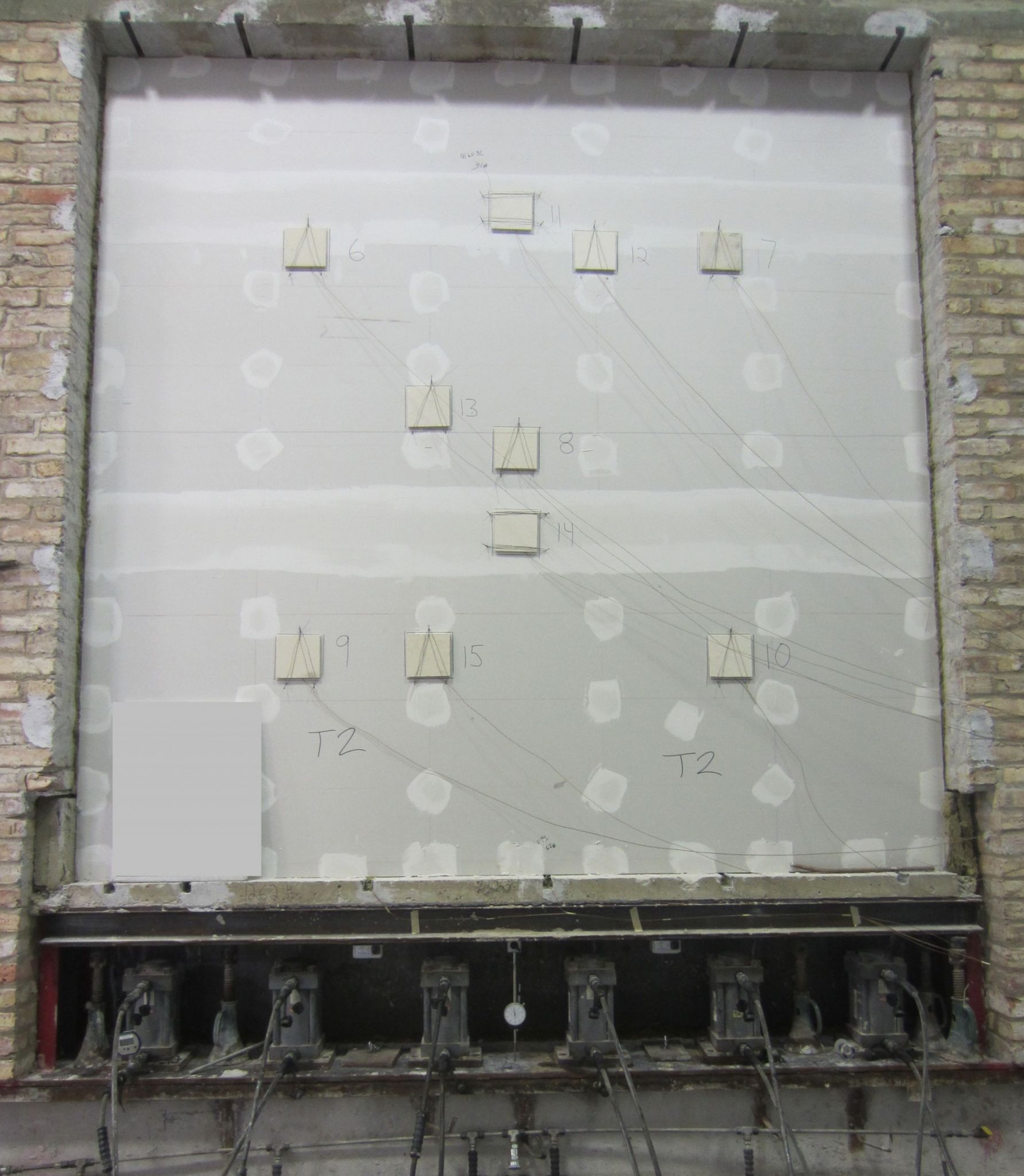
and fastener heads are included. Photo courtesy Underwriters Laboratories
Fire and smoke dampers
The fire and smoke damper industry seems to focus on maintenance/testing during the building lifecycle for ongoing reliability. In Canada, fire dampers and firestop flaps shall be inspected annually, or on an approved time schedule.
Healthcare occupancies have dampers inspected during the initial commissioning, after the first year, and then every six years thereafter. According to the healthcare industry, this is due to the high degree of maintenance and management that takes place in these structures, which results in greater reliability with less inspection. FCIA members also provide fire damper inspections to provide greater reliability of fire-resistance-rated and smoke-resistant assemblies.
For installation, the National Energy Management Institute (NEMI) developed a program for contractors who are signatory to and use workers exclusively from the Sheet Metal Workers Union of North America. Sheet metal contractors who install fire and smoke dampers and opt into this program have their management systems audited by the U.S. National Energy Management Institute, but this is not required by code on either side of the border.
Fire-rated glazing
Other than those provided by manufacturers, this author knows of no unique organized installation programs for fire-rated glazing assemblies and frames. In the United States, inspection has been made more uniform through a new labelling format as specified by the 2012 IBC. Glazing is also included as a fire-resistance-rated construction maintenance item requiring visual inspection in IFC 703.1.
Rolling fire doors
Rolling fire doors are the largest opening in a fire-resistance-rated assembly. The Institute of Door Dealers Education and Accreditation (IDEA) program provides recognition for knowledgeable rolling fire door installers. Used in both Canada and the United States, the individual certification is a knowledge-based program where those with at least two years of experience in the field who pass an industry exam become certified.
Swinging fire doors and hardware
Manufacturers provide installation instructions, and there is available training for the workforce from organizations such as the carpenters and labourers unions. The Door and Hardware Institute’s (DHI’s) Foundation for Door Safety and Security has built a credible education program to qualify individuals performing fire door inspections in existing buildings. Its relationship with Intertek has produced a Certified Fire Door Inspector Professional designation, along with a company certification that involves an audit of the inspection firm.
In Canada, doors are mentioned in ‘Closures’ sections:
Where closures are damaged so as to affect the integrity of their fire-protection rating, the damaged closures shall be repaired so that the integrity of the closures is maintained.
Under “Maintenance of Closures,” it states:
1. Closures in fire separations shall be maintained to ensure that they are operable at all times by:
(a) keeping fusible links and heat or smoke-actuated devices undamaged and free of paint and dirt;
(b) keeping guides, bearings and stay rolls clean and lubricated;
(c) making necessary adjustments and repairs to door hardware and accessories to ensure proper closing and latching; and
(d) repairing or replacing inoperative parts of hold-open devices and automatic releasing devices.
Under the section, “Operation of closures,” it sets the requirements for operation of these important devices:
Closures in fire separations shall not be obstructed, blocked, wedged open, or altered in any way that would prevent the intended operation of the closure…
Doors in fire separations shall be inspected monthly.
1. Doors in fire separations in occupied buildings shall be checked as frequently as necessary to ensure that they remain closed.
2. Sentence (1) does not apply to:
(a) doors designed to close automatically in the event of a fire, or
(b) doors for which an approved fire safety plan contains provisions for closing in the event of a fire.
Walls and floors
Inspections of fire- and smoke-resistant assemblies occasionally find walls and floors with large holes, but no penetrating items such as pipes or cables. Those walls need to have their continuity restored through reconstruction of the wall to the tested and listed system design.
Structural steel fireproofing
This industry has seen several changes the past few years. At the International Code Council’s past two code development cycles, increased bond strength and inspection frequencies have been added to the requirements for high-rise buildings. UL/ULC has a Qualified Fireproofing Contractors Program similar to the one for the firestopping industry. The National Fireproofing Contractors Association (NFCA) provides education to those seeking individual certification as well. The heart of this program is individual personnel examination on the association’s manuals and education modules. With a minimum of two years of experience and membership in NFCA, the company is also recognized through a Contractor Accreditation Program.
Conclusion
The Firestop Contractors International Association has been involved in the development of better reliability of firestopping installations by building a body of knowledge via the Firestop Manual of Practice, which serves as the study guide for FM and UL/ULC exams. At the same time, FCIA committees work with FM Approvals, ULC, ASTM, IAS, and others to implement the DIIM for these systems.
Where is the future of fire resistance going? Qualifications are continually being developed for companies that install and inspect fire-resistance-rated construction, and all the features of fire and smoke protection features. This author also believes building owners and managers from many other occupancies other than healthcare will become more aware that breaches in fire- and smoke-resistance-rated construction must be repaired to keep the effective compartmentation working.
Bill McHugh, CSC, CSI, MBA,is executive director of the Firestop Contractors International Association (FCIA). He has been involved in Division 07 items since 1981, and in firestopping since 1990. McHugh has been FCIA executive director since the organization’s beginning in 1998. He has written, spoken, and moderated symposiums throughout North American and the Middle East. A past CSI institute director, and chapter and region president, McHugh chairs the ASTM E2174/2393 Standards Task Group and served on the International Code Council’s (ICC’s) Ad-hoc committee on Terrorism-resistant Buildings. He can be reached at bill@fcia.org.