Eastern Ontario hospital overcomes waterproofing challenges
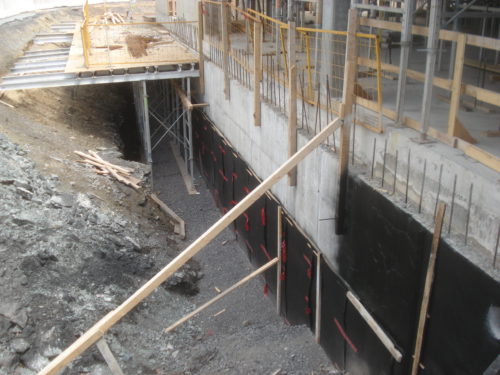
Images courtesy W.R. Meadows
Hawkesbury District & General Hospital (HGH), located halfway between Ottawa and Montréal, is in the midst of an ambitious long-term construction project, first submitted to the Ontario Health Ministry in 2007. The project features a pair of three-storey additions with basements, to be appended to the existing hospital. This is part of a $120-million investment, which will also fund more beds (to add to the existing 100), expanded healthcare services, and updated diagnostic equipment.
In order to complete these additions, designers and builders had to overcome some very complex problems. First, below ground level, there was a substrate composed of solid rock with gravel on the top. Any groundwater that accumulated on top of this would have nowhere to go unless it seeped through the building’s concrete, causing damage to the structure.
The general contractor, Bondfield Construction, solved this problem by laying composite sheeting over the ground covering the additions’ footprint—an area spanning 4459 m² (48,000 sf). According to Scott Watson, the superintendent appointed by Bondfield, this sheeting was used under the entire basement floor, generating much better results than polyethylene or plastic.
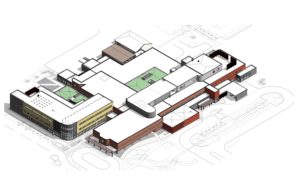
To circumvent the danger that groundwater buildup could also affect the foundation walls, waterproof sealant and a drainage system were used in combination. The sealant, which was cold-applied directly onto the concrete, is a single-component waterproofing membrane that is water-based and polymer-modified. It covers tiny cracks and holes in the wall, ensuring it is fully sealed and protected.
Once this was applied, a rolled matrix drainage system was installed, with geo-composite makeup that both allows the passage of moisture through the fabric and prevents fine soil from entering the drainage channel.
“When the groundwater flows toward the foundation, the dimples in the [drainage system] catch it. Gravity then pulls the water down toward a drainage pipe and it then flows away from the building,” explains Watson.
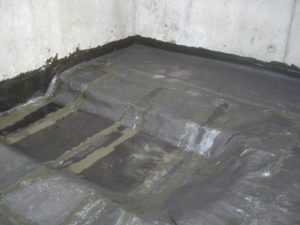
Work was also impeded by a long cliff of underground rock too big and expensive to remove, found during the excavation process. The concrete foundation had to be poured directly against this rock, meaning normal waterproofing materials could not be applied. The Bondfield team solved this problem with the creative approach of ‘reverse-engineering’ its materials.
To do this, the team simply flipped the usual order of their waterproofing steps. First, sheets of the drainage system were applied directly against the rock. Those sheets were then sprayed with sealant. From here, all that remained to complete the waterproofing process was the pouring of the concrete foundation wall.
Thanks to this innovative use of materials, the hospital’s additions are rapidly nearing completion—but there is still other work to be done before HGH can achieve its goal of becoming a full-service regional hospital by the end of 2018. Watson, who has been on the site since construction began in 2014, says smaller additions and renovations will continue for two more years.