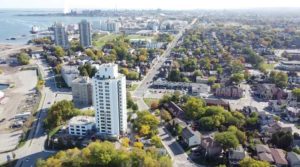
By Alejandra Nieto
Deep energy renovations of commercial and multi-unit residential buildings are critical if cities want to tackle their climate emissions on a large scale. Energy renovation could provide up to 55 per cent of the greenhouse gas (GHG) emissions reductions needed to meet 2030 targets, aligning cities with a 1.5 C (34.7 F) trajectory. Recently, federal leaders in both Canada and the U.S. have announced initiatives that will simultaneously help meet environmental protection targets as well as drive post-pandemic economic recovery.
Presently, renovation rates are one to two per cent of the building stock per year, with an average energy use intensity (EUI) reduction of less than 15 per cent—to make a significant impact, EUI reductions should be between 30 and 50 per cent. For these changes to happen, energy codes must add measures to strengthen energy reduction while not raising resultant emissions. Also, policy development around energy retrofits and the adoption of high-performance net-zero buildings needs to be accelerated. Where codes and policy changes are not enough, project teams and research and development investments require government support to enhance building technologies and materials.
Throughout North America, model energy codes are evolving for higher energy efficiency. Local code adoption and policy development have also strengthened governmental positions on energy reduction targets, adopting building retrofit requirements. For example, the Climate Emergency Action Plan in Vancouver has the aim to reduce carbon emissions by half by 2030 (based on 2007 values), which will require focus on buildings, specifically retrofitting existing buildings.
In addition to energy and emissions conservations, building retrofits improve occupant health and comfort. In many cases, existing buildings are poorly insulated, or not insulated at all, and leaky, resulting in excess heat loss and reduced thermal comfort. Mechanical systems are often outdated and inefficient, requiring constant maintenance. In this way, improvements to indoor health and comfort can also be vital drivers for building renewal investment.
Where to start?
Existing older buildings will typically have little to no insulation within the envelope, resulting in excess heat loss and increased energy consumption. More importantly, they often do not have any water-resistive and air barriers, making them very leaky and further increasing energy losses. The addition of insulation in exterior walls and roofs, combined with a water-resistive barrier (also acting as part of the air barrier system), is integral to improving building performance, reducing leaks, and creating more comfortable indoor environments.
Material selection for the building envelope is key. Stone wool insulation solutions (batt, semi-rigid, and rigid board for continuous insulation) are an ideal option for myriad reasons, including the most obvious one—superior performance in improving thermal efficiency. Buildings with stone wool insulation, for example, can see up to 70 per cent reduction in heating and cooling costs. Beyond this, the other benefits of specifying stone wool insulation for the building envelope include greater protection from fire, noise, and moisture, each of which can adversely affect the integrity of the building’s structure and long-term durability as well as the health and well-being of its occupants.
All retrofits are not the same
Each building retrofit comes with unique conditions and challenges, requiring a holistic and long-term planning approach to ensure a project achieves its overall goals and specific targets. A comprehensive plan should include auditing the building’s existing conditions, assessing potential energy conservation measures that will be applied, analyzing cost and long-term capital requirements, and understanding the social and economic effects on the building occupants (current and future).
Though energy conservation is the primary driver for most large-scale retrofits today, there will be some other consistent criteria that should be considered in different types of commercial retrofits. Many are driven by the needs of the occupants. For example:
Construction Canada received the following Letter to the Editor:
Dear Editor,
The article was very interesting and informative. Could the author comment on the affect this type of roof energy design has on the design roof snow load? The reason I ask is research in the United States indicates the roof load is significantly higher than for roofs retrofitted with R-30 insulation than older buildings. It has been observed that freezer buildings have significantly greater depths of snow on roofs than on the ground. I have also seen the same condition in my work in Canada. The commonly accepted explanation is the surface of the roofs are cooler than the ground and snow does not melt as normally expected. Up to this time, the ratio between ground to roof snow loads is based on extensive field studies done in the 1960s, so the reduction of snow depth on the roof is based on how roofs were insulated during this period. A discussion of increased snow loads on building roofs is well presented in the article “Snow Thermal Factors for Structural Renovations” in Structure Magazine (https://issuu.com/structuremag/docs/structure-jun19-zmag/24). The latest version of ASCE-7-22 has incorporated these factors. Also, for low sloped roofs, structural engineers are now required to calculate the roof deflections when checking for ponding of rain. With more snow on roofs, the roof deflects more which encourages ponding of rain during spring melting. Care needs to be taken to improve drainage off roofs to ensure ponding is less likely.
David P. Thompson, M.Sc., P.Eng.
Principal
KTA Structural Engineers
David,
Thank you for the comment and the interesting article that you shared.
The engineering design of the roof is outside my area of expertise, and generally as an insulation manufacturer. For this application, we always recommend to work with a structural engineer to ensure the roof system can withstand the upgraded insulation. That said, I do believe that we should not compromise energy efficiency due to structural concerns. When dealing with a roof retrofit, different approaches can be taken both in terms of the type and amount of insulation added, and whether updates are required to the structure. For example, if the existing roof structure is not being reinforced and you need to limit the added weight, one can opt for a hybrid retrofit solution where you can use a layer of foam plastic insulation and then add the non-combustible and dimensionally stable stone wool insulation as a cover board. Stone wool roof insulation can also be tapered and available as a cant strip to assist with drainage requirements.
I would be happy to connect you with our building science team if you have any additional questions, or you can reach our technical service team at http://www.rockwool.com/contactus .