Mid-rise wood-frame construction gets innovative
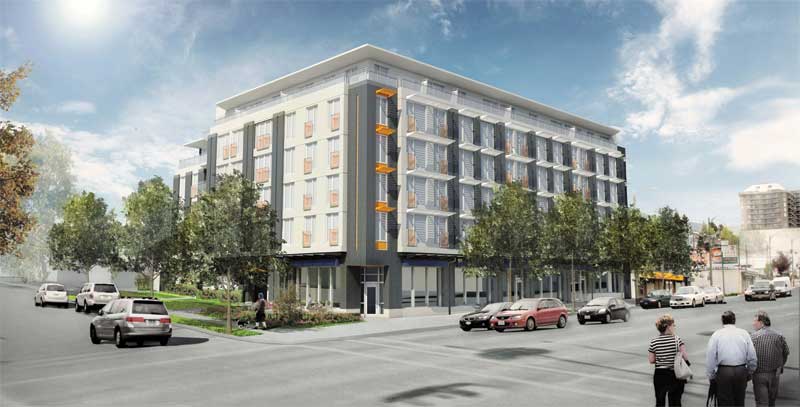
By Jim Taggart, FRAIC
In the nine years since the British Columbia Building Code (BCBC) was revised to permit six-storey residential wood construction, architects, engineers, municipal authorities, and local fire departments have become familiar with the basic parameters of this new building type. Over the same period, market conditions and technological advances in wood products and building systems have continued to evolve, creating new challenges and opportunities.
There is an increasing interest in ultra-low energy buildings that comply with the Passive House standard, along with a growing need to explore new approaches to project delivery, particularly when building on constricted infill lots. There is also a desire to explore hybrid wood construction in anticipation of impending code changes that will permit six-storey wood construction for some Group D occupancies.
This article looks at three six-storey wood-frame projects in the Vancouver area that are addressing these emerging changes on the country’s urban development landscape. (The full case study titled Mid-rise 2.0: Innovative Approaches to Mid-rise Wood Frame Construction is now available online. Visit wood-works.ca/bc/case-studies-videos.)
The Heights
Scheduled for completion in early 2018, The Heights (shown above), owned by 8th Avenue Properties, is a mixed-use residential building, with a basement parking garage and ground-level commercial space constructed in concrete, and five storeys of light wood-frame apartments above.
The project was rezoned from its existing C-2 commercial zoning under the City of Vancouver ‘Rental 100’ program, which offers incentives to new projects undertaking to provide rental accommodation for a minimum of 60 years. Since this arrangement means the developer is responsible for long-term operating costs, it makes low-energy solutions particularly attractive.
With this in mind, Scott Kennedy of Cornerstone Architecture proposed that the project pursue Passive House certification. Among some of the most important strategies for Passive House buildings are:
- the correct orientation, sizing, and shading of windows to optimize passive solar heating;
- super-insulated building envelope with minimal thermal bridging;
- airtightness to reduce heat loss through air leakage;
- reduction of ventilation rates to maintain healthy indoor air quality (IAQ); and
- recapture of heat from exhaust air using heat recovery ventilation.
The cumulative effect of these strategies is to reduce the building’s energy demand to such an extent internal sources provide much of the energy required for heating, and conventional mechanical systems can be smaller than in traditionally designed buildings.
Kennedy wanted to prove a Passive House building could be constructed using traditional methods, and worked with Doug Wilson of Peak Construction to develop details that would minimize uncertainty, risk, and additional cost.
First, he had to convince his client the Passive House approach made sense from a business perspective. Kennedy argued a conventional hydronic heating system would have a capital cost of approximately $450,000 and maintenance and repairs over the 60-year life of the building had a net present value of $150,000. If this money could instead be spent on a superior building envelope, hydronic heat could be replaced with cheaper electric baseboards, and the net cost would be the same. The advantage would accrue to the developer in the form of greatly reduced operating costs.
Cornerstone designed the building with a conventional nominal 50 x 152-mm (2 x 6-in.) wood stud exterior wall, sheathed in plywood and supporting a rainscreen system of brick veneer. These walls contain no services—such components are contained within a secondary service wall—facilitating the installation of insulation.
Inboard of the 50 x 152-mm exterior wall, and separated from it by a 50-mm (2-in.) gap, is a secondary nominal
50 x 101-mm (2 x 4-in.) wood-stud service wall. These were built after installation of a 50-mm expanded polystyrene rigid insulation on the interior face of the exterior wall. The rigid insulation was factory finished with a polymer coating and acts as both a vapour and air barrier when appropriately sealed. Sealing takes the form of proprietary tapes at joints, and caulking where necessary.
The specified slider id does not exist.
The expanded polystyrene air barrier is sealed to theplywood floor, which extends out to the exterior face of the 20 x 152-mm wall, then wrapped around the floor joists and back to the top of the inner wall on the next level down (Figures 1 and 2). To ensure this detail and others relating to the airtightness of the building were executed correctly, two members of the contractor’s crew were trained in Passive House construction at the nearby British Columbia Institute of Technology (BCIT).
To eliminate thermal bridging, sunshades and balconies are hung off the 20 x 152-mm exterior wall—the fasteners neither penetrate the insulation nor puncture the air barrier (Figure 3). The interior service wall is also insulated (i.e. the vapour barrier is in the centre of the wall), and the drying out of any moisture that might become trapped within the wall happens to either the interior or exterior, depending on where it occurs. The wall assembly’s performance was verified using simulation software.
The careful attention to detailing and sealing for airtightness has resulted in a building envelope in which thermal bridging has been eliminated (Figure 4). In this way, The Heights has confirmed traditional wood-frame construction techniques can successfully be applied to the new generation of high-performance buildings.