Galvanneal coatings versus galvanize coatings
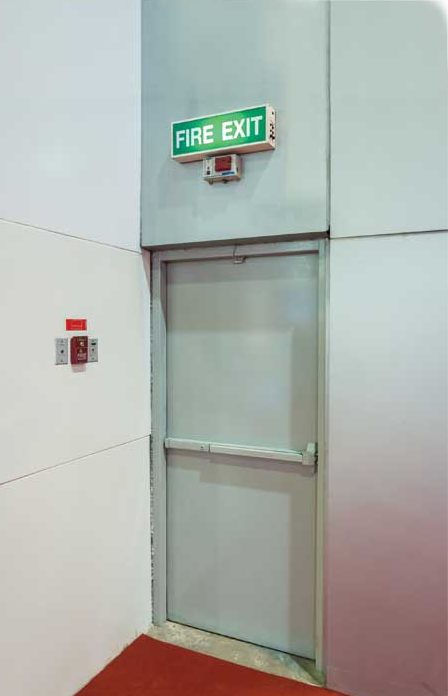
By Gary Dallin, P.Eng.
The continuous hot-dip coating process for steel sheet products—like the door on the left—is widely used and employed in all corners of the globe. Most users of continuously hot-dip coated zinc-coated steel sheet (i.e. galvanize) think of it as a product with a bright, silvery metallic sheen. However, there is a version that has a dull, matte appearance—it is called galvanneal. While both are made by the same process (Figure 1), the main difference in producing a hot-dip galvannealed coating and a hot-dip galvanized coating is an additional step in the production process.
By making a galvannealed coating, the strip, with its still liquid zinc coating, is further heated by passing it through a furnace directly above the coating bath. Heated to approximately 538 to 565 C (1000 to 1050 F), and by holding the strip at this temperature for a specific amount of time, the zinc coating alloys with iron through diffusion between the molten zinc and iron from the steel strip. The result is a coating that is an alloy of approximately 90 per cent zinc and 10 per cent iron. The iron percentage varies throughout the coating thickness, from as low as six per cent at the surface, to as high as 23 per cent at the steel interface.
Galvanneal coatings have no free-zinc present and a low-lustre matte appearance, versus the metallic sheen of galvanized coatings. The final bulk iron concentration depends mostly on the heating cycle, since the rate of diffusion is primarily a function of time and temperature. The zinc and steel chemistries can also affect the alloying behaviour, but are secondary to the heating cycle.
Coating composition
A galvanize coating is essentially pure zinc, with between 0.20 and 0.50 per cent bulk aluminum, which is mostly concentrated in a thin inhibition layer next to the steel. The aluminum does not affect the corrosion performance, but rather enables good coating adhesion, which is required when the coated sheet is eventually formed. Galvanneal coatings contain nine to 12 per cent bulk iron, along with the above-mentioned aluminum, which becomes more uniformly spread through the coating thickness than in the case of galvanize. However, it is not uniformly distributed—rather, it is combined with zinc in three distinct zinc-iron phases (Figure 2). It is also important for good appearance and press formability the top zeta layer contain no less than five per cent iron or there will be a risk of free-zinc on the surface. The higher bulk aluminum content through the three alloy layers is a result of its diffusion outward from the inhibition layer next to the steel where it was concentrated prior to the reheating cycle.
Galvanneal coatings are hard and brittle, so during bending and press forming, coating cracks and powdering are always present to some degree. To balance performance in forming versus coating line throughout, each coating line must develop practices to produce the optimal coating properties for the product’s particular use.
Production of galvanneal
To produce galvanneal, a moving sheet is immersed in the zinc bath and a thin, aluminum-bearing, inhibition alloy layer forms at the zinc-steel interface (Figure 3). As the strip emerges from the bath it drags excess zinc with it, which the air knives remove to obtain the desired coating weight. The strip, with the still liquid zinc coating, enters the galvanneal furnace about 3 to 4 m (10 to 15 ft) above the gas wiping knives.
Before the zinc can solidify, reheating of the strip begins. As the temperature rises, a zinc-iron diffusion reaction restarts and breaks down the aluminum-zinc-iron inhibition layer formed in the zinc pot at the steel-zinc interface. After five to seven seconds of heating, and up to about 10 seconds of soaking, enough iron diffuses into the coating to convert it to a dull matte grey appearance.
Since the early 1990s, coating lines have used induction galvanneal furnaces. Typically, they have three or more zones, which can reheat the strip from about 463 C (865 F) to as high as 565 C (1050 F) in the few seconds available. Older galvanneal coating lines use gas-fired furnaces, making it difficult to obtain a well-controlled alloying reaction. Induction galvannealing is inherently different than gas-fired convection or radiation versions because the heat for diffusion comes from within the strip for the former, not externally as with the latter.
Following the heating furnace zones, an electrically heated holding zone is used to optimize the iron content of the coating. The reactions that convert a liquid zinc coating to a solid zinc-iron coating begin at the steel interface and depend on factors, including:
- heating time and temperature percent aluminum in
the coating; - coating bath temperature, steel grade; and
- coating weight, and line speed.
These variables are not necessarily independent, and each coating line has to determine the protocol to produce a product for a particular use. For instance, a higher aluminum in the coating requires a higher reheating temperature or a longer soak time. Too high a temperature or too low an aluminum will result in high iron and excess powdering. Stabilized interstitial-free, ultra-low carbon grades react faster than plain carbon steel, and steels with higher phosphorous levels react slower in the galvannealing furnace than low phosphorous steels. (Figure 4 is a schematic representation of the galvannealing process. (Figure 5 depicts the stages the coating goes through during its conversion from zinc to zinc-iron.)
Coating weldability, paintability, formability, and adherence
The benefits of using galvanneal over galvanize are improved spot-weldability, ease of painting, and coating adhesion.
Weldability
Zinc-iron alloy coatings generally have better spot-welding characteristics than pure zinc coatings. The coating’s higher electrical resistance, along with its higher hardness and melting point, allow good welds to be obtained at lower currents with longer electrode life to the extent galvannealed sheet spot-welds very much like cold-rolled sheet.
Paintability
Performance of galvanneal under paint is synergistically improved because of the excellent bond formed between the paint and surface of the coating. The reason for the good bond is because the paint can mechanically lock with the zinc-iron crystals on the surface, in addition to any chemical bonding that may occur (Figure 6). This surface is why galvanneal coatings can be painted directly without the need for a primer. Compared to galvanize, galvanneal generally exhibits less undercutting corrosion beneath paint at exposed edges, scratches, or other breaches in the paint. To achieve maximum corrosion protection, galvanneal is usually treated with zinc phosphate before painting.
The specified slider id does not exist.