Moisture management strategies for stone verandas
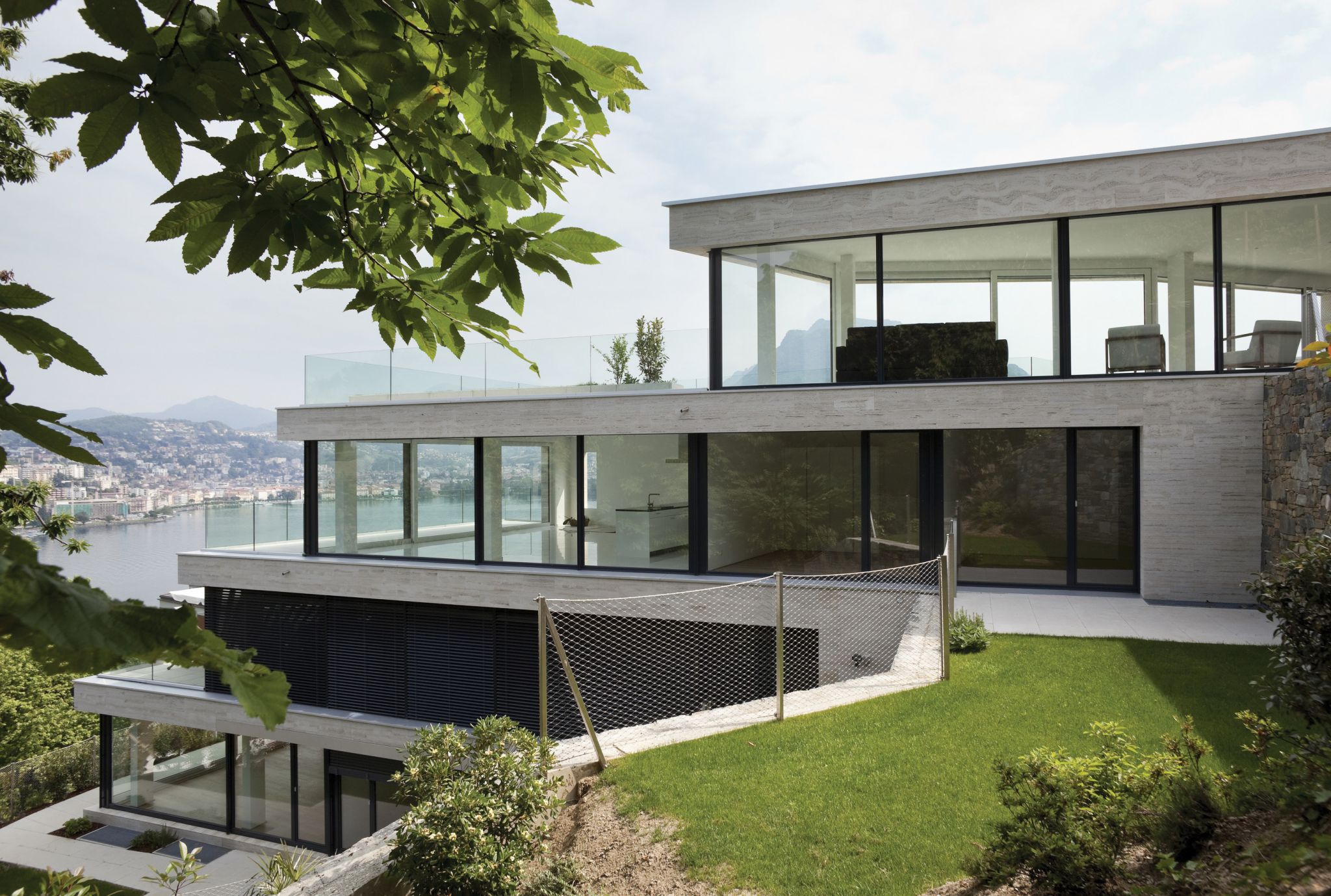
By John Koester and Mark A. Johnson
A comprehensive moisture management plan for any construction detail must include moisture-resistant materials (e.g. dampproofing, water-resistant barriers [WRBs], and waterproofing) and a slope-to-drain—a designed elevation change to direct liquid water to a desired low point away from, off of, and out of the construction detail. It also involves an unobstructed pathway/void for liquid water to exit the construction detail.
Although these points seem reasonable and straightforward, they are nonetheless often ignored. One rationale for this could be a design professional’s unwavering, but erroneous, belief in simply specifying ‘waterproofing’ and ruling out the need for anything else. After all, there are hundreds of high-quality moisture-resistant products out there with claims they can waterproof anything and everything.
Informed, experienced construction professionals who understand the capabilities of waterproofing materials may instead use the phrase, “moisture management system (or plan).” While ‘waterproofing’ is easier to say, true waterproofing can be hard to accomplish. Many manufacturers know this—a roofing assembly’s warranty, for example, often has a clause specifying it will be made void if there is ponding water on the system.
Applying moisture management to verandas
Verandas, or porticos, are commonly used as second-storey decks. (When they are employed as walkways to connect exterior doorways to rooms they are also called galleries, promenades, or loggias.) The characteristics that add degrees of difficulty to these moisture management systems are that they need to be durable for traffic-bearing, while also meeting esthetic requirements. A common overlayment that would accommodate these requirements would be stone in various patterns.
General descriptions of the construction details making up verandas include:
- three exterior, insulated, structural bearing walls supporting the structural deck;
- insulated structural deck;
- waterproofing system on the structural deck’s top surface, which may run down over the structural walls’ exterior face or terminate at the deck perimeter;
- code-compliant perimeter restraining system (e.g. railing) or parapet walls of various heights and designs;
- support system for the stone overlayment that may include some type of pedestal paver assembly for each stone corner, or a mortar bedding system;
- flashing system where the veranda meets the main dwelling’s exterior wall;
- slope-to-drain on the traffic-bearing stone’s surface;
- slope-to-drain on the top surface of the waterproofing material applied to the structural deck’s slope-to-drain;
- unobstructed pathway for liquid water (that may be present on the slope-to-drain top surface of the traffic-bearing stone) to run off the veranda; and
- unobstructed pathway for the liquid water (that may be present on the slope-to-drain waterproofed surface of the structural deck) to run off, and out, of the mortar bedding or stone pedestal system.
No task for amateurs
The design and execution of the construction phase of a stone-overlaid veranda’s moisture management system is no task for the uninformed professional. (Utilizing the services of a professional consulting firm or choosing a waterproofing systems manufacturer that has trained representatives to oversee design and execution and warranty the system is a real option.) There are several factors that add even more difficulty to this type of construction.
As Figure 1 illustrates, the top surfaces of these verandas may have accumulations of snow and/or ice on them for long periods. Further, they may have other surfaces (e.g. roofs) that drain onto them, and the interior living areas underneath are heated and/or cooled. These extremes of temperature have to be accommodated within the deck’s insulated structural areas.
Verandas have numerous critical construction details, any of which—if not properly designed, constructed, and maintained—can cause serious moisture management problems. Some of the most common detail failures include improper or inadequate:
- slope-to-drain on the traffic-bearing stone’s top surface (Figure 2);
- slope-to-drain on the structural deck’s top surface (Figure 3);
- waterproofing system on structural deck;
- pathway for any accumulated liquid water to run off the stone overlayment’s traffic-bearing surface;
- pathway for any accumulated liquid water on the structural deck’s waterproof surface to drain out;
- perimeter details (e.g. scuppers or eavestroughs) for liquid water to flow off deck surface;
- railing mounts;
- insulation of structural deck; and
- venting of structural deck joist cavities.
The slope on the surface of the traffic-bearing stone is the first critical point. Slope-to-drain is commonly called out in inches-per-foot or fractions of inches-per-foot. The minimum slope-to-drain acceptable for low-slope stone surfaces is 1/4 in. per 1 ft (i.e. approximately 6.4 per 305 mm). According to industry resource, Smoley’s Parallel Tables of Slopes and Rises, this is equal to 2.08 per cent.
The distance liquid water has to travel before it is away from, off of, and out of a construction detail is also critical. The greater the distance, the greater the chance this flow will be interrupted or slowed by some sort of obstruction, such as organic debris, snow, or ice. Distance travelled is in direct proportion to time; the amount of time liquid water is in contact with a construction detail is in direct proportion to the amount of water it may absorb. Additionally, the longer water is on, in, or near a construction detail, the greater the chance it may go through a freeze-thaw cycle. It should go without saying this slope-to-drain should be diverted away from the main dwelling whenever possible (Figure 4).
A second area of focus is the structural deck’s top surface. Unfortunately, this is one of the most overlooked and neglected aspects of good moisture management of verandas. The top surface should be sloped-to-drain the aforementioned 2.08 per cent minimum to at least match the minimum slope-to-drain of the traffic-bearing stone; it could be sloped even more. However, designers should keep accessibility requirements in mind for safety and universal access.
Stone traffic-bearing surfaces rarely conform to the requirements of a barrier system. They absorb moisture, and there will be voids/cracks in grouting mortar and bedding mortar. Moisture ingresses down to the waterproof system on the top surface of the structural deck as shown in Figure 4.
Further thoughts on slopes and paths
With inadequate slope-to-drain on the structural deck, moisture accumulates and ponds. At best, it will drain slowly. In the long term, continuous moisture presence in and on this construction detail greatly increases the risk of a leak through the waterproofing system, accelerating the deterioration of the bedding system and stone overlayment.
Dead-level structural members with continuous loads on them do not remain dead level for long—they belly down. This is one of the lesser-known problems with inadequate slope-to-drain or dead level structural decks. They are usually constructed with structural members like steel beams, concrete blanks, dimensional lumber, or fabricated wood joists. These materials have crowns in them, and are installed crown up. If they are supported dead-level at each end, half of the structural deck will be pitched back toward the main dwelling (Figure 5). The structural consultant typically calculate loads with a ‘camber’ in the joist and/or beam.
An improper or inadequate pathway for liquid water to run off the waterproofing system on the structural deck and out of the support detail for the stone overlayment is another point of concern. Water may want to run in a design direction with slope-to-drain, but it needs a space (i.e. void) to run through. This drainage plane is created by:
- height of the support pedestals in the stone paver pedestal system; and
- drainage plane system installed under the bedding mortar of the stone overlayment and over the waterproofing. (These drainage plane materials also act as a protection mat for the waterproofing system.)
The perimeter detail’s requirement for liquid water to flow off the edge of the sloped-to-drain top surface of the traffic-bearing stone is critical. However, it can be complicated by esthetic requirements. This water may transport varying amounts of impurities—soot, dirt, organic debris, and dissolved salt and minerals—from the stone overlayment. If this water comes in contact with the vertical face of the exterior wall, it will stain. Besides the negative esthetics that may result from this contact, there is the potential for structural deterioration of the vertical wall.
Inadequate perimeter drainage detailing is the most common design flaw. The design and construction of these details conflict with the esthetic appeal of the rooflines and face of the supporting wall, and designers are too restrictive with them. In doing so, they can be too small and too few to be functional.
Internal roof drains are an option that should be entertained to accommodate the drainage for both the surface and internal liquid water. There are numerous high-quality systems available, such as double- and duplex-drains. However, the negatives of this option include:
- drains have restrictive openings that can be easily obstructed by roof debris;
- designing slope-to-drain for 360 degrees to a centre point (i.e. drain opening) is labour-intensive and complicated;
- waterproofing connection details for this type of drainage system are extremely critical; and
- plumbing required to convey this liquid water has its own critical details in that it must be leak-free and insulated for temperature control (condensation control).
Another common detailing design flaw occurs when the required elevation step-downs are not designed in the traffic-bearing surface perimeters. As a result, the perimeter drainage detail material actually dams up a certain amount of water as it attempts to enter the detail. This point can also be a material transition, and consequently, a stress point. A perimeter roof leak, more so than an in-the-plane roof leak, is likely to also become a wall leak (Figure 6).
The perimeter drainage detail allowing the water on the waterproofed surface of the structural deck and in the bedding mortar of the stone overlayment system to drain is also critical. Good waterproofing practices require additional, stronger materials at points where the surface of structural details change (i.e. horizontal to vertical at the edge of structural deck). If such strengthening means adding layers of material, the elevation change created by thicker material has to be designed into the perimeter elevations of the structural deck. The design and execution of this construction detail will, in most cases, involve some type of skirt or facia board (Figure 7).
Thinking hole-istically
Improper or inadequate railing mounts are another common failure point. This author knows of projects where the structural engineers, waterproofers, and stone masons performed their work to perfection, only to have the railing installers drill holes through everything (Figure 8).
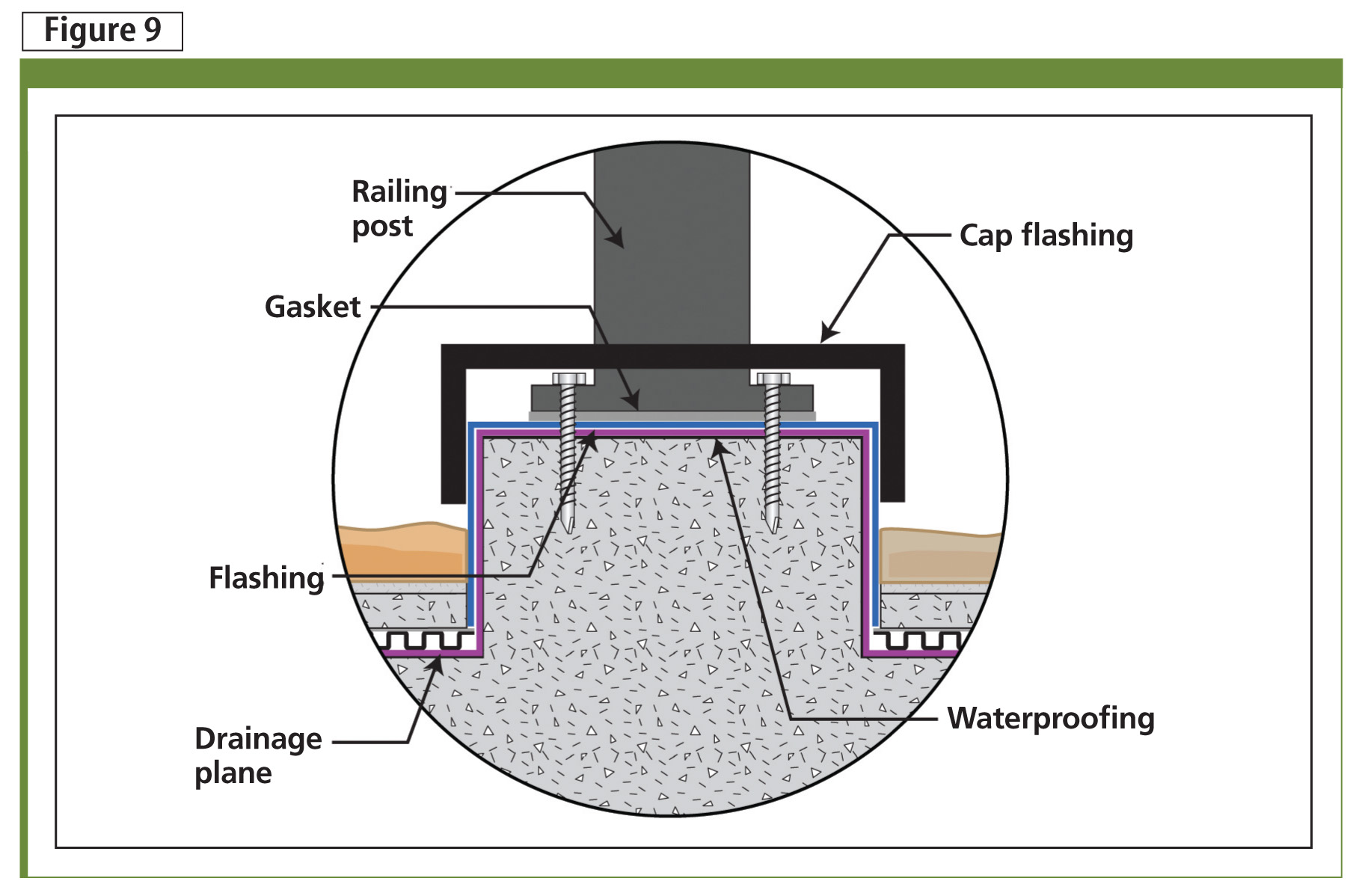
Building industry professionals are well aware a significant percentage of all labour procedures conducted on waterproofing systems, including installation, are conducted by those who do not understand waterproofing and are seldom held responsible for their premature failures—electricians, plumbers, mechanical equipment installers, masons, sign-installers, et cetera. It is not uncommon for waterproofing to be damaged after installation during ongoing construction. This is the very issue causing waterproofing system warranties to contain clauses such as “when applied according to the procedures, instructions and conditions of [said company] as set forth in our written specifications, technical data sheets, and application instructions.”
In cases of improper or inadequate railing installation, the structural deck designer missed an important requirement. The structural deck design should have had pedestal curbs built in and up past the top surface of the stone overlayment; further, these components should have been included into the waterproofing system (Figure 9).
Insulation considerations
The structural deck of a veranda has to be insulated, and the insulation material has to be kept dry. The insulation part is easy; keeping it dry is not. The two main sources of moisture are infiltration of liquid water (a leak) and water vapour driven into the insulation from the interior living area where it meets a dew point and condenses into water droplets (liquid water).
The types of materials used to construct the structural deck of a veranda are as numerous as the methods of how to best insulate them. There are, however, several best practice design points (Figure 10):
- waterproof system to keep liquid water from entering from above;
- structurally sound deck;
- system to vent the open area between the bottom of the decking and top of insulation in the joist cavities;
- insulation;
- vapour-retarding system on the interior walls behind the interior sheathing;
- moisture-resistant interior sheathing; and
- vapour-resistant coating or covering on the exterior surface of the interior sheathing.
(There are many examples of structural decks—poured concrete or solid concrete plank, for example—that will not accept all these systems.)
Conclusion
Stone-overlaid veranda decks above living areas need to be designed and built with great care. In many areas, they are becoming more common because of local zoning requirements—for example, some municipalities in Canada have restrictions on hard-surface landscaping that affects surface water runoff. When designed and built correctly, they can be a beneficial, long-lasting detail (with proper maintenance). When they are not, however, moisture-related failures may be imminent.
John Koester is founder and CEO of Masonry Technology Inc. (MTI). With construction experience dating back almost 40 years, he has been a card-carrying mason and cement-finisher, and for many years operated his own masonry construction business in Minnesota. Koester has extensive background in waterproofing systems in the areas of forensics, design, and installation oversight—both in restoration and complete re-roofing projects. He can be contacted via e-mail at john@mtidry.com.
Mark A. Johnson is MTI’s media technologies manager, having spent three decades as an instructor at the secondary, college, and graduate level. His responsibilities include the design and management of MTI’s web communications, educational and training programs, and all digital marketing efforts. Johnson can be reached at mark@mtidry.com.