Building successful indoor cannabis cultivation facilities
By James Lowe and Benjamin Franz
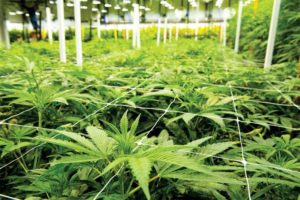
Indoor controlled cannabis production is a rapidly growing business segment, with many industry specific aspects to facility design. Although many design elements can draw upon parameters from similar industries, some operational aspects remain unique to cannabis production facilities.
Cannabis cultivation has several elements and activities that must be taken into consideration including:
- landscaping;
- mechanical and electrical equipment placement;
- carbon dioxide (CO2) tank placement;
- parking; and
- shipping and receiving operations.
Landscaping around the exterior of the building is an often-overlooked aspect of facility design, but it can have economic consequences. When selecting plants for the exterior of the building, it is important to avoid species capable of harbouring pests and diseases common to cannabis facilities. Certain plants can act as a reservoir for the continued introduction of these organisms into the facility, resulting in losses to yield and increased costs for pest and disease control. The best practice is to place plants away from any entrances or paths where employees or maintenance staff members access the building to avoid human-mediated transfer of pests and diseases into the facility as much as possible.
Harmful pests to watch for include the two-spotted spider mite, cyclamen mites, rice root aphids, and thrips. Common disease organisms include botrytis, sclerotinia, powdery mildew, verticillium wilt, fusarium, and pythium.
Equipment considerations
Mechanical and electrical equipment for indoor cannabis facilities uses up to 100 watts per square foot (depending on technology selection and space capture), which rivals the amount of energy a data server room requires—between 100 and 200 watts per square foot (For information, read “Data Center Density Hits the Wall” by Robert L. Mitchell in the January 2010 issue of Computerworld.). Further, it takes more than 23 t (25 tons) of cooling and dehumidification equipment to service a 93-m2 (1000-sf) cultivation room.
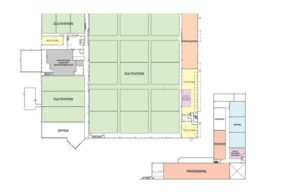
Image courtesy GrowForce Holdings Inc.
Although it is preferable to locate this equipment on the roof, many buildings may not be able to accommodate the weight, which is why it often ends up screened on the ground near the rooms it is serving to minimize
outside ducting.
When building from the ground up, a structural engineer will ensure the building is able to bear the weight of the large and heavy mechanical and electrical equipment that heats and cools the space. Some pre-engineered buildings being retrofitted for indoor cannabis cultivation are not designed to handle the weight of the equipment, so this can be an important consideration when selecting a structure.
To increase yield in cultivation rooms, CO2 is used to enrich the atmosphere. The CO2 must be stored in tanks located on the outside of the building, ideally as close as possible to the cultivation rooms to minimize piping, but also in a location accessible by a large truck. Keep in mind bollards are typically required near the tanks.
CO2 use varies based on operating procedures, mechanical systems, and room construction. While the plants in the room consume some of the CO2, usage is mainly driven by CO2 escaping the room. A good rule of thumb for CO2 usage is 45 to 91 g (0.1 to 0.2 lb) of CO2 per square foot of cultivation room, per month. The tank(s) should be sized so the local CO2 supplier can refill them without any supply interruptions. Often, the CO2 suppliers provide the tank and help with sizing.
Building considerations
Cannabis facilities are often mapped out based on operational activities to reduce the potential for cross-contamination between spaces, and improve supply flow within the facility from the shipping area. Separate areas are created for activities such as cultivation, processing, and fertigation (the application of water, fertilizers, and other agrochemicals through an irrigation system utilizing injectors). Due to the value of cannabis, it is important to have a secure shipping area when moving product offsite.
Microbial growth can be prevented and mitigated within the walls of a cannabis cultivation facility by insulating the exterior walls and ventilating the interstitial spaces. In the authors’ experience, the envelope of the building should be insulated to a high R-value per inch and incorporate a vapour barrier to prevent moisture penetration and condensation from forming inside.
In terms of internal layout in a new building, columns should be hidden in walls as much as possible to avoid the loss of cultivation space. When a building is being repurposed for cannabis cultivation, this becomes a design challenge. For example, GrowForce is retrofitting what was previously a meat-packing warehouse in Winnipeg into an 11, 148-m2 (120,000-sf) cannabis production facility compliant with the Access to Cannabis for Medical Purposes Regulations (ACMPR). The existing columns were used to help dictate where the walls would go. Whenever possible, the walls were placed along column lines to minimize the loss of space due to columns.