Spec Matters: Concrete floors, concrete success
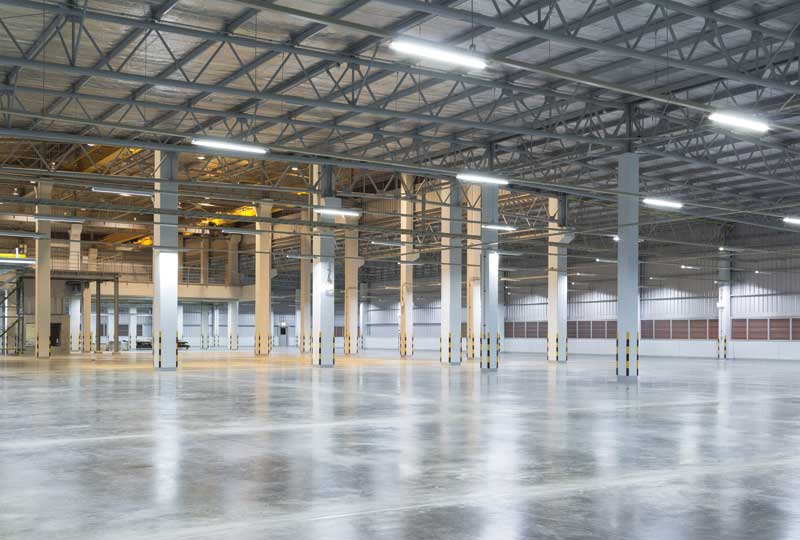
By Geoff Kinney
“Look out everyone—the inspector is coming!” Whether it is an owner’s representative, a construction manager, or a ministry official, there always seems to be a heightened sense of duty and care when inspectors are on the job. It is natural for everyone to step up his or her efforts to do what is right when their work is being inspected.
Considering the substantial effort that goes into the design and creation of project plans and specifications, one would think there would be an equal desire to ensure they are followed. However, some people believe inspection offers little value; they feel it is troublesome, inconvenient, disruptive, and an expense to be minimized. Others embrace inspection openly as a means of avoiding problems and ensuring specified quality.
In this author’s opinion, site inspection plays a critical role by ensuring:
- specification materials and methods compliances;
- building code and CSA standards compliances;
- fair competition through equal performance;
- a focus on quality planning and problem avoidance;
- accurate execution of the work;
- better surface tolerance results;
- an accurate as-built historical record; and
- maximum quality, performance, and value for the client.
In the darkest parts of the construction industry, unethical contractors flourish by ignoring specification requirements to pursue the cheapest cost materials substitutions with an almost total disregard for performance. A lack of inspection not only permits this type of behaviour, but also encourages and rewards such practices. It remains a great injustice to honest contractors they must compete against unethical firms. In an effort to promote competition based on equal scopes of work, the Concrete Floor Contractors Association (CFCA) has defined a standard scope of work for its industry.
A not-for-profit voluntary membership organization, CFCA is determined to advance quality and integrity in the concrete floor industry. Contractor members are required to follow a code of ethics, participate in annual education, and to undertake preconstruction quality planning on every project. The specified prequalification of CFCA contractors helps promote this focus on quality and ethics across the entire concrete floor industry.
Sources, standards, and specifications
Concrete floor slab-on-grade trade contractors are high-volume production experts. A single concrete floor crew can install more than 2000 m2 (21,530 sf) of slab-on-grade in a day. Larger firms, with multiple crews, can place upward of 50,000 m2 (538,200 sf) in a week! With this very high productivity, there is a need for inspection to ensure a focus on quality as well.
As trade contractors, quality planning is often limited to contractual responsibilities. The construction of a slab-on-grade concrete floor is commonly divided amongst a number of different contractors and materials suppliers (i.e. ‘divided-source’ responsibilities). Any breakdown in communication, co-ordination, or ethics between these parties can result in reductions in quality and other potential problems. It is recommended specifiers include the need for a concrete floor pre-construction meeting to ensure specification and standards requirements are understood, and that adequate quality planning, communication, and co-ordination occurs between these parties. In fact, CFCA recommends a ‘single-source’ approach to construction responsibilities for complex surfaces such as architectural finishes, rink slabs, bonded toppings, and superflat concrete floors.
The Canadian concrete standard—CSA A23.1-2014, Concrete Materials and Methods of Concrete Construction, defines numerous requirements and tolerances that must be met. Many of these tolerances are not written in project specifications and can be overlooked. The obvious benefits of following standards requirements are to minimize problems and to improve quality and hardened performance. Non-compliance with CSA A23.1-2014 includes the risks of lower unknown performance, abnormal set problems, and contractual liabilities.
It is critical to have good-quality concrete materials in order to obtain good-quality hardened performance. For example, when it comes to interior trowel-finished concrete floors, CSA A23.1-2014 requires use of a concrete mix with a maximum 0.55 water cement (w/c) ratio. This 0.55 w/c ratio is the minimum quality necessary to produce a trowel-finished concrete surface that has good hardened performance qualities. The use of substandard concrete materials is at the cost of hardened performance, reduced wear resistance, increased drying shrinkage curling, and other problems. The ‘concrete purchaser’ plays a critical role by ensuring specifications and standard requirements are met.
Project specifications commonly reference CSA A23.1 for floor surface tolerances, yet very few floors actually get measured. This has created an environment where some floors meet specified requirements and others do not. It is impossible to know whether the specified floor tolerances have been achieved unless the ‘as-built’ tolerances are actually measured. A lack of floor tolerance measurements creates an environment where inconsistent results should be expected.
Mandatory testing can be overlooked as well. CSA A23.1 requires plastic air testing of all concrete materials when casting compressive strength cylinders, yet this testing is often not performed. Plastic air testing is critical to ensure:
- exterior air-entrained concrete mixtures will have adequate air for freeze-thaw resistance, and
- interior non-air entrained concrete mixes have less than three per cent air to avoid surface delamination problems when trowel finished.
A lack of plastic air testing can permit improper and incompatible concrete to be placed and finished. It is important to note some polycarboxylate mid-range plasticizers can increase plastic air contents above three per cent. For interior slab-on-grade concrete mixes, it is recommended the first load of concrete be inspected to ensure air compliances from the beginning of every placement.
Inspection and testing companies offer a variety of services to assist owners with quality assurance (QA). Full-time inspection can be accommodated easily by adding a person to monitor the concrete-placing activities. The small cost of one inspector per slab-on-grade placement can make all the difference between achieving good or bad hardened floor performance.
Conclusion
At a minimum, inspections should identify if specified materials are being used and that CSA A23.1 requirements are being met. This author strongly recommends owners invest in full-time inspection on concrete slab-on -grade placement days to maximize quality, reduce problems, and obtain the highest value for their building investment.
Project specifications commonly reference CSA A23.1 for floor surface tolerances, yet very few floors actually get measured.
SLAB-ON-GRADE INSPECTION CHECKLIST |
A partial list of slab-on-grade inspection items includes:
|
Geoff Kinney has more than 20 years of experience as a concrete floor trade contractor. He has been the executive director of the Concrete Floor Contractors Association (CFCA) and the Cement Finishing Labour Relations Association since 2007. Kinney can be reached via e-mail at gkinney@concretefloors.ca.