A comprehensive scrutiny of building enclosure design and construction
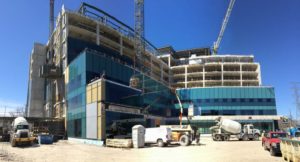
By Andrea Mucciarone, BSS
The building enclosure is the ‘skin’ of a structure and protects occupants from the exterior environment. The driving factors of enclosure design have evolved through the decades. Today, they include reducing carbon footprint, meeting greenhouse gas (GHG) emission targets, climate resiliency, and minimizing building energy use (aiming for net zero). Thus, there is a pressing need to design and construct thermally efficient, air- and water-tight, and durable building enclosures.
Although there is eagerness to address the factors listed above with new and innovative materials and construction techniques, building professionals may be putting the cart before the horse. Instead, it is better to focus on improving and implementing fundamental building envelope principles in the design, preconstruction, and build stages.
Design phase
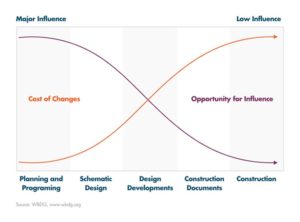
Image courtesy WBDG
Implementation of fundamental building science principles in the design phase is critical to the successful performance of the facility (Figure 1). It is highly recommended to engage a building envelope specialist at the schematic design stage to achieve the highest opportunity for influence on the project with the least impact on overall cost.
At this phase of the project, the design team/building envelope consultant is able to discuss and validate high-level ideas to establish buy-in with the client and help set realistic expectations. These meetings should determine building envelope objectives including the general plan for the control layers (i.e. air, water, thermal, and vapour barriers), R/U-value targets for the assemblies, the planned maintenance life cycles, and the building’s designed lifespan in accordance with the Canadian Standards Association (CSA) S478, Durability in Buildings, be relevant in these meetings.
Shop drawings
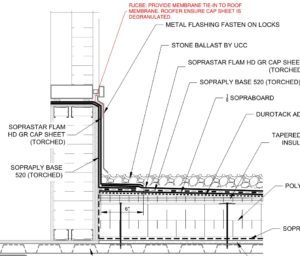
Images courtesy RJC Engineers
An enhanced review of building enclosure shop drawings is highly recommended, as they are critical documents. They can impact the overall performance of a building if insufficient and incorrect detailing is unaddressed at the review stage. For building envelope elements, such as light/medium-weight cladding on thermally broken framing or windows/curtain wall, it is recommended shop drawings be designed, reviewed, and stamped by a professional engineer for air/water performance along with structural. It is recommended shop drawings contain a comprehensive list of all materials being used for the project, and all components on the details are labelled and dimensioned.
Shop drawings should include and be checked for close co-ordination of adjacent trades so critical connections/interrelationships are thoroughly detailed, as these create most of the discontinuity failures on a building. For example, a roof shop drawing detail at a curtain wall curb may only show the roof membrane wrapping the curb and the curtain wall installed on top. However, the curtain wall subcontractor may be installing a membrane transition between the curtain wall and the granulated roof membrane. As such, in most cases, the roof membrane will need to be degranulated (i.e. heated and granules embedded in the bitumen) for the transition membrane to properly adhere to the roof membrane (Figure 2). If this transition is included in both trades’ shop drawings, it is less likely to be missed at the site where it will lead to discontinuity in the air and moisture barrier.