Transparency in the Built Environment: Calculating and assessing embodied energy of construction materials
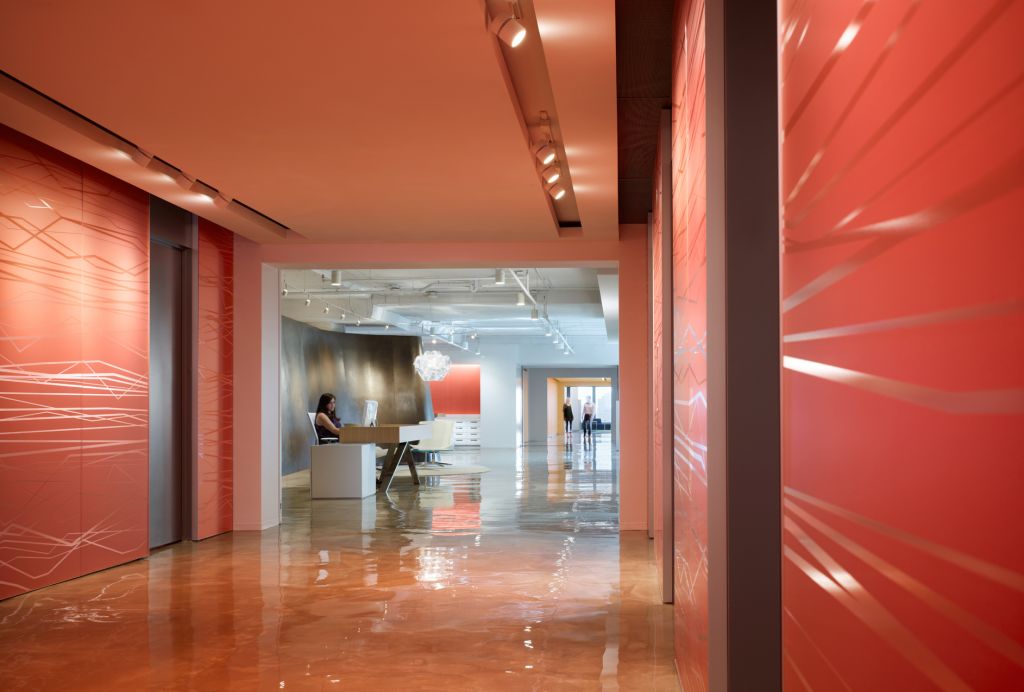
By Francesca Desmarais, Marion Lawson, and Thaddeus Owen
Specifiers, architects, engineers, and contractors use numerous criteria when choosing materials and products for a building. Questions they must consider include:
- Does the product perform well?
- Does the product match the project esthetics? and
- Does the product fit the budget?
Energy consumption and carbon footprint are also key product attributes. Reducing energy and greenhouse gas (GHG) emissions from building construction and operations are critical steps the construction industry can take to reduce the risks of climate change.
Each building product consumes energy throughout its lifecycle. These different lifecycle stages include:
- raw material extraction;
- raw material transport;
- product manufacture;
- product transport and distribution;
- installation;
- maintenance and use; and
- product disposal or recycling.
The total energy used for all stages is referred to as the product’s embodied energy. In Canada, it accounts for approximately eight per cent of the national energy consumption (Figure 1). A building product’s carbon footprint refers to the GHG emissions released as a result of burning fossil fuels to produce energy to create the product.
Embodied energy and building materials
The embodied energy of materials usually represents about 20 to 25 per cent of the building’s total energy consumption over its lifetime (averaging 50 to 60 years), with operational energy—heating, cooling, plug loads, and maintenance—accounting for the remaining 75 to 80 per cent. As building designs become more efficient and minimize operational loads, the embodied energy of materials becomes a larger percentage of a building’s total energy consumption.
Therefore, it is important to consider the impact of building products in order to design carbon-neutral buildings. For example, on move-in day for a new building, 100 per cent of its energy footprint is associated with the embodied energy of the materials used to construct the building. Operational energy will then accrue over time, but during the first 15 to 17 years, the materials themselves have a larger energy impact than the energy required to run the building (Figure 2). Low-energy building products are critical to achieve energy and GHG reductions.
Architecture 2030
In order to catalyze progress toward using building products that reduce the risks of climate change, the non-profit organization Architecture 2030 issued its 2030 Challenge for Products in February 2011. This initiative is a global, voluntary, and incremental roadmap for building products to achieve a 50 per cent smaller carbon footprint than the average for that product category.
The challenge creates a framework for the global building sector to collaboratively work toward low-energy and low-carbon building products. Architecture 2030 challenges manufacturers to calculate and publish the energy consumption and carbon footprints of building products and to use these analyses to reduce their impact. It also challenges architects, designers, and specifiers to request this information from their product representatives, use the information to make informed, low-carbon decisions, and ultimately specify building products meeting the challenge’s targets.
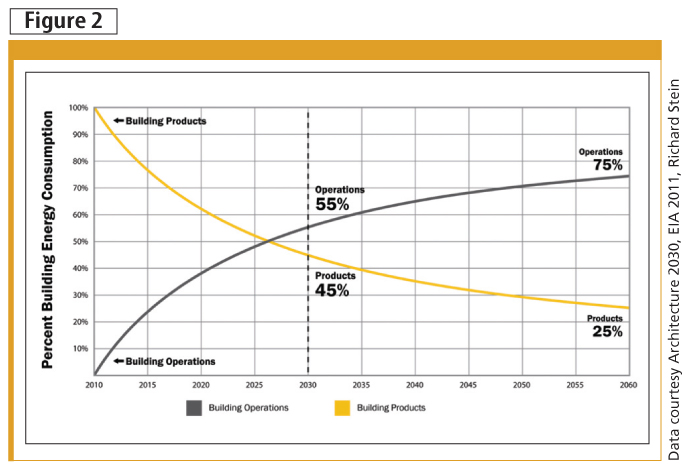
As consumers increasingly request product energy consumption information, the hope is manufacturers will become more transparent with their product information. By increasing transparency, manufacturers are more easily able to identify and communicate the major areas of focus during production in order to make their products more sustainable. The challenge is to then find a standardized method of reporting these environmental impacts in a consistent way across the industry. The Environmental Product Declaration (EPD) has risen as one of the most prevalent tools for reporting a material’s lifecycle impacts.
Understanding EPDs
An EPD is a document disclosing the lifecycle environmental performance of products and services. It usually includes results of impact assessments (e.g. Global Warming Potential), lifecycle inventory results (e.g. water consumption, embodied energy), and other non-lifecycle assessment (LCA) data (e.g. recycled content, list of environmental certifications). An EPD does not, however, constitute a claim of environmental superiority. It is intended to be an objective document developed following International Organization for Standardization (ISO) guidelines and it must be supported by a critically-reviewed LCA. ISO 14025, Environmental Labels and Declarations–Type III Environmental Declarations: Principles and Procedures, is the governing standard for EPDs. In order for an EPD to be verified, the supporting LCA must comply with:
- ISO 14040, Environmental Management–Lifecycle Assessment: Principles and Framework;
- ISO 14044, Environmental Management: Lifecycle Assessment: Requirements and Guidelines; and
- the relevant Product Category Rule (PCR) for that product type.
The EPD must also be registered by a qualified third-party EPD provider to ensure the reported data is credible, accurate, and complies with the Product Category Rules.

An EPD is essentially a summary of an LCA and, is similarly owned by the product manufacturer or service provider. A lifecycle assessment measures a product or service’s potential environmental impacts (e.g. global warming) from the time raw materials are extracted through production until the product is disposed of or recycled at the end of its life. An LCA report may total more than 200 pages and can be written and organized in a way difficult for the casual reader to glean information. An EPD, on the other hand, summarizes the key results from an LCA in a consistent format developed with the user of the results in mind.
Both EPDs and LCAs are based on a Product Category Rule. According to ISO 14025, Environmental Labels and Declarations–Type III Environmental Declarations: Principles and Procedures, a PCR is a set of specific rules, requirements, and guidelines for developing Type III environmental declarations, including EPDs. PCRs are written to ensure the LCA and EPD are performed according to the prescriptive language in the PCR, so all LCAs and EPDs created in a specific product category follow the same rules. For example, all EPDs created for carpeting use the same set of PCRs.
Someone comparing EPDs using the same PCR and created for the same company can have reasonable assurance the differences in impacts are valid. However, EPDs following the same PCRs but originating from different manufacturers may not be directly comparable. Due to variations in the data used and results obtained, the environmental impacts of products from different manufacturers may have a large range of uncertainty. Consequently, small variations in environmental impacts between two different companies’ products may not be as significant as if comparing two products manufactured by the same company.
As the LCA field develops and more customers begin requesting them, the reports, methods, and guidelines will become increasingly stringent. The ultimate goal is LCAs will all be comparable, and the increase in requests will stimulate additional work focused on achieving comparability between manufacturers.
In the building design and construction industry, EPDs can be used to help specifiers and purchasers identify manufacturers who are working to understand the environmental impact of their products and the associated hotspots in their product’s lifecycle. By completing an EPD, a manufacturer can identify which phases of manufacturing have the greatest environmental impacts and work to develop a method to lessen those impacts. Specifiers can use the EPD to obtain data on the product’s embodied energy and carbon and this data can then be used to select materials with a smaller energy footprint.
Building design
To better understand the impact embodied energy has on building projects, the architecture and engineering firm Cannon Design (which has offices in Toronto and Vancouver) conducted a research study on the embodied energy of building materials. The goal was to calculate and evaluate the embodied energy of materials and to use these findings to determine the total amount of embodied energy in two interior build-out projects. The research focused on evaluating existing calculation tools and collecting embodied energy data from publicly available sources such as EPDs and the University of Bath’s Inventory of Carbon and Energy (ICE).1
This investigation led to the development of Mbod-E—an interactive embodied energy calculator designed specifically for building projects—as well as Material LIFE, an embodied energy material selection guide for designers.2
Mbod-E is formatted to cater directly to the building industry. Embodied energy is typically measured in megajoules (MJ) per kg—a unit of measure not suitable for construction materials since these products are not usually quantified by weight. Embodied energy units in Mbod-E have been converted to more applicable construction units, such as MJ per square metre or foot, MJ per linear metre or foot, etc.
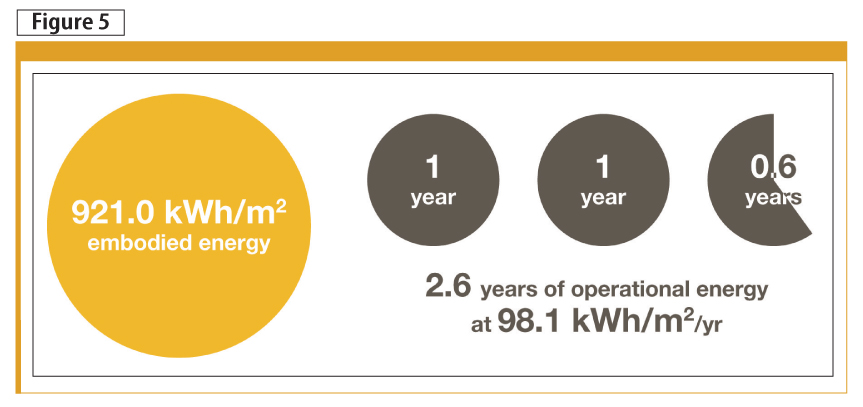
Material LIFE is a complementary embodied energy guidefocusing on interior products and organized according to ASTM International categories, allowing for quick embodied energy comparisons between various material types. After developing Mbod-E and Material LIFE, these new tools were tested by conducting an embodied energy evaluation on two corporate interior build-out projects—the firm’s Chicago and Washington, D.C., offices.
Case studies
In 2012, the Cannon Design Chicago office relocated to a new building in the city. The new office is a 5590-m2 (60,205-sf) build-out of one floor in an office tower. The project was recently certified Platinum under Leadership in Energy and Environmental Design (LEED)–Commercial Interiors (CI) by U.S. Green Building Council (USGBC). Tracking embodied energy was one of the many sustainability goals for the project and embodied energy analysis of different products considered for the project was provided throughout the design. Embodied energy was tracked and calculated for all the materials used in the project, excluding ancillary furnishings and mechanical equipment due to the complexity of these components. Whenever possible, the research team collected product and manufacturer-specific data from Environmental Product Declarations. However, when this information was not available for particular products, industry averages from the ICE database were applied.
Information regarding embodied energy was also built into the request for proposal language submitted to furnishings manufacturers. The responses to the requests were mixed, with some manufacturers providing detailed, product-specific LCAs and others providing only a general sustainability summary.
The total embodied energy for the Chicago office was calculated to be 5.15 million MJ or 921 MJ/m2 (85.6 MJ/sf). As illustrated by Figure 4, the most energy-intensive categories are movable furnishings and floor finishes. Furniture itself represents more than half of the interior build out’s embodied energy, even though all systems seating was reused from the office’s prior location.
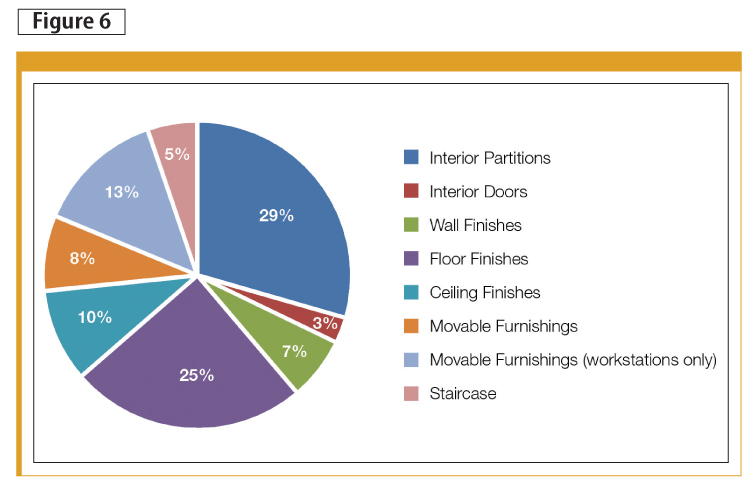
To better understand the magnitude of the project’s embodied energy, the embodied energy of 921 MJ/m2—which is equivalent to 255.8 kWh/m2 (1 MJ is equal to 0.278 kWh)—was compared to the modelled operational energy. The project was modelled and operational energy was projected to be 98.1 kWh/m2/yr (31.1 kBtu/sf). Therefore, the energy embodied in the interior architectural components and furnishings is equal to over 2.5 years’ worth of operational energy (Figure 5). If the embodied energy of mechanical, electrical, and plumbing (MEP) equipment had been included, the energy built into these systems would have totalled to be an even longer term of operational energy use.
This comparison of embodied versus operational is particularly important in a commercial tenant improvement project since a leasehold is measured on a short-term basis—sometimes as short as five years. Longer lease periods, combined with the reuse of existing systems, help mitigate the embodied energy impact on a project’s overall energy footprint.
During the Chicago office’s relocation, Cannon Design’s Washington, D.C., team also began the design of its new space; the project was used as the second case study for embodied energy tracking. The new office encompasses 1890 m2 (20,336 sf) on two floors of an office building in Arlington, Virginia. The project is also targeting LEED-CI Platinum and has high energy goals. The design concept of this office included the construction of a new steel and wood communicating stair connecting the two floors, which the team hypothesized would increase the embodied energy of the project compared to the Chicago office.
The total embodied energy for the project was measured to be 860,740 MJ or 455.3 MJ/m2 (42.3 MJ/sf). Compared to the Chicago office, this total value was significantly lower mostly due to the fact the Washington, D.C., office elected to reuse all its existing workstations, systems seating, and conferencing furniture. Additional workstations were only purchased to complement the expansion project. As demonstrated by the Chicago office case study, furniture systems are the largest contributor to the embodied energy footprint of interior construction projects. The most energy-intensive categories in the Washington D.C. office were interior partitions and floor finishes.
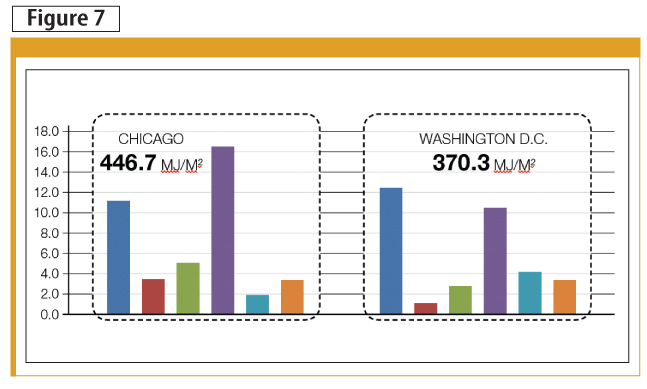
Figure 6 illustrates the distribution of embodied energy for the Washington, D.C., project. In the end, the construction of the communicating staircase represents only five per cent of the total energy embodied in the project, and this impact is far less significant than the movable furnishings category. To provide an accurate comparison between the two projects, movable furnishings were subtracted, as well as the staircase from the Washington D.C. office. Once standardized, the results are much more comparable and replicable (Figure 7). The intent is to continue such evaluations on projects so an embodied energy baseline can be established for projects.
Conclusion
The research discussed in this article shows there is a demand for embodied energy data, as well as overall transparency from manufacturers to permit this flow of information. As more manufacturers publish EPDs, it will become increasingly easier to highlight manufacturers who are taking the necessary steps to reduce the energy footprint of their manufacturing processes. However, decisions are not made in a vacuum, and looking at embodied energy alone is not enough. Designers and manufacturers must study the energy and carbon impacts of a product, as well as other lifecycle and human health impacts including global warming potential, eutrophication, and chemicals of concern.
Complete product transparency is a challenging endeavour to say the least, but it can be achieved through the collaborative effort of manufacturers, designers, specifiers, builders, and third party participants. The tools and standards exist for manufacturers, designers, and specifiers to make better-informed choices about sustainable materials. It now falls to manufacturers to use those tools, and designers to request product disclosure.
Notes
1 The complete database is available online at opus.bath.ac.uk/12382. (back to top)
2 The material selection guide, Material LIFE, is available at media.cannondesign.com/uploads/files/MaterialLife-9-6.pdf. (back to top)
Francesca Desmarais is the director of Architecture 2030’s Challenge for Products. She supports other Architecture 2030 initiatives with in-depth technical research and analysis. Desmarais can be contacted at desmarais@architecture2030.org.
Marion Lawson is a sustainability consultant at Cannon Design. She was part of the Material LIFE and Mbod-E calculator development team and participates in the firm’s continued research on Environmental Product Declarations (EPDs), lifecycle assessments (LCAs), and Health Product Declarations. Lawson can be reached via e-mail at mlawson@cannondesign.com.
Thaddeus Owen is Herman Miller’s chief sustainability engineer, greenhouse gas program manager, and lifecycle assessment leader. Since 2007, he has helped lead sustainable product design as part of Herman Miller’s Design for the Environment (DfE) team. Owen can be contacted via e-mail at thaddeus_owen@hermanmiller.com.