Thinking Zinc: Examining the cladding options
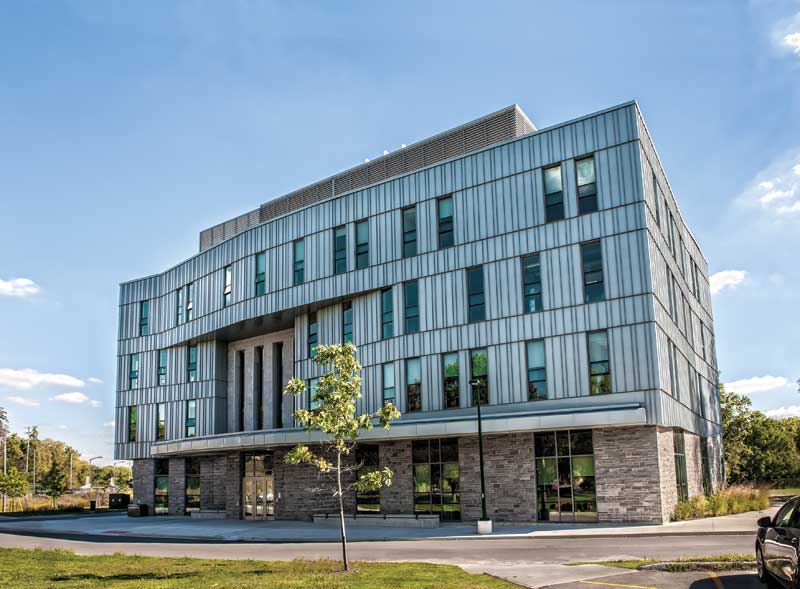
By Peter Gatto and Charles “Chip” McGowan
This article examines some of the advantages, characteristics, and cladding choices that ‘zinc’ (or, more accurately, architectural rolled zinc) offers the built environment. The material is a mixture of titanium, zinc, and copper; essentially, it is an engineered, non-ferrous metal alloy of high-grade zinc. For more than 200 years, zinc has been utilized by European designers and craftsmen to clad structures that have endured for generations. Since at least the early 1990s, it has also been recognized in Canada for the significant value offered as a cladding material.
From an owner’s perspective, one value of using zinc is its longevity. The life expectancy of a roof is anywhere from 80 to 100 years while a wall can last as long as a century and a half. Since zinc is a natural material, it weathers according to its environment. When exposed to wetting and drying cycles, the surface will slowly develop a natural patina comprised of zinc carbonate (ZnCO3) or zinc hydroxide in a marine environment. The patina is a thin outer layer that protects the underlying alloy and ensures its long life.
The formation of the patina is a process of the gradual growing together of patinated ‘freckles,’ while its formation rate is related to the slope of the surface and exposure to moisture. The patina forms faster on a slightly pitched roof than on a vertical wall surface. Ultimately, the natural patina forms to a uniform colour—an essential esthetic difference from painted surfaces. The slope-related patination speed can vary between six months and five years, depending on climatic conditions. The more exposure to wetting and drying cycles, the quicker it develops.
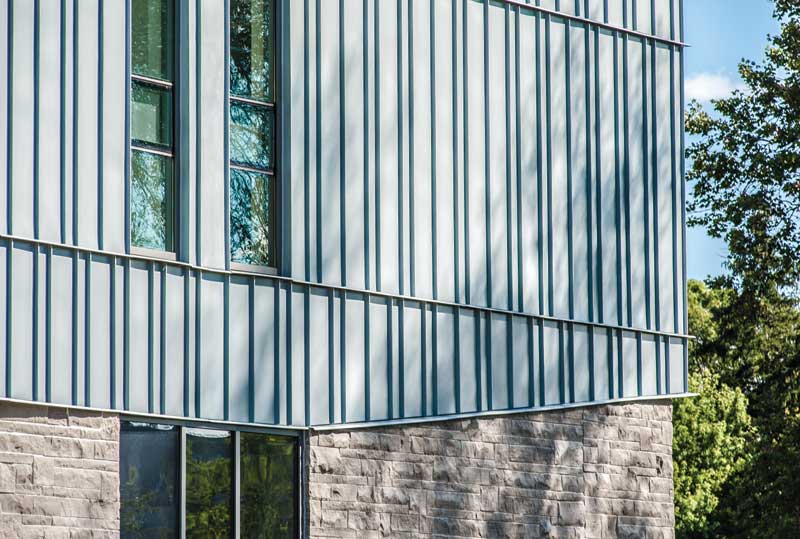
Advantages of zinc
Zinc is a ‘sacrificial’ material. When scratched, scuffed, or fingerprinted, the metal heals itself by re-patinating, through exposure to water and drying, to match the surrounding metal—with time, it blends so the scratch disappears. This is important when exposed surfaces such as bare edges form the grey patina, reducing the need for touch up paint or edge coatings as the patination process will take over.
While the patina colour is determined by the composition of the alloy and the environment (or compounds present in the air and environment), it is possible to have slight variations from coil to coil, panel to panel, or within an individual sheet or panel surface. Owners, architects, and installers should be aware and expect possible variations that will even out over time—as is the case for many other construction materials exhibiting tonal variations. However, variations will dissipate as the material goes through wetting and drying cycles, developing its natural patina.
Zinc may be employed inland or in marine environments. Roofing comprising the material has been used for more than 100 years in coastal climates, with numerous examples of old European zinc roofs still in existence.
The durability of zinc as roofing, roof drainage, and cladding material is inherent in the material itself; it can be attributed to the ability to form a protective patina that prevents the zinc from oxidizing.
The patina also makes it possible for low to no maintenance needs over the life of the material. Other benefits to using zinc include ease of fabrication, clear rainwater runoff, and its ability to be recycled an infinite amount of times without the loss of properties.
Based on known ore reserves, the world’s zinc supply is expected to last 700 years; scrap is also eliminated through recycling. The material has a low primary energy content (embodied energy) compared to other architectural metals. The primary energy required to produce zinc coils is 3610 kW hours per tonne, which is substantially less than most metals. This is because the concentration in zinc ore is higher than other metals in their respective ores. It is also due to the fact zinc has a relatively low melting point—about 418 C (785 F)—and requires a relatively low level of fuel to extract, smelt, alloy, roll, and fabricate the metal. By comparison, the melting point of zinc is about two-thirds that of aluminum and a third that of copper or steel.