Design of concrete for moisture-sensitive floorcoverings
by Paul Potts
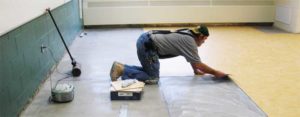
It takes three to six months for concrete to dry to 70 to75 per cent relative humidity (RH), a safe level to place moisture-sensitive floorcoverings and adhesives. The drying duration, a critical factor in the overall schedule, is directly affected by the concrete mix design, the capillary break and vapour barrier, and curing methods. There are several parties, such as architect/engineer, construction manager, concrete contractor, batch-plant operator, soils/materials testing agency, and floorcovering contractor, each with contractual duties that will affect the successful installation of the floorcovering. While each party has separate duties, no single entity has overall responsibility for the entire process (The term construction manager in this article refers to both construction manager and general contractor (GC). The word architect or architect-engineer refers to both architect and engineer individually. Floorcovering refers to moisture-sensitive floor coverings and adhesives.).
Preconstruction meeting
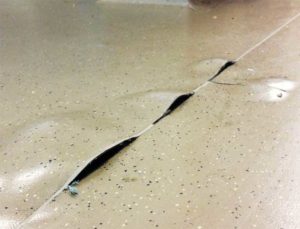
Photo courtesy Chris Maskell
The preconstruction meeting is the opportunity to establish a collaborative working group. The leaders of the meeting (architect/engineer and construction manager) should describe the special challenges of placing concrete for moisture-sensitive floorcovering and reinforce the necessity of each party performing their duties with care. The architect/engineer must play a central role at the meeting because they have the greatest authority to discuss the design and construction documents.
Requirements to be discussed at the meeting include:
- the objectives of the low water mix design and why it is important to not add water to the concrete at the jobsite;
- slump tests should be performed before plasticizers or water reducers are added to the concrete;
- the contractor or construction manager must notify the testing agency 24 hours in advance of concrete placement;
- patterns of nonconforming test results should be reported to the architect and construction manager as soon as possible;
- discussion on documents incorporated by reference and what to do if conflicts are discovered;
- if bleed water appears on the surface, one must stop the finishing work until the water evaporates; and
- do not hard trowel concrete slab surfaces for moisture-sensitive floorcovering because it closes the pores and seals moisture in the concrete prolonging drying time.
The batch-plant operator must also be at the meeting. They must be informed that allowing a driver to add water to the concrete at the site, unless approved by the owner or architect/engineer, could result in the material being sent back to the plant. They should also be reminded to make sure trucks returning from the site are emptied of leftover mix or rinse water.
Design and construction objectives
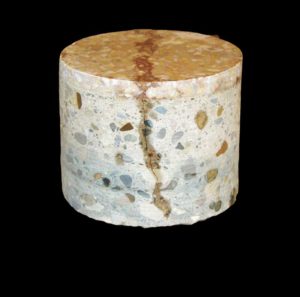
Photos © Paul Potts
The principle objectives in planning concrete to receive moisture-sensitive floorcovering are (see the American Concrete Institute’s [ACI’s] 302.1R-06, Guide for Concrete Floor and Slab Construction):
- design concrete with low water-cement ratio (w/c);
- add welded wire reinforcement (WWR) to minimize random cracking;
- grade the subgrade slab before placing the capillary break aggregate;
- construct a capillary break of coarse aggregate and rake the aggregate before placing the vapour barrier;
- provide a vapour barrier over the capillary break, directly under the concrete;
- manage curing with the intent to minimize drying duration; and
- provide adequate time in the schedule for the concrete to dry satisfactorily (American Concrete Institute [ACI] guide for concrete slabs that receive moisture-sensitive flooring materials.).
Mix design
According to the Portland Cement Association (PCA), “all desirable properties of concrete are improved by reducing the total water content to the practical minimum.” A low w/c ratio mix design reduces the delay required to bring the RH of the slab to a safe level to apply the floorcovering and also result in flatter concrete surfaces with less curling and long-term shrink cracking.
The w/c ratio, size, and quantity of coarse aggregate and cement content could affect the total water content. If properly selected, each requirement will result in minimizing the total water content. The w/c ratio is the most important factor when determining the drying rate of a concrete slab. The lower the ratio the faster concrete dries. A plasticizer may be needed to reduce placement difficulties.