Prefabricated composite structures: The best of both worlds
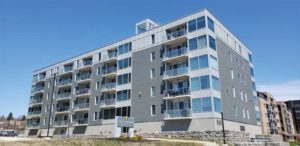
By Dominic Lemieux, P.Eng.
For the last decade, concrete and steel structures have been archrivals for multi-storey buildings requiring fire resistance. While cast-in-place concrete buildings offer an inherent fire resistance and slim floors, steel structures provide speed and precision due to their prefabricated nature.
Prefabricated composite structures allow designers and contractors to leverage the benefits of both concrete and steel to erect at a fast pace fire-resistant buildings with slim floors.
Project overview
The Luxenbourg phase II and III are multi-family residential projects located near downtown Québec City, Qué. The development comprises two identical buildings, each containing a total floor area of approximately 8000 m² (86,111 sf). There are 54 units in both buildings with five levels of residential and two levels of parking.
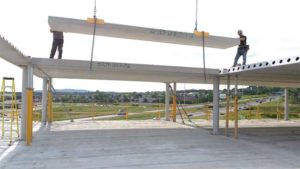
Challenges
The challenge for the developer was to find ways to reduce the construction schedule in order to enclose the building before winter, thus significantly lowering the impact of having to heat a poorly insulated building as well as snow removal during construction in the colder months.
Additionally, the site had a height restriction which meant a slim floor system had to be used to maximize the number of floors in the buildings.
Innovations
To solve the challenges, the developer and his team of professionals introduced a couple of innovations to make the project viable.
Innovation 1: Using a prefabricated slim-floor composite structure
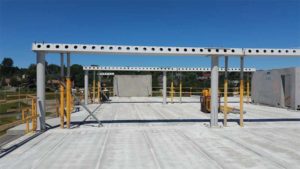
One of the objectives of the developer was to build a non-combustible structure that would be quick to install and would require as little manpower as possible. A combination of composite beams, composite columns, and hollow-core slabs were chosen to achieve the design solution.
The composite beams and columns are steel profiles containing shop-installed reinforcement. The profiles were later filled with concrete onsite to increase their strength and to provide fire resistance of two hours.
The precast hollow-core slabs also helped increase the speed of construction by minimizing the number of crane picks and by significantly reducing the amount of shoring required. Only two shoring posts per beam were needed during the erection which allowed for other trades to move in faster than with conventional cast-in-place construction. While the numerous shoring posts required for cast-in-place structures typically need to remain in place for weeks until the concrete cures, the few shoring posts utilized in a prefabricated structure are removed after just a few days since they are only required to stabilize the structure during erection. The faster the shoring posts can be removed, the faster other trades can get into the building.
The combination of hollow-core slabs and shallow trapezoidal composite beams created a floor assembly of only 250 mm (10 in.) while allowing for spans of over 11 m (35 ft). This compact floor assembly permitted the developer to maximize the number of floors he could build on this property.
Results obtained from using a prefabricated structure
Once the foundation walls had been poured, the five-man crew was able to erect a complete 1200-m² (12,917-sf) level every three to four days. The first day was used to install all the composite columns and the shallow trapezoidal composite beams. The second day was utilized to install the hollow-core slabs and the third day was used to grout the composite columns, the shallow trapezoidal composite beams, and all the joints between the hollow-core slabs. On the fourth day, the cycle could be started over on the level above. After 20 working days, the crew topped off the five floors of residential levels. The five-man crew consisted of one crane operator and four steel erectors.