Montréal landmark receives copper restoration
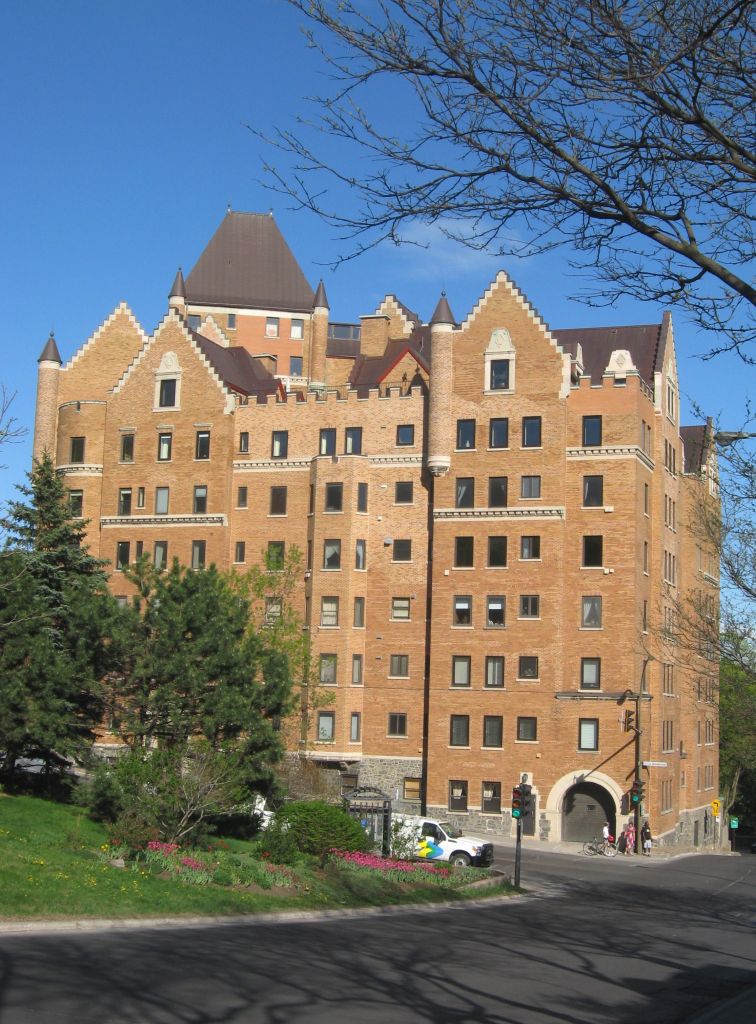
By Stephen Knapp
When first constructed in 1931, Trafalgar Condominium Apartments in Montréal had a significant presence along the city’s downtown skyline. Reaching 10 storeys, the numerous turrets, chimneys, and gable front dormers atop the brick building’s steep-pitched copper roof gave the residence an imperial appearance—similar to a medieval castle dating back to the turn of the century.
Over the years, the architectural features continued to make the building stand out against the newer, more modern structures of the 21st century—specifically near the popular Mount Royal Park. These include both historic and contemporary copper roofing and cladding applications, which are a common feature for many of Montréal’s most prestigious buildings. However, the three-tower building complex began to age with time, leading to the deterioration of the building’s façade and failure of its copper roof.
Discovering deterioration
Harsh winters, combined with exposure to the elements year after year, had compromised the roof, causing a loss of thickness due to oxidation over time, and required regular patching, caulking, and soldering to joints. In particular, ice storms hit Montréal during the winter of 1997 and caused some of the batten-seam panels to become deformed, as well as left punch points in the copper roof measuring as large as 13 mm (1/2 in.). As a result, sections of the roof had to be replaced, including a group of vertical panels and the horizontal apron at the bottom of the pitched roof.
Additional flashing at the valley and ridge had to be installed where leaks had occurred. An inspection of the 80-year-old copper roof system had revealed it was nearing the end of its life, and needed to be replaced.
To preserve the building and ensure the safety of its residents, a major restoration project began in the spring of 2008, and was completed in three phases. The $7 million-project consisted of two major components: repairing the brick envelope and architectural stone (masonry work), and replacing the existing copper roof, said Daniel Durand, project manager and principal architect of DFS Inc., Architecture and Design.
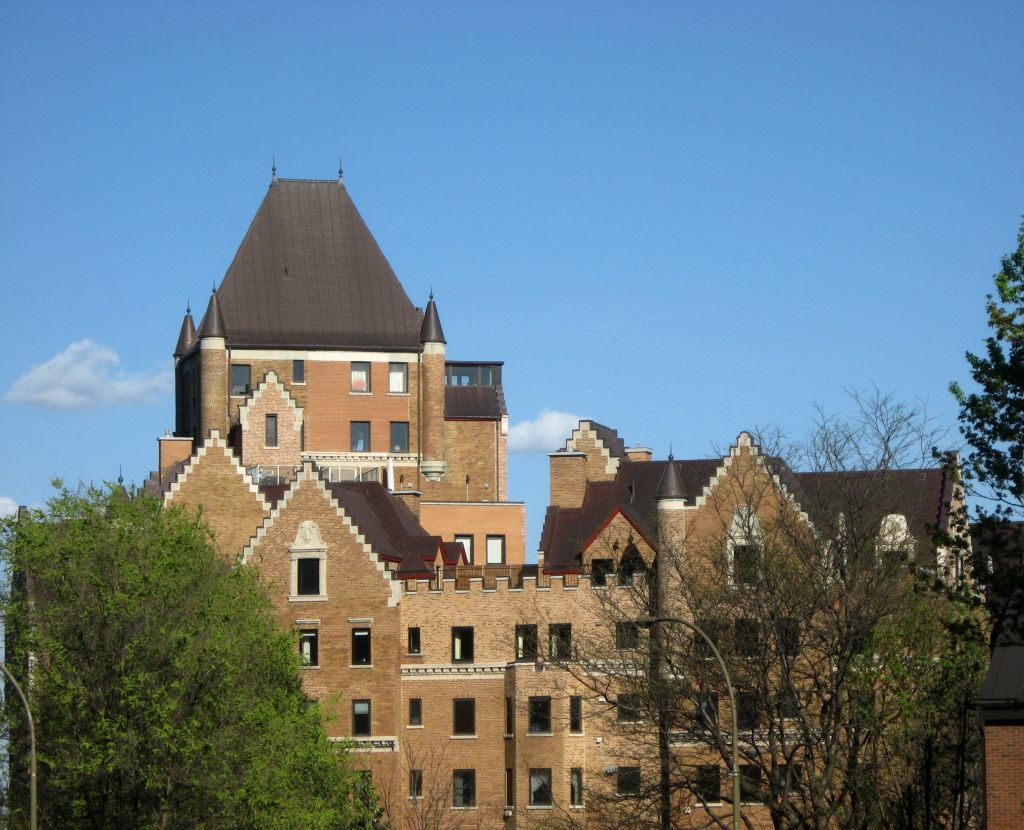
“By doing the restoration work at the same time as the repairs, we not only upgraded the construction, but also improved the energy efficiency of the building,” he explained.
By replacing the copper roof, the design team was able to take a closer look at the entire wood decking and inspect it carefully for damage. It was then it became possible to introduce proper insulation and install a vapour barrier and air membrane to secure the roof.
Original design
The Trafalgar building is a national historic landmark designed by well-known architects Hutchinson & Wood—under lead developer and constructor Joseph Gersovitz, grandfather of acclaimed Montréal architect Julia Gersovitz. Once one- and two-storey rental units, the apartments were converted into upscale condominiums in 1975. While renovations were made to the units, the building’s exterior remained intact. The 57-unit complex comprises an assembly of three major blocks, with some of the larger and more luxurious units located on the upper floors. With a mix of private roof terraces and common areas, residents now enjoy panoramic views of the city.
As a historical landmark, the Trafalgar building’s roofing had to be restored to its original form using a copper batten-seam roof system, as well as other unique copper details and features. Copper is used for various building projects—from wall cladding and roofing to ornamental designs—and the contractors had no concerns when it came to working with the age-old metal.
Copper not only delivered the desired esthetic, but it also provided durability, longevity, and sustainability. The flexibility and malleability of copper makes it an easy material to form over irregular roof structures. Domes and other curved roof shapes are readily handled with copper.
The original copper roof of the Trafalgar lasted for more than 50 years with relatively no major problems or issues. Copper had demonstrated its durability and appropriateness for the roof shape and detail. The material has shown it can be soldered in difficult corners and angles, which is not easy with pre-painted steel or aluminum or galvanized roofing systems.
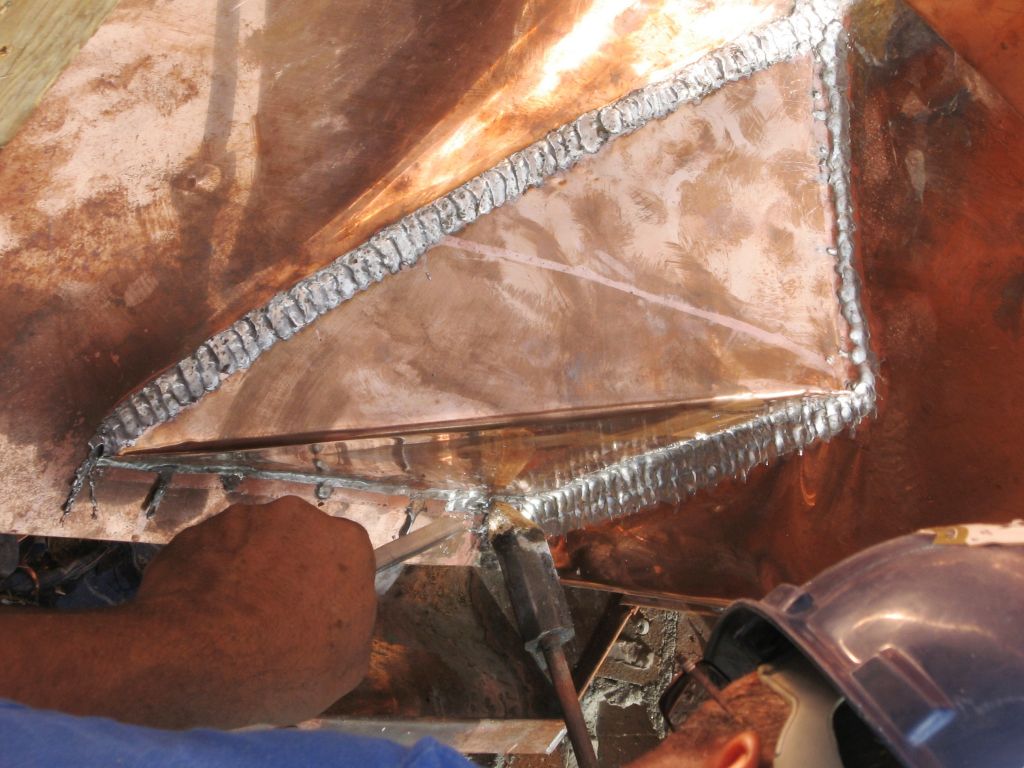
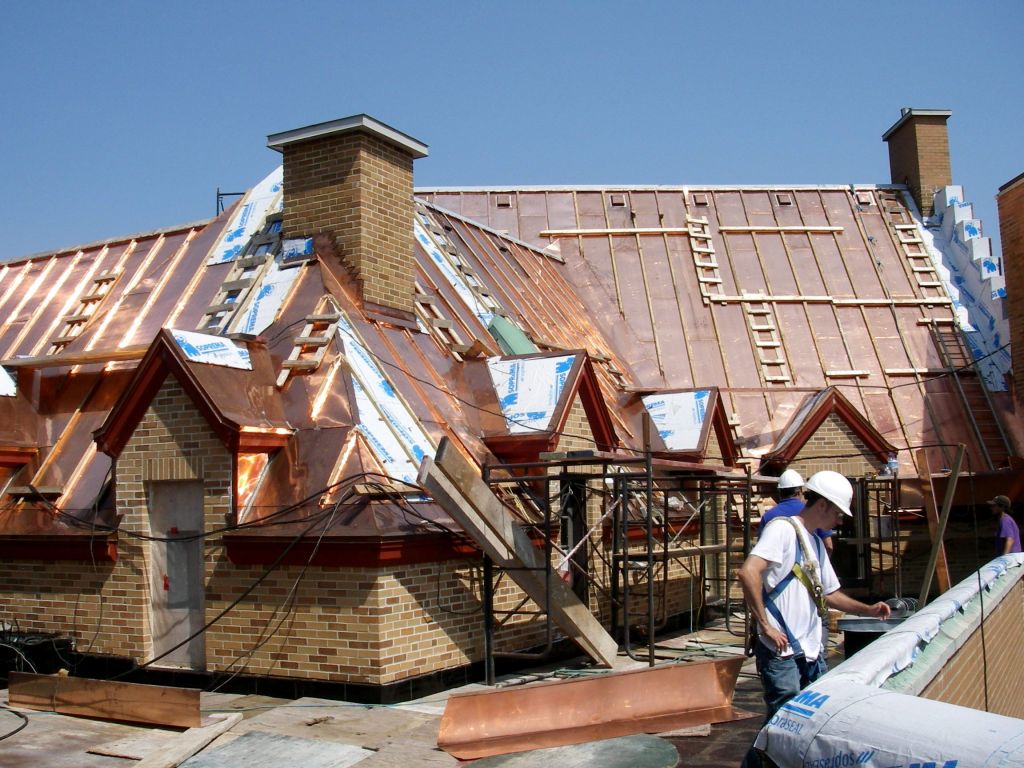
Copper oxidation also provides a self-protection to the metal. This surface oxidation allows the roof to maintain a uniform colour appearance throughout the life of the system. Due to its ductility, copper reacts well to temperature change, allowing the roof to retract and expand as needed.
Many cities in Eastern Canada (and in Québec particularly) are dotted with examples of this. For centuries, copper has been the material of choice for important public buildings, churches, universities, and residential structures like the Trafalgar building. Older buildings, and especially larger ones, were covered with metal roofs, commonly tin. When it came to institutional buildings, train stations, hotels, or large civic buildings, copper was preferred because of its unique look and durability. In modern times, other kinds of distinctive metals such as zinc, inox, or lead, are used.
Standard conformance
Conforming to current energy codes and standards meant the new roofing system had to be insulated in order to ensure proper waterproofing for the building. Besides saving energy, insulation protects the copper roof by allowing it to maintain a cold temperature (i.e. less heat conduction through the roof) during winter months. This prevents snow from freezing, causing ice dams to form on the roof and potentially damage joints.
For example, in Québec, the design team had to comply with Construction Safety Code, Chapter E-1.1, “Regulation Respecting Energy Conservation in New Buildings.” In newer buildings similar to the Trafalgar, the requirement for roof thermal resistance is RSI 2.9 (R-18). The typical new roof composition provides a thermal resistance of RSI 5.3 (R-30), which is the standard for an individual residential home.
For this purpose, a 3530-m2 (38,000-sf) batten-seam copper roof system was designed and installed, with careful attention paid to numerous special details in the intersections gables and turrets intersections, and crenulated wall copings.
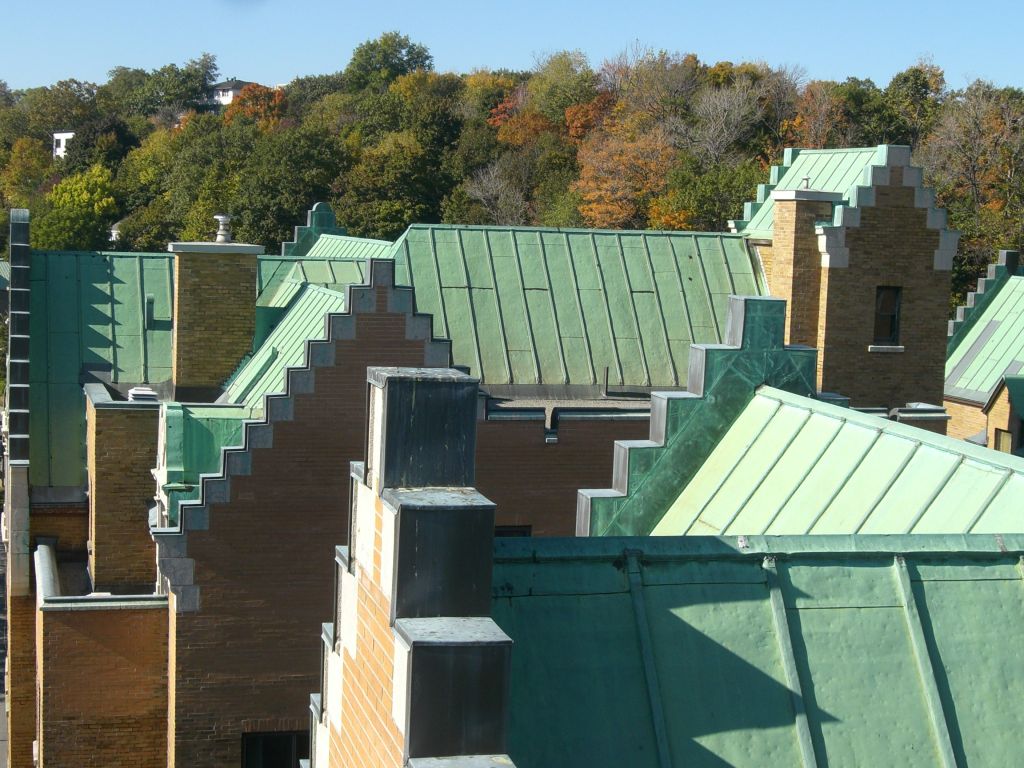
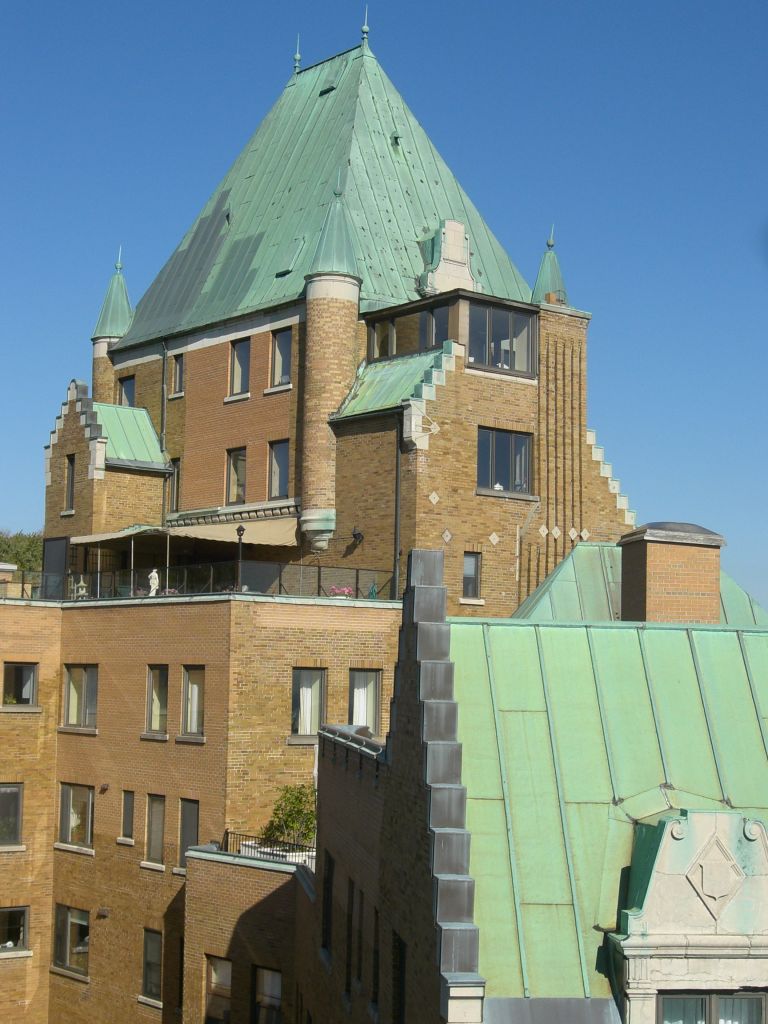
Some of the decorative features include:
- main tower with its steep-pitched roof;
- four intricate volumes with complex angular junctions;
- needle point with the bulb under (nine units);
- four large masonry dormers that have gable and curve surfaces at the base of the main tower roof;
- several medium-sized dormers with artificial stone gables at the base of the lower volume—some of the roof surface is curved while others sections contain a multi-angular slope;
- main-wall gable along the street façade required a lot of folding and solder details;
- seven turrets required good dimensioning of panel and several in particular needed to be cut to fit exactly with roof surface and circular masonry of the turrets;
- chimneys in complex corners;
- curved form of parapet wall and more complicated assembly at the opening of crenellations.
During the restoration, repairs were made to the wood structure where condensation and infiltration had caused damage to the roof assembly. Some of the planks were replaced, and new plywood was laid down in certain areas. Once the existing copper roofing, gutters, and downspouts were removed and recycled, the new roof was installed. It should be noted new copper sheet is produced in many cases from 100 per cent recycled content, especially when sourced from mills in North America.
For Trafalgar, some of the copper pieces in good shape were salvaged and reused elsewhere on other projects. This included parts of the gutter, downspout, and copper panel systems. However, in general, most of the copper removed was sent to the recycling centre.
The new roofing system consists of:
- modified bituminous (mod-bit) vapour barrier;
- foil-faced polyisocyanurate (polyiso) insulation;
- plywood sheathing;
- an underlayment system; and
- 453-g (16-oz)—or ‘Calibre 28’—copper batten-seam panels.
All these elements contain custom details as required by numerous and varied site conditions, such as the transition between the concrete and wood structure, dormer configuration, and fire separation stopping and partition.
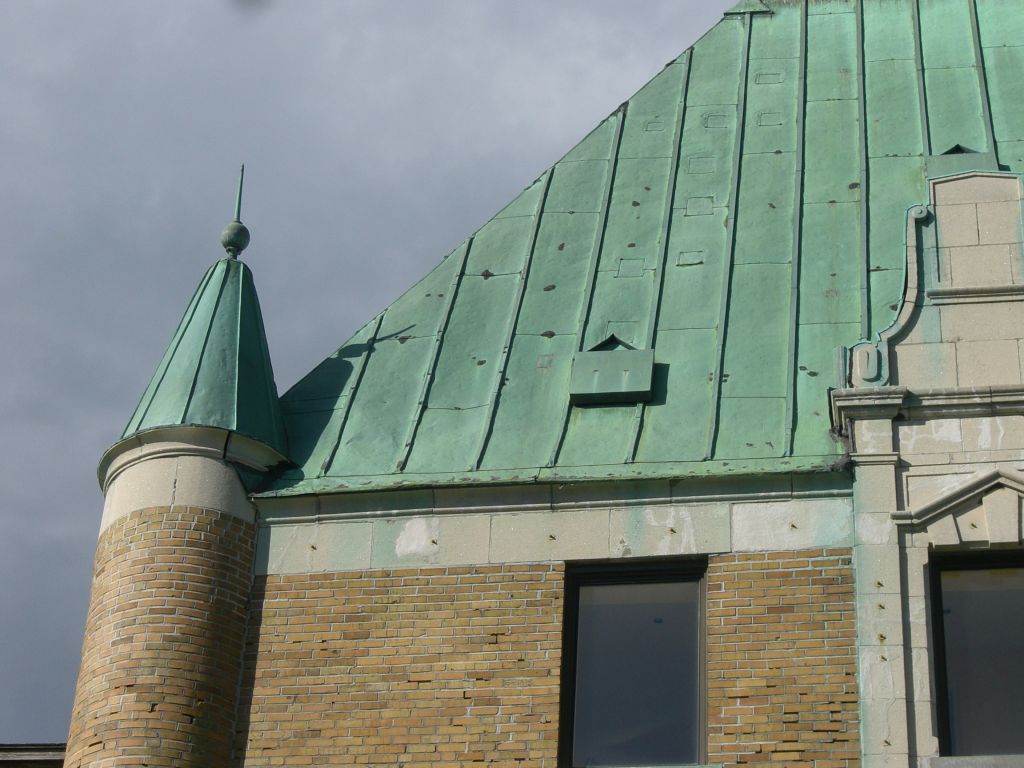
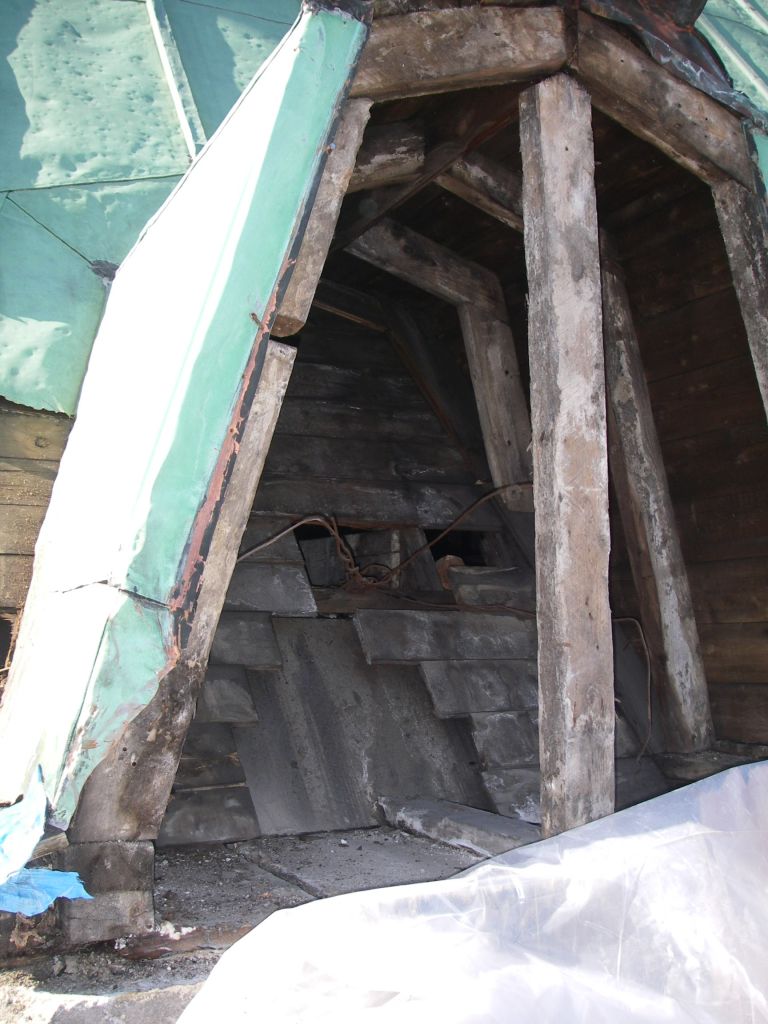
Mockups of copper gutters, architectural decorative elements, and roof turrets were prepared and tested onsite before final installation. Specifically, the contractor created mockups for the large gutter system being installed at the main tower’s base, the turret’s reconstruction (i.e. structure and copper installation), the water deviator aside from the gable wall, and for the co-ordination of the batten-seam connection at the ridge.
Like any roofing system of this size and historic significance, there were challenges. The roofers not only wanted to replicate the original detail and design of the copper roof system, but also improve on them to extend the life and ensure issues do not arise in the future.
The three-year restoration project earned the sheet metal contractor and the architectural firm a North American Copper in Architecture Award (NACIA) from the copper industry. The Trafalgar was one of 14 building projects to be selected for an award by the Canadian Copper & Brass Development Association (CCBDA) and Copper Development Association (CDA) this year.
Conclusion
Copper is no stranger to Montréal’s architectural landscape. It has been used in many structures throughout the city, including hotels, churches, and government office buildings. The copper roof of the historic Trafalgar Condominium Apartments was restored, once again returning this upscale residential complex in the heart of Montréal to its original beauty while extending its life in the process.
Stephen Knapp is the executive director of the Canadian Copper & Brass Development Association (CCBDA). He is responsible for guiding market development and promotional efforts for various applications of copper and copper alloys including tube and plumbing, electrical, renewable energy systems, energy-efficient technologies, and architectural applications. Knapp holds a bachelor’s degree in architectural science from Ryerson Polytechnical Institute in Toronto, and a master’s degree in architecture from Texas A&M University in College Station, Texas. He can be contacted at stephen.knapp@copperalliance.ca.