Meeting the National Energy Code requirements with masonry
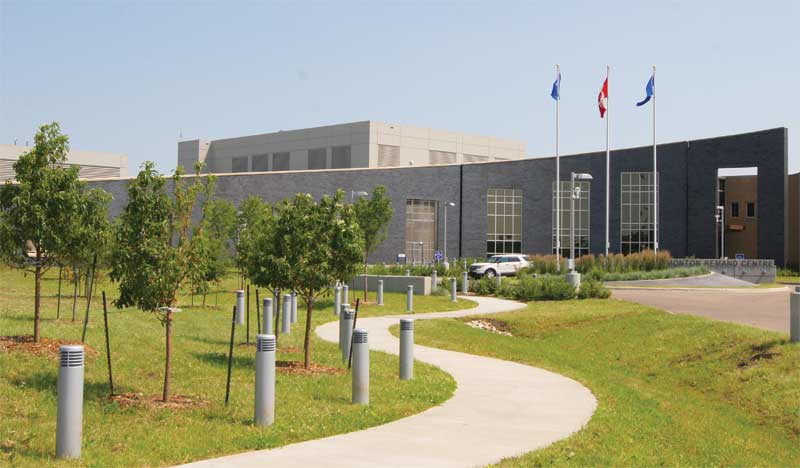
By Mark D. Hagel, PhD
Masonry is a 5000-year-old building technology proven to perform well in all types of built environments, given its inherent resistance to fire, insects, and moisture degradation. However, the expectations for buildings have grown from simply providing shelter to maximizing use of renewable, recycled, and recyclable materials, as well as space, energy, sound, and light. This historically used technology must adapt to meet modern construction requirements, including high RSI/R-values, effective moisture management, and more efficient use of space.
Canada’s National Energy Code for Buildings (NECB) was released in 2011, and updated last year. In Alberta, the 2011 NECB requirements became effective as of last month, while Ontario has already developed its own version of the energy code. This article explores techniques to meet the NECB requirements using the trade-off compliance path. It also discusses a masonry innovation that could address increased thermal performance demands using insulated structural masonry products with the potential to preserve single-wythe concrete masonry unit (CMU) construction.
NECB tradeoff system
The 2011 NECB allows for tradeoff between opaque wall and less-energy-efficient fenestration and door components. By comparing the energy consumption requirements for door and walls provided by the code to the actual building’s wall and fenestration components, the required RSI-value of the opaque wall can be reduced if the fenestration-and-door-to-wall ratio (FDWR) is sufficiently low.
An example would be a Calgary office building that has an elevation as presented in Figure 1. The number of heating degree days (HDD) for this location is 5000, which yields an FDWR of 0.333 (i.e. 33.3 per cent). For this location, opaque walls are required to have a U-value of 0.210 (i.e. RSI 4.75 [R-27]) while the fenestration and doors must have a U-value of 2.2 (i.e. RSI 0.46 [R-2.6]). Put simply, if the building under consideration located in Calgary has 33.3 per cent of the wall area comprising glazing and doors, with an average RSI of 0.4587 (R-2.6), then the opaque wall RSI required is 4.76 (R-27).
The dimensions for the total wall of the elevation in Figure 1 translate to a wall area of 43.9 m (144 ft) by 13.4 m (44 ft), yielding a total wall area of 588.63 m2 (6336 sf). The window bands are 7.09 m (23 ¼ ft) wide by 1.6 m (5 ¼ ft) tall. On the main floor, there are 2.6-m (8 ¾-ft) tall doors and windows. The total fenestration area for this elevation translates to an FDWR of 0.243—that is, 24.3 per cent of the wall area is glazing.
Utilizing typical RSI values for thermally broken, double-glazed aluminum windows and doors of 0.387 (R-2.2) translates to a required RSI of 3.17 (R-17.7) for the opaque walls. Figure 2 shows the energy balance calculation. This goal is quite achievable with traditional 90-mm (3 5/8-in.) brick veneer, a 100-mm (4-in.) steel stud backup wall, and 76 mm (3 in.) of extruded polystyrene (XPS), which yields an effective RSI value of 3.28 (R-18.6). (For more information on these calculations and analysis, visit the Alberta Masonry Council’s website at www.albertamasonrycouncil.ca/wall-test.)
In addition to trading efficiencies between wall components, the NECB section of the National Research Council (NRC) website states that the code:
allows you to trade enhanced energy efficiency of one component against decreased energy efficiency of another component within the same part of the Code. For example, in Building Envelope (NECB Part 3), higher roof insulation efficiency levels can be traded off against lower wall insulation levels, but not against lighting levels, which are included under Lighting (NECB Part 4). (To read more on this visit www.nrcan.gc.ca/energy/efficiency/buildings/eenb/16598.)
Therefore, increasing roof insulation can also facilitate the use of lower R-values in the opaque wall. In this example, increasing the roof insulation sufficiently could reduce the wall insulation from 100 to 50 mm (4 to 2 in.).
For multi-family residential buildings, fenestration ratios are often higher than 25 per cent. Figure 3 shows the front elevations of a wood-frame, brick-clad low-rise residential building in Edmonton. For this elevation, the FWDR is 0.328 (i.e. 32.8 per cent). Assuming vinyl with a spacer is being used, most windows and doors have an RSI value of 0.511 (R-2.8), and the opaque wall will require an RSI value of 3.33 (R-18.9), as shown in Figure 4. This can be achieved using traditional 2×6 wood-frame construction with R-19 batt insulation in the stud and 25 mm
(1 in.) of expanded polystyrene (EPS) in the cavity. This yields an effective RSI value of 3.77 (R-21.4), as shown in Figure 5.
For buildings like warehouses and light industrial projects, the fenestration ratio are often significantly lower than 30 per cent. Figure 6 displays two elevations of a typical warehouse.
On Elevation I, the Fenestration wall ratio is 0.180 (i.e. 18 per cent); on Elevation II, even with the large bay doors and man doors, the FDWR is only 0.101 (i.e. 10.1 per cent). Assuming the typical RSI value of 2.64 (R-15) for insulated metal man doors, and 0.405 (R-2.3) for the large bay doors and glass windows and doors, yields
RSI requirements of 1.90 and 1.29 (R-10.8 and R-7.3) for Elevation I and Elevation II, respectively.
An alternative to using two separate insulation values for the two elevations would be balancing the R-value by taking an effective RSI value of 1.57 (R-8.9) for both. However, neither of these insulation requirements can be met with a single-wythe CMU wall using a typical 200 or 250-mm (8 or 10-in.) concrete block—even when filled with vermiculite or sprayed polyurethane foam (SPF) as shown in Figure 7.
To achieve an RSI value that is greater than 1.14 (R-6.5) with a single-wythe masonry wall, insulated concrete unit technologies are required. The next section describes some of the technologies already available in the market that can achieve RSI values between 1.41 and 4.93 (R-8 and R-28) with a single-wythe wall.
The specified slider id does not exist.