Carbon sequestration in cement enhances concrete construction
By Nancy Novak
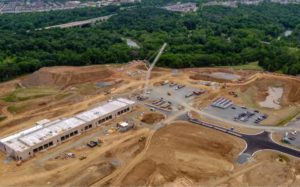
When the topic of buildings and carbon emissions come up, most people think of climate control, minimizing power usage, and sourcing renewable electricity—all of these are important ways to do better by the environment. Operations are the major source of sustained, long-term emissions, and the primary focus of Canada’s Climate Action Plan as it relates to the commercial building sector. However, there is an opportunity to improve the environmental impact of buildings from the ground up.
Buildings are the third largest source of greenhouse gas (GHG) emissions in the country, followed by the oil and gas and transportation sectors. They account for approximately one-third of the country’s GHG emissions. Across the globe, buildings and construction are responsible for 39 per cent of all carbon emissions. Eleven per cent of that is upfront carbon associated with construction, or embodied emissions.
Cement, the key component of concrete and the foundation of all formidable structures, is the primary source of embodied emissions. Cement generates around seven per cent of global carbon emissions. Every year, manufacturing cement emits more than two billion tons of carbon dioxide (CO2) in the process of firing massive kilns, which require large amounts of energy and produce high volumes of CO2.
For years, the construction industry has focused on operational opportunities to reduce the carbon impact of commercial buildings. Strides have been made to reduce volatile organic compounds (VOCs), creating safer environments for workers and occupants. There is a heightened awareness of transportation-related impacts on the environment and efforts have been made to source materials closer to the site. These are all important steps to protect the environment.
From a construction standpoint though, solutions to reduce the carbon intensity of new builds have been limited. Recycled steel and concrete fillers have driven some reduction in embodied carbon in new construction, but not made meaningful impacts.
Carbon sequestration technology
There is a real and effective opportunity to offset the negative environmental impacts of cement production with new technology that makes it possible to sequester carbon in cement. The technology focuses on converting CO2 into a mineral and uses CO2 in concrete to help manufacturers respond to the demand for green building products.
Using such technology, concrete producers mineralize carbon waste and inject it into concrete. The CO₂ is sourced from industrial emitters. They collect, purify, and distribute the CO₂ to concrete plants, which store it in pressurized tanks until it is ready to use.
Once injected into the wet concrete mix, the CO₂ reacts with calcium ions from cement to form a nano-sized mineral, calcium carbonate, which then becomes embedded in the concrete. This makes the concrete stronger. Aside from increased strength, CO₂ does not impact the concrete properties. Set-time, slump, workability, pumpability, air content, temperature, and finishing are unaffected; neither are hardened properties, including pH, freeze-thaw, density, colour, texture, and durability.
In addition to improving compression strength, mineralized CO2 reduces the volume of cement used in concrete. Most importantly, it permanently eliminates CO2 from the atmosphere, offsetting negative impacts of cement production on the environment.
For a measure of environmental impact by application…
- ready mix saves 11 kg (25 lb) of CO₂ per cubic yard;
- precast saves 11 to 18 kg (40 lb) of CO₂ per cubic yard; and
- masonry saves 0.5 kg (1 lb) of CO₂ sequestered per 30 standard blocks.
Solution applied
Compass Datacenters, a data centre construction company, recently learned of the carbon sequestration technology and committed to using it in the production of concrete for its new data centres, which rely heavily on concrete.
The number of data centres worldwide has grown from 500,000 in 2012 to more than eight million today. Expansion is likely to continue on that trajectory as more people work, learn, shop, and stream entertainment from home in the wake of COVID-19. A lot of that expansion will be new construction in key markets, such as Toronto, Montréal, and Vancouver.