Innovation in the wood finishing industry
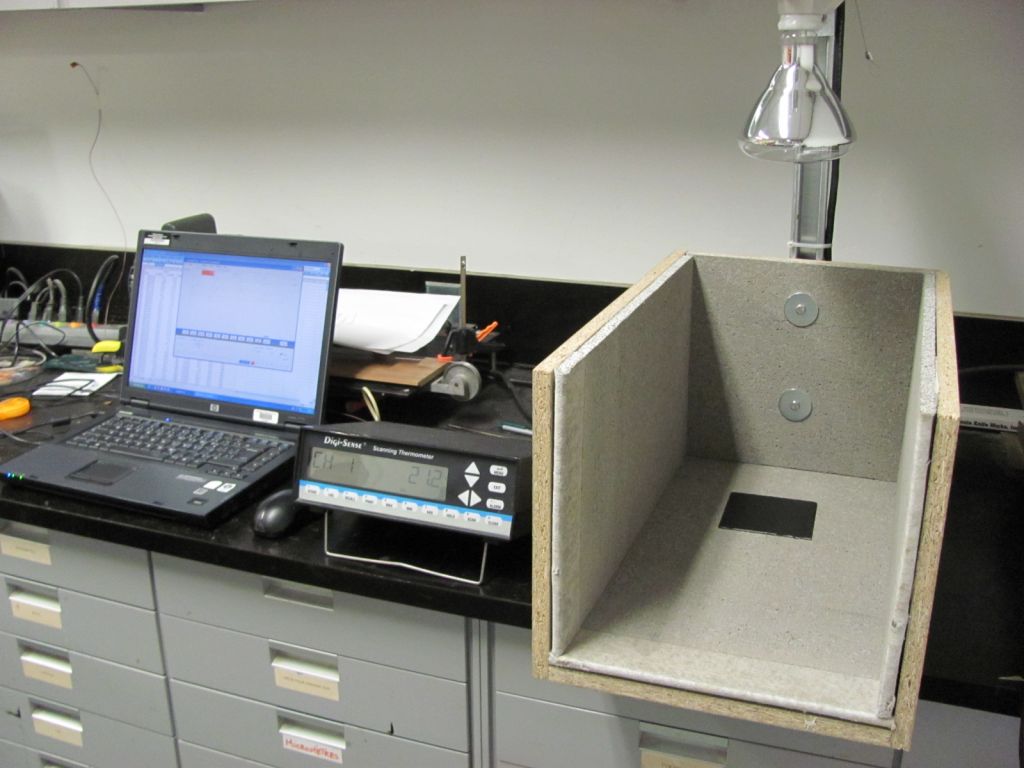
By Véronic Landry, PhD
Wood product finishes wage ongoing battles against the elements and daily use. Observing the many applications of interior and exterior wood products, and the various temperature and humidity conditions in which they need to perform, it is no surprise new, specialized finishes regularly hit the market. The challenge to reduce volatile organic compounds (VOC) and formaldehyde emissions also contributes to coating development.
Coatings are liquid, liquefiable, or mastic compositions applied as thin layers on a substrate (i.e. wood, plastic, metal) that convert after drying or polymerization into solid adherent films. Traditionally, demands ranged from extended service life, low maintenance cost, and colour (or lack thereof), to ultraviolet (UV) protection, waterproofing, good surface mechanical performance (i.e. hardness, scratch, and wear resistance), and chemical resistance. To keep up with future demands, as well as maintain competitiveness, the wood finishing industry is transforming by looking into greener products, along with innovations coming from other industries such as metal, plastics, or glass.
Various types of wood coatings have been studied and developed for exterior (e.g. construction, patio, doors, windows, siding, shingles) and interior products (e.g. flooring, furniture, kitchen cabinets, wall panels, mouldings). Recently, the focus has been on:
- low-VOC interior and exterior coatings;
- interior and exterior bio-based products (from renewable raw materials); and
- smart coatings fitting the industry’s future needs.
Interior coatings
Low-VOC products are increasing in number and now include solvent-based coatings containing less listed VOCs or hazardous air pollutants (HAPs). Some also include bio-based solvent content. Formaldehyde-free solvent-based coatings are also hitting the market. Classified as a known human carcinogen, formaldehyde is defined as a toxic air pollutant subject to regulatory action by the Clean Air Act Amendments and it is considered by the U.S. Environmental Protection Agency (EPA) as a major toxic constituent of smog. (In Canada, there is currently no regulation as precise as that of EPA.)
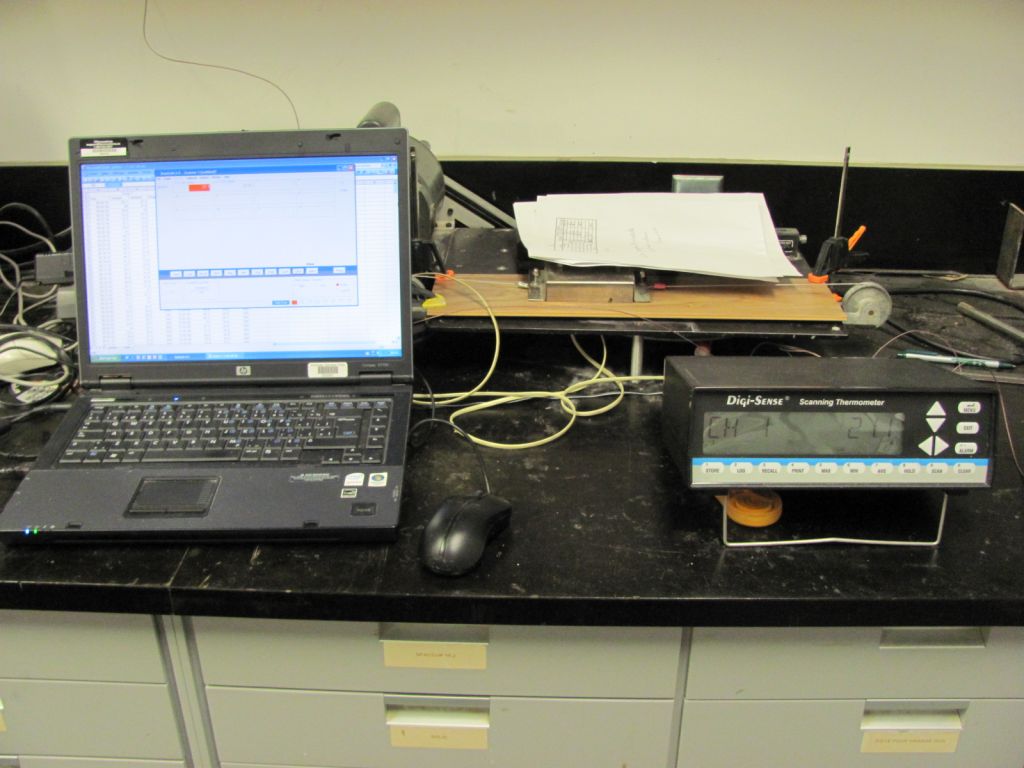
Water-based interior coatings have also improved to offer:
- higher clarity;
- less milky or hazy aspects;
- lower grain-raising;
- decreased drying times; and
- overall better mechanical and chemical performance.
Wood coating manufacturers are in the second or third generation of water-based products. With the recent water-based resin innovations and developments taking place, current water-based coatings are far ahead of their predecessors.
In the past, the wood flooring industry was the major beneficiary of the performance of UV-curable coatings. Now, water-based UV-curable interior coatings composed mainly of resins and photo-initiators (i.e. molecules that split in two when exposed to UV light and form radicals starting the polymerization process), can be industrially applied and cured, or applied onsite and cured using handheld or rolling portable UV-light machines.
The benefits of UV coatings include:
- fast UV-curing;
- enhanced finished product’s mechanical, chemical, and thermal properties; and
- inflammable.
Traditionally, UV-curable finishes were only used in flooring or wall panels. However, with the advent of water-based UV-curable coatings—especially the novel dual-cure UV coatings using hybrid technology—it is now possible to use these coatings on wood products with complicated shapes such as chairs, guitars, mouldings, or millwork. These coatings allow surface build similar to waterborne coatings without, UVcuring, with the chemical and physical resistance of UV-curable. They polymerize under UV light and temperature (i.e. ultraviolet polyurethane dispersion [UV/PUD]) and can be applied using spray, vacuum, curtain, or roll-coating methods.
These methods are selected according to the viscosity, size, and shape of the samples being coated.
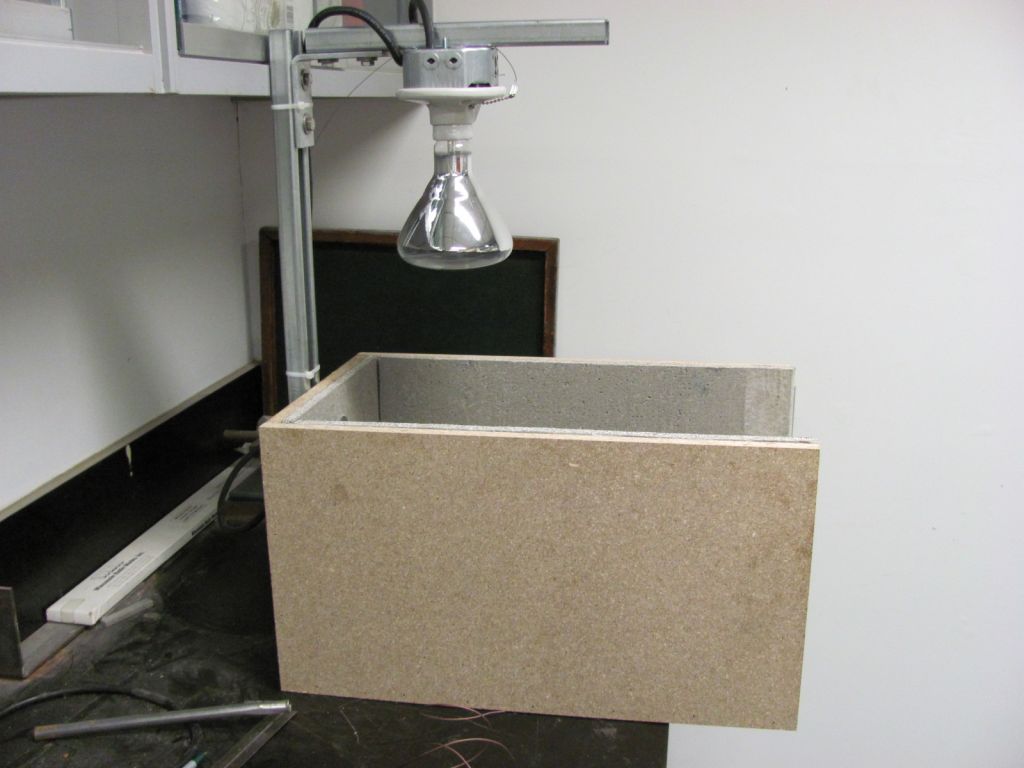
Exterior water-based coatings
With the adoption of Canadian Environmental Protection Act’s (CEPA’s), “Volatile Organic Compound Concentration Limits for Architectural Coatings Regulations,” water-based exterior acrylic coatings are gaining popularity. Two interesting innovations in these coatings include fluoro-acrylic and infrared (IR)-reflective coatings.
Over the last 30 years, solvent-soluble fluoropolymers coatings have commonly been applied on metal building siding. The carbon-fluoropolymer bond is the strongest bond in organic chemistry and enables these products to provide chemical, thermal, and UV-radiation resistance.
These coatings also comply with standards/regulations, such as American Architectural Manufacturers Association (AAMA) 2605, Voluntary Specification, Performance Requirements and Test Procedures for Superior Performing Organic Coatings on Aluminum Extrusions and Panels. However, solvent-based fluoropolymers cannot be used on wood because they must be baked on the substrate at high temperatures (i.e. melting temperature of 170 to 180 C [338 to 356 F] for polyvinylidene difluoride [PVDF]). Therefore, onsite applications are impossible.
Recent developments have enabled their use on wood in the form of water-based fluoropolymer resins (emulsions). These new resins can be dried at room temperature so they can be applied on heat-sensitive substrates, such as wood and various plastics. They can also be mixed with water-based acrylic resins—an opportunity providing the possibility to lower cost while increasing adhesion and mechanical properties. Recent accelerated aging tests have shown both semi-transparent and opaque water-based fluoro-acrylic coatings lead to lower degradation and total colour change of coated wood samples of any species, compared to acrylic coatings. Important chemical changes in acrylic coatings lead to discolouration, chalking, and adhesion loss. Using a fluoropolymer can slow the degradation as they are an inert material with little to no ability to react chemically, and seem to protect the acrylic part of the coatings.
Cool coatings (i.e. IR-reflective coatings) are prepared from pigments that reflect infrared rays (i.e. heat). They have mainly been used in hot regions on metal roofs, polyvinyl chloride (PVC) windows, and exterior siding. Using these coatings in densely populated regions reduced the urban heat island effect caused by heat-absorbing materials. In colder northern climates, the same type of resin-based systems are used, but the pigments differ.
On wood products, specifying appropriate IR-reflective coatings is expected to limit resin exudation due in part to high temperature, as well as the creation of cracks. Premature wood drying, especially on south-exposed (i.e. full sunlight) building surfaces facing greater temperatures, can cause cracks. Coating cracks are an ideal environment for the proliferation of mould. Heat is also known as a catalyst of coating degradation, by having coatings that absorb less heat, longer coating service life can be expected. Even though wood is a well-known insulating material, experiments conducted by this author’s firm have proven absorption is still significant. Results show IR-reflective pigments significantly limit heat-buildup of wood samples when exposed to IR radiation.
The effect of two black formulations on white pine samples—one prepared from carbon black pigment and another from an infrared reflective pigment—were compared in research conducted by this author’s firm. When heated with an infrared-emitting light, the samples coated with carbon black formulation presented inner temperatures 60 C (108 F) above the measured ambient temperature, while IR-reflective pigment coated samples present temperatures of 48 C (86.4 F), a difference of 20 per cent.
These results demonstrate heat absorption is much lower for the formulation prepared with an IR-reflective pigment, which can be expected to have less heat-related problems. Similar experiments were performed for other colours (including green and yellow), with similar results obtained.
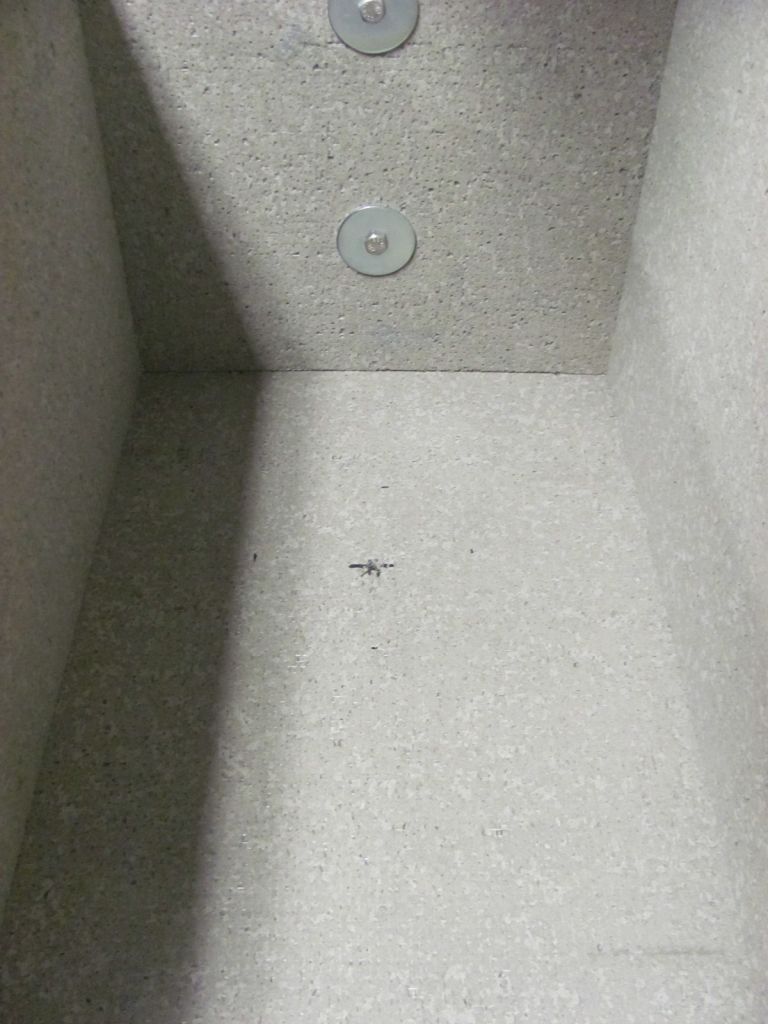
Bio-based coatings
There is growing uncertainty regarding the availability/pricing of products extracted from the study of chemical reaction involved in converting petroleum and natural gas into other materials and products (i.e. petrochemistry).
New products made for decks, floors, cabinets, and furnishings made from renewable raw material—such as soy, flax, cellulose, lipids, starch, proteins, lignin, or hemicellulose—are constantly being developed, pushed by green marketing and Leadership in Energy and Environmental Design (LEED) achievement strategies. The availability of unique chemical structures from these renewable raw materials is also pushing the industry towards these bio-based coatings.
Examples of such coatings include whey-based products and soybean oil-based coatings. Soybeans contain polyols that can be used to replace petrochemical polyesters or acrylics. Of equal interest is the development of coatings made of biological extracts, such as pinene (pine resin), and limonene (citrus) that were traditionally considered unreactive solvents. In partial replacement of monomers, rosin (pine resin), and lignin have been used.
Lignin is a complex organic compound binding to cellulose fibers, hardens, and strengthens the cell walls of plants. Lignin is a polymer consisting of various aromatic alcohols, and is the chief non-carbohydrate constituent of wood.
The large availability and lower environmental impact of these raw materials present great value. Combined with new or improved polymerization technologies, new bio-feedstock material can also mean novel characteristics such as higher UV performance and mould resistance.
Smart coatings
Smart coatings are materials structured to react to outside conditions, such as temperature, stress, or strain. Whether developed to be self-cleaning, self-healing, thermochromic (i.e. change colour depending on temperature), or electrochromic (i.e. change colour when a burst of charge is applied), they represent the future of coatings. Research projects have shown optimized self-healing solvent-based polyurethane formulations obtain significant gloss recovery and scratch size reduction (length and width) after being heated on wood products. Moreover, the process seems to be able to sustain multiple deformations for low- and high-gloss formulations.
Anti-mist, anti-dirt, and easy-to-clean coatings using balanced formulations of hydrophilic and hydrophobic nanoparticles are also being developed. Self-cleaning coatings have been around in the plastic, glass, and cement industry and are extensively used for interior and exterior products. These two types of smart coatings are of particular interest for the wood products industry.
Conclusion
Exciting and innovative improvements are constantly being developed for low-VOC interior, water-based exterior, bio-based, and smart coatings, and new products are expected to continue developing.
Véronic Landry, PhD, completed her undergraduate studies and master’s degree in chemistry, and PhD in the wood science department at the Université Laval (Québec City). She is a senior research scientist at FPInnovations—a Canadian wood research centre with her focus on exterior and interior coatings and wood surface preparation. Landry can be contacted via e-mail at veronic.landry@fpinnovations.ca.