Improving continuous insulation
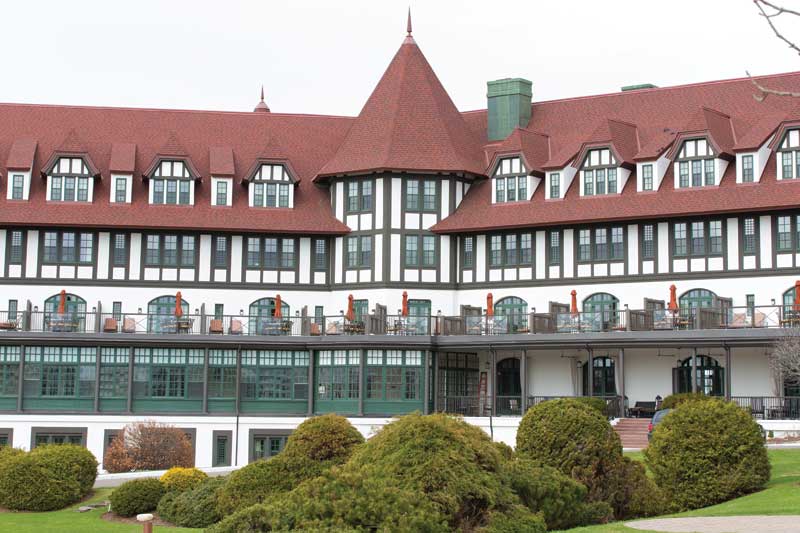
By John R. S. Edgar
Insulation manufacturers have devised numerous ways to improve the thermal performance of their products, from adding specialized particles to polystyrene to refining vacuum insulated panels (VIPs) and phase-change materials to aerogels. Unfortunately, none of this matters when these high-performance products are installed ineffectively. Batt insulation between steel studs loses half its R-value. Steel studs themselves act like ‘radiator fins’ to the exterior—along with shelf angles and structural connections, they are a prime example of a thermal bridge.
New research, using computer modelling, has shown thermal bridging through insulation is a far more serious problem than previously suspected. The accepted solution is continuous insulation (ci) outbound of the studs. Canadian code-writers have taken note—the National Energy Code for Buildings’ (NECB’s) focus has shifted to the building envelope’s passive performance, limiting reliance on powered mechanical systems in the alternative path options.
In some ways, the new design battlefront will be about energy conservation versus gravity. In all methods of construction, the cladding dead load must be secured to the structure through the ‘continuous’ insulation. If thermal bridging is eliminated, what will hold the cladding to the structure? Currently, stainless steel channels, fibreglass clips, and composite assemblies with built-in thermal breaks are being rolled out to support the cladding.
Over and above the structural penetrations, what will hold the continuous insulation in place? With some types of insulation, adhesives do the job. With others, screws with washers are required to secure the insulation to the supporting structure. Typically, in thermal energy calculations, the screw shaft diameter is compared to the insulation area, yielding a thermal bridge ratio of about 0.05 per cent—a seemingly insignificant amount. In fact, a thermally conductive screw shaft transmits heat from an area many times larger than its diameter (Figure 1).
Thermal bridging through every fastener cools the interior temperature by radiating heat out of the wall. If the temperature of a fastener tip is below the dewpoint, the result may be condensation and potential corrosion—not good for long-term durability and resilience. To combat these drawbacks, there are now inventively designed fasteners that have reduced thermal conductivity and are corrosion-resistant. Fortunately, designers no longer need to deal with bridge-by-bridge calculations. Much simpler and more accurate methods have been developed to design code-compliant building enclosures.
With the energy modelling discussed in this article, the starting point in the calculation is a ‘clear wall’—that is, an area of opaque wall devoid of major thermal bridges. The ‘clear wall’ value is determined by guarded hotbox calculations. Insulation fasteners are included as part of the ‘clear wall,’ so their effect is included in the base calculation. Essentially, there is no need to model every fastener. However, if a particular design is running close to the unacceptable mark, something as trivial as fasteners may require examination.
Calculating thermal performance
The way a building envelope’s thermal performance is calculated has changed, thanks to more powerful computers and an amazing degree of sophisticated modelling. The same computer simulations that model heat shield performance during spacecraft reentry, for example, are also used to determine heat loss through a floor slab.
Prior to advanced computer simulations, the parallel approach to heat loss calculations was used. For a slab penetration, the energy flow through both wall and slab was calculated based on the elevation area (Figure 2). The wall and slab energy flows were added together, based on the ratio of wall-to-slab area. Any lateral flow of energy was ignored.
The reality is that energy moves in all directions and a cold, uninsulated slab will draw heat not only from the slab, but also from interior air and the wall assembly above and below the slab (Figure 3). Wall insulation is rendered less effective because heat flows around the insulation and out the slab. The problem has been how to calculate the energy end run accurately.
The specified slider id does not exist.
In July 2011, Toronto-based engineering firm Morrison Hershfield Ltd. presented a paper to the American Society of Heating, Refrigerating, and Air-conditioning Engineers (ASHRAE) showing how advanced computer modelling could accurately predict heat flow through thermal bridging. (The firm’s “Thermal Performance of Building Envelope Details for Mid- and High-Rise Buildings [1365-RP]” was presented to ASHRAE Technical Committee 4.4 on July 6, 2011.) This research evaluated thermal performance data of 40 common building envelope details for mid- and high-rise construction. The modelling was validated by 29 guarded hotbox measurements. The goal of this research project was to modify the energy calculation methods described in ASHRAE 90.1, Energy Standard for Buildings Except Low-rise Residential Buildings.
The paper introduces a simpler, but accurate, way to calculate the effect of thermal bridging. Rather than calculate the cross-sectional areas of building elements and work out heat loss per area, modellers only have to measure the length of the thermal bridge (e.g. the length of the deck or perimeter of a window) or identify point sources (e.g. a penetrating structural beam). Each element has a thermal transmittance value already determined by the research. Linear transmittance is measured in W/(m•K) and point flow is measured in W/K.
The opaque wall, or ‘clear wall’ as described above, for which the thermal transmittance value has been predetermined and validated, is measured in W/(m2•K). As an example, all components of an insulated stud wall—air films, studs, batts, sheathing, insulation, cladding, and fasteners—are included.
Thus, to calculate the thermal bridging effect of a cantilevered balcony, the length of the balcony at the wall interface is multiplied by the linear transmittance value. This number is then divided by the area of the wall, before adding the increased thermal transmittance to the ‘clear wall’ value. If a whole elevation is calculated, then the lengths of all balconies, windows, doors, shelf angles, and other linear penetrations are added. Point penetrations are also calculated and added. Once all the values are added to the ‘clear wall’ value, the result should be the total effective assembly thermal transmittance.
The complete method is described in Morrison Hershfield’s Building Envelope Thermal Bridging (BETB) Guide (Version 1.1), (The BETB Guide was published by BC Hydro Power Smart earlier this year.) which is based on research done for ASHRAE, plus additional research funded by a number of industry partners, including the Exterior Insulation and Finish Systems (EIFS) Council of Canada. (See Table 1 of the 2014 “Thermal and Whole Building Energy Performance of Exterior Insulated Finishing Systems Assemblies,” Report No. 5130962.00, by Morrison Hershfield Ltd. Visit www.eifscouncil.org.) The method, compared to previous data manipulations, is elegantly simple. The result, compared with what is allowed in a local building code, may be surprising to most design/construction professionals.
In fact, the real fun of determining the effective thermal transmittance of a proposed building begins when one realizes it does not comply with local codes. That dilemma will increase as different code bodies start stretching their codes to meet the demand for more thermally efficient buildings. At that point, designing and building to eliminate thermal bridging will get serious.