Enabling faster returns to service when installing flooring
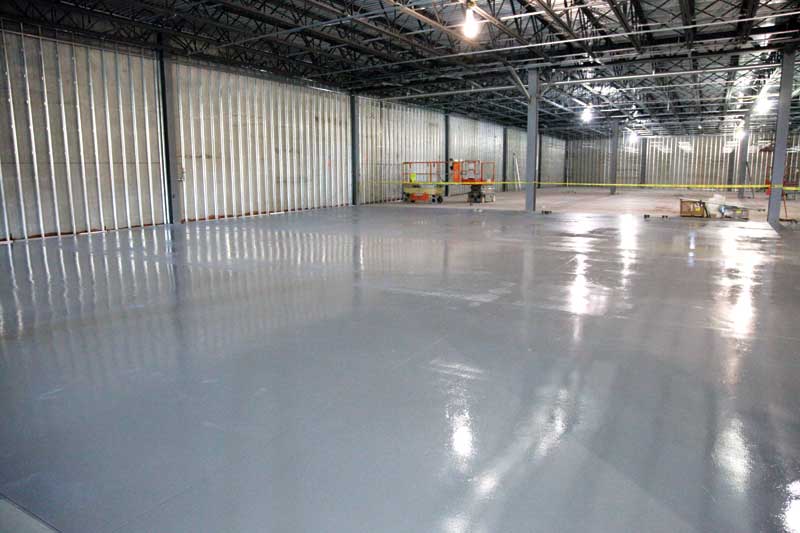
By Casey Ball
Whether building a new facility or retrofitting an existing one, downtime can be a construction manager’s worst nightmare. It can interfere with the project’s overall productivity, creating delays that hold up multiple service providers from performing their duties.
Unfortunately, when the time comes to install or repair a resinous flooring system, downtime is a given for nearly every discipline involved. However, unnecessary delays can be prevented by knowing more about the different types of flooring and their limitations, allowing design/construction professionals to select the system best aligning with the project timeline, budget, and longevity requirements.
To avoid contaminating a new resinous flooring system, other construction activities must often stop, and personnel must clear the area throughout the multistep—often multiday—installation. The applicator’s goal is to then return the facility to service as quickly as possible following the flooring installation. To speed up installations and minimize project downtime, it is best to select flooring systems that apply and cure quickly. Such products include urethane concrete coatings, which can allow foot traffic within four to eight hours of application and full service within six to 12 hours.
Additionally, methyl methacrylate (MMA) systems allow foot traffic after one hour and full service in two hours, with the caveat they typically require additional project setup time to mitigate odours. Conventional epoxy mortar systems are another common alternative, but they typically need a 24-hour curing time before returning to service. The three systems also differ in their number of application steps and total installation times, with urethane and MMA systems offering enhanced efficiencies.
Evaluating resinous flooring system options
For commercial facilities, there are three commonly used flooring system chemistries.
Epoxy mortar systems
These cost-effective, medium- to heavy-durability floor coatings can be applied at thicknesses from less than 40 mils (1016 µm) to 9.5 mm (3/8 in.). While quick to install, these systems are slow to cure. They have good chemical resistance, but low abrasion resistance, which can lead to wear patterns in high-traffic areas.
MMA systems
MMAs tend to offer the fastest option for flooring installations by installing and curing rapidly. However, that high speed comes with a price premium. MMAs also have a strong odour, which often necessitates the installation of mitigation systems during application, adding to project timelines. The systems have excellent weathering resistance, allowing them to be used for exterior applications.
Urethane concrete systems
Self-levelling slurry or mortar urethane systems offer fast installation turnaround times due to their rapid curing and moisture tolerance properties. They have high resilience against moisture vapour emissions (MVEs), allowing them to be applied to green (i.e. new) concrete. They can be returned to service 12 hours after topcoating and have excellent chemical resistance.
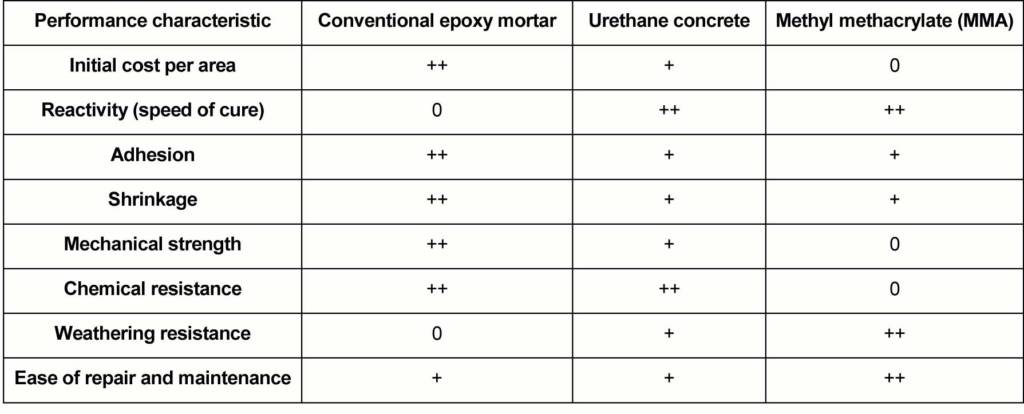
Figure 1 offers a comparison of critical performance characteristics among these flooring systems. Each characteristic contributes in some way to the downtime, labour, and longevity factors that enter into the flooring selection process. Such details, combined with this discussion, help design/construction professionals decide on the most appropriate flooring system for a given project.
For example, one may opt to trade the potentially faster return to service possible with an MMA system for the added longevity of a urethane concrete system. Doing so may slightly increase the initial flooring application time, but it could also significantly increase the flooring maintenance interval, which means less downtime later (see “Reducing Future Downtime”).
When considering the cost of each system, the initial cost per square metre does not reveal the full picture. Factors such as application time, odour-mitigation setup, maintenance intervals, curing time, and longevity all enter into the equation, making it difficult to ballpark true flooring costs without having a detailed conversation between the owner, applicator, and coatings manufacturer.
For example, while epoxy mortar systems have the lowest initial cost per square metre, they also have the slowest curing time. If the facility chooses a faster-curing—and higher-cost—MMA or urethane concrete system instead, it will experience a faster return to service, which could mean a faster return to earning profits that will more than make up for the price premium of an MMA or urethane system.