Specifying precast terrazzo
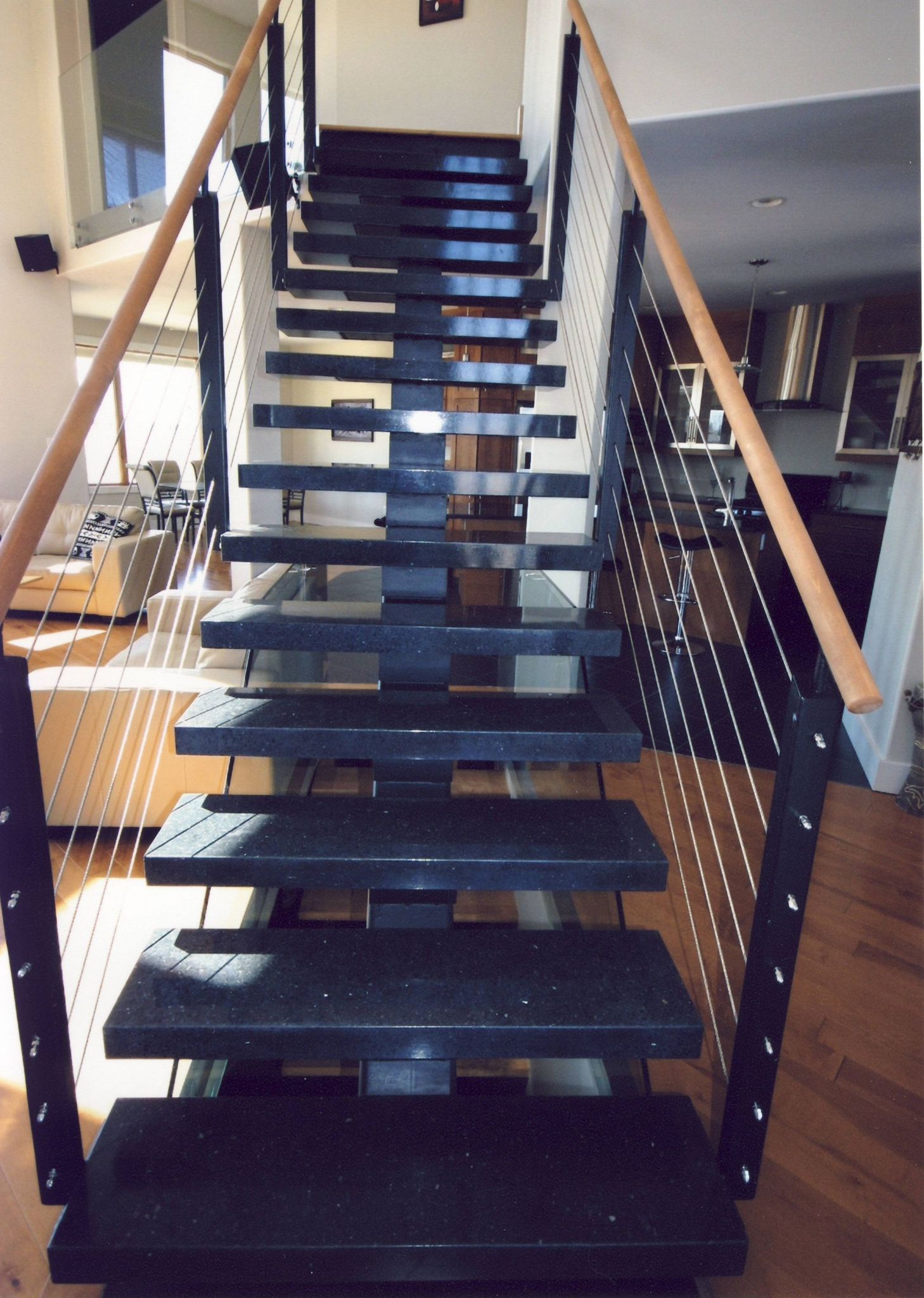
By Tony Torriano
Terrazzo has been valued for its durability and subtle beauty with an uncompromising record of performance dating back over a thousand years. From its ancient beginnings, terrazzo has been used for floors in many commercial, industrial, and institutional applications because it typically lasts the lifetime of the building. Today, many installations that are more than 30 years old are still being used and can be viewed throughout Canada.1
Terrazzo, from the Italian word terrace, was discovered by Venetian workers who found another use for discarded marble remnants created from odd-sized pieces of custom marble fabrications. As a form of art, terrazzo was used in stately buildings from numerous palaces across Europe to the Vatican, and eventually brought to North America by skilled European immigrants. Now, its evolution continues with the introduction of a precast version, which offers new benefits while providing the same durability.
The precast process
Precast terrazzo has many of the same properties as traditional terrazzo, but it is made offsite. The precast product evolved from terrazzo flooring and is a composite material that is blended and poured into a prefabricated mould. After it has cured or hardened, the component is removed, and the surface is ground smooth with mechanical equipment. It consists of marble, quartz, or granite aggregates, glass, or other suitable particles commonly referred to as ‘chips’ that are bonded together with cement or a polymeric compound, such as epoxy.
Since precast terrazzo elements are made in a controlled, easy-to-work-in environment, and often employ similar mechanical equipment to finish marble or granite, the final surfaces offer excellent quality and appearance. Precast terrazzo offers excellent durability because it is a composite that consists of the same material, binder, and aggregates, throughout the thickness of the element—as the surface wears, the same particles and binder are exposed.
Colour options for precast terrazzo are virtually unlimited. This is because the binder that holds all aggregate particles together can be pigmented to almost any colour. Further, with the ever-increasing use of epoxy as the binder, the spectrum of colour and accuracy is unlimited. Nature’s palette of colour is available from marble aggregates that are sourced within North America or Europe. Other aggregates, like granite or washed screened and graded stones, can also be incorporated into precast terrazzo elements.
Recycled materials like glass, porcelain, or concrete can be added to terrazzo elements in varying proportions. These recycled materials are from pre- or post-consumer sources that are washed, sorted, screened, and available in various mesh sizes. Fine particles from these materials can also replace fine manufactured particles used in terrazzo elements.
The use of glass allows the addition of unique or bold colours for accents or special effects that are unavailable with natural marble aggregates. Crushed sheet mirror or manufactured mirror particles in different colours may be used for sparkle or to add depth to a terrazzo surface. Nacre (i.e. mother of pearl), another natural material, can also be added to provide special effects. The combination of new and recycled materials allows for virtually any design or pattern.
Custom fabrications that utilize special shapes, curved surfaces, or larger thickness are possible with precast terrazzo elements since forms may be constructed with limitless options. In comparison to using flat stock to construct design elements, precast terrazzo offers the ability to make almost any concept reality while maintaining reasonable costs.