Crystalline waterproofing and protection for concrete
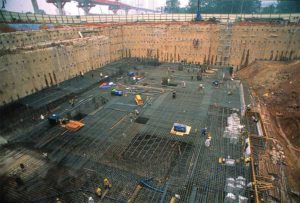
Images courtesy Xypex Chemical Corp.
By Dave Ross
Concrete has been used for thousands of years and is the most widely used building material in the world. According to the Cement Association of Canada (CAC), more than twice as much concrete is used in construction around the world than the total of all other building materials, including wood, steel, plastic, and aluminum.
Yet, despite its apparent solidity, strength, and durability, concrete is porous and permeable to fluid and vapour infiltration and migration. Water and dissolved chemicals, such as chlorides, sulfates, and acids, can penetrate deep into concrete, sometimes resulting in premature damage, such as reinforcing steel corrosion, freeze/thaw cracking, spalling, and chemical attack.
Added to this ‘natural’ porosity is the fact newly poured concrete develops cracks. This can be due to excess water, rapid drying, improper strength, settlement, and shrinkage. When it comes to building foundations, elevator pits, water/wastewater treatment and water containment structures, and many other applications, waterproofing and protecting the concrete is critical.
The porous and permeable nature of concrete
Concrete is a mixture of rock, sand, cement, and water. Rock and sand form the aggregate base of the concrete. The mixture of cement and water provides a paste, which binds the aggregates together. As the cement particles hydrate and form calcium silicate hydrates, the whole mixture hardens into a solid, rock-like mass.
To make this mixture workable, easy-to-place, and consolidate, more water than necessary is used to hydrate the cement. This extra water, known as the water of convenience, bleeds out of the concrete, leaving behind pores and capillary tracts.
Despite the use of admixtures to reduce the amount of water in the mix, pores, voids, and capillary paths form in the concrete. They carry water and aggressive chemicals that corrode steel reinforcement and deteriorate the concrete, thus jeopardizing the structure’s integrity.
Porosity is the amount of holes or voids left in concrete, expressed as a percentage of the total volume of a material. Since it is porous, concrete is also permeable.
Permeability—a broader term than porosity—is an expression of how well the voids are connected, providing the ability of water to flow through a material. Together, these pathways allow the movement of water into and through the concrete. Permeability is described by a quantity known as the ‘permeability co-efficient,’ also called Darcy’s Co-efficient. The water permeability of concrete is a good indicator of its quality and durability. The lower the permeability co-efficient, the more impervious the concrete and the higher its quality and performance. Nevertheless, concrete with low permeability may still need a waterproofing agent to seal micro-cracks.
Vapour flow in concrete structures
Water can also migrate through concrete in the form of vapour. The flow travels from high vapour pressure, generally the source, to low vapour pressure by a process of diffusion and can vary based on environmental conditions.
Vapour flow direction is critical when applying a waterproofing treatment in situations where an unbalanced vapour pressure gradient exists. Some typical examples of this are as follows:
- applying a low vapour permeable membrane, such as a traffic deck coating over a damp concrete surface (even if the very top surface is dry) on a warm day results in the buildup of vapor pressure and pin-holing or blistering;
- adding a coating or sealant to the outside of a building wall may trap moisture if the sealant is not sufficiently vapour permeable; and
- installing low vapour permeable flooring over a slab-on-grade with high subsurface moisture content may result in delamination.
As a general rule, a coating with low vapour permeability should not be placed on the downstream face (negative or dry side). Either vapour or water pressure will ‘push’ the coating from the surface, causing it to blister. Some types of coatings (e.g. cement-based ones) and water permeability-reducing admixtures accommodate considerable vapour movement, thus allowing them to be placed successfully on the downstream side.
How crystalline waterproofing works
Crystalline waterproofing technology improves the waterproofing and durability of concrete by filling and plugging pores, capillaries, and micro-cracks with an insoluble, highly resistant crystalline formation. The process is based on two simple properties—one chemical and the other physical.
Concrete is chemical in nature. When a cement particle hydrates there is a reaction between water and the cement, which causes it to become a hard, solid mass, but there are also chemical byproducts given off that lay dormant in the concrete.
Crystalline waterproofing introduces a second set of chemicals. When these two groups are brought together (i.e. the byproducts of cement hydration and the crystalline chemicals) in the presence of moisture, a reaction takes place, resulting in the formation of an insoluble crystalline structure.